Properties of Cotton Fibers – An In Depth Look
If you’re someone who frequently finds himself/herself busy with textile materials-whether it’s making clothes or doing other art projects- you must have encountered cellulosic materials, especially cotton. It’s the only fiber that gets used the most among other ones.
So, ample knowledge about the properties of cotton will help you to make your tasks that much easier.
Without further chit-chat let’s get it started then.
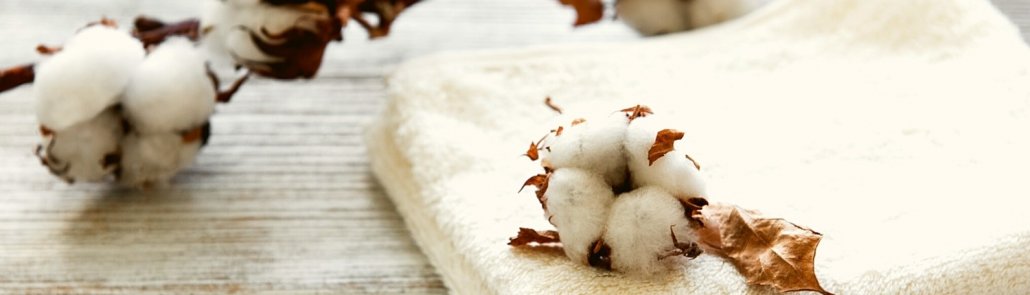
What is Fiber?
Fiber is a pliable substance like hair, and its length is one thousand times higher than its diameter.
Now, to be textile fiber, it should fulfill some specific requirements. They should have,
- Spinning power
- Dyeability
- Sufficient strength and durability
- Finer structure and flexibility
Fibers are of two types: Natural fiber and Man-made fibers. In this article, we will discuss some most common natural fibers.
Natural fibers have different origins. They are found from animals (Wool and silk), vegetables (Cotton, flax), and mineral (Asbestos).
Let’s start with Cotton fiber.
One of the most major fiber in the textile industry is cotton. It can be called the backbone of the world’s textile trade produced in more than 80 countries. Cotton holds more than 50% market share in the apparel and home furnishing. With advancements in technology, industries are now exploring innovative techniques such as 3D textile design insights to enhance the versatility and sustainability of cotton-based products. These insights not only optimize production processes but also pave the way for creating intricate designs and patterns that were previously unimaginable. As the demand for sustainable and unique textile solutions grows, 3D textile design innovations play a crucial role in meeting these needs while reducing waste and energy consumption. By integrating these advanced techniques, manufacturers can produce cotton textiles that not only boast aesthetic appeal but also contribute to eco-friendly practices. This forward-thinking approach ensures that the cotton industry remains competitive, adapting to modern consumer preferences and environmental challenges.
History of Cotton
The word ‘Cotton’ is derived from the Arabic word ‘katan.’ Cotton fiber is collected in the form of unicellular hair from the seed of the cotton plant. Malvales is the order of cotton plant, Malvaceae is the family, Gossypieae is the tribe, and Gossypium is the genus.
More than 5000 years BC, cotton was first used in the middle east and India. During the invasion of Alexander the Great in India, its use spread over Europe. During the eighteenth century, England began to manufacture cotton, and it quickly spread to America. Until the invention of man-made fibers, it was the most important textile fiber. Annually around 25 million tons of cotton are produced annually, and it is increasing at a rate of 2% per annum.
Cotton Plant
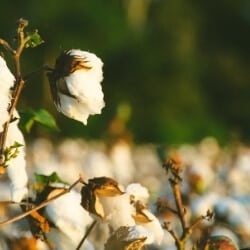
The cotton plant is the purest form of cellulose available in nature. The cotton fiber grows inside an elongated capsule, which is generated in the cotton plant after flowering. The capsule bursts after the growth cycle are completed, and cotton fibers emerge.
- About 30 seeds are generally available in a cotton capsule
- 2000-7000 seed hairs depending on the type of cotton and conditions of growth are available in each seed
The cotton fiber is mainly composed of Cellulose. The chemical composition is,
- Cellulose – 94%
- Protein – 1.3%
- Pectic substances – 0.9%
- Ash – 1.2%
- Wax – 0.6%
- Malic, citric and other organic acids – 0.8%
- Others – 1.2%
Cotton Cultivation and Harvesting
- During spring (March-April) seeds are sown
- After 2-3 weeks, seeds sprout
- Plant flowers bloom after 2-3 months of sprouting
- After a few days, the flowers fall off leaving the cotton balls
- Inside the balls, seed hair starts to grow (one cotton ball consists 5-10 adzuki bean)
- Fiber length and other parameters are achieved for 16-18 days
- Cellulose is deposited inside the fiber for the next 22-50 days
- The balls become dry and burst naturally when the cellulose deposition is finished
- Picking period of the balls for 1-3 month manually or by machine
- The fibers are collected by ginning
Cotton Fiber Structure
The fibril structure of cotton fiber consists,
- Cuticle
- A primary wall
- A secondary wall
- A lumen
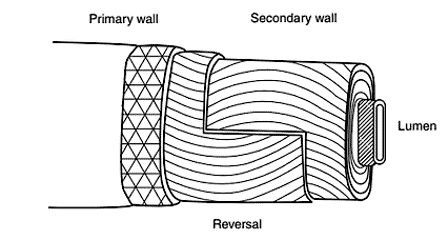
- The outside layer of the cotton is the cuticle. It contains some cellulose with fat and waxes. The wax components in the cuticles enable it to adhere tenaciously to the primary wall.
- The primary wall contains criss-cross fibrils of cellulose and some pectins. It gives peripherical strength to the fiber. The degree of polymerization of cellulose in the primary wall is between 2000-6000.
- The secondary wall remains between the primary wall and the lumen and constitutes the bulk of the cellulose component. Nearly 100% cellulose is present in the secondary wall of a wholly matured fiber. The degree of polymerization of cellulose is near 14000 in the secondary wall.
The molecular weight distribution is more uniform. The fibrils in the secondary wall are 10nm thick. They are packed densely and aligned parallelly throughout the fiber lengthwise with 25-35° spiral winding to the fiber axis. That’s why they can provide immense longitudinal strength.
- The innermost part of the cotton fiber is the lumen, which is a hollow canal running the length of the fiber. Proteins, coloring matter, and minerals are deposited in the wall of the lumen.
The lumen consists of cell, nucleus, and protoplasm before the ball opening. They are removed in the dried fiber and cause twists and convolution.
Lumen varies in dimension depending on the maturity of the fiber. Matured fiber has more secondary wall and less lumen while in immatured fiber; the lumen is broad and distinct.
Properties of Cotton
Physical Properties of Cotton
- The length of cotton fiber ranges from 0.5-2.5 inches.
- The width varies between 12-20 microns.
- A matured raw cotton fiber typically looks like a flattened tube. The cross-section is like oval or kidney shape. They look like a twisted ribbon under a microscope.
- The tenacity of cotton fiber is 26.5-44 cN/Tex (3.0-4.9 g/denier).
- Extension at break is 8-10%.
- Cotton fiber is less elastic. They have an elastic recovery of 74% at 2% extension and 45% only at 5% extension.
- Cotton fiber is very hygroscopic due to the presence of a large number of -OH groups. They show 7-8% moisture regain in standard atmospheric condition (RH= 65%, Temp= 20°c). For calculating the mass in a commercial transaction, the recommended allowance is 8.5%. At 100% humidity, cotton fiber shows 25-27% absorbency.
- Generally, cotton fiber is creamy white. Although five recognizable colors are available: white, gray, spotted, tinged, and yellow stained. The color is affected by climatic conditions, types of soil, impacts of fungi and insects, conditions of the storage, etc.
- They are very comfortable and soft.
- Due to the natural polish in the surface and circular cross-sectional shape, cotton fiber has a natural luster. The smooth coating of wax also contributes to the luster.
Read Also: What is Baumwolle Fabric Le choix du tissu est essentiel pour garantir non seulement le confort, mais aussi la durabilité des vêtements que nous portons. En effet, chaque type de tissu a ses propres caractéristiques et fonctionnalités, ce qui rend crucial de choisir le bon type de tissu en fonction de l’usage prévu. Ainsi, il est important de se renseigner sur les matières disponibles afin de faire un choix éclairé et adapté à ses besoins.
Chemical Properties of Cotton
Effects of Acid
Cellulose is generally sensitive to acid due to the presence of oxygen linkage in the glucosidal linkage. Due to the formation of hydrocellulose, degradation takes place.
There is no effect of cold, weak acid on cotton. Degradation of cellulose occurs when cotton comes into contact with cold concentrated acid, and cotton loses its strength.
Cotton is fully dissolved in highly concentrated mineral acid.
Effect of Alkali
In lower temperatures, the glucosidal linkage in cotton is highly resistant to alkali. occurs in the presence of alkali. In the presence of air, oxidation of cellulose happens in the presence of hot alkali, causing oxycellulose formation.
If cotton is boiled in the presence of 1-2% solution of caustic soda, it reduces the weight due to the removal of non-cellulosic matters. It is called scouring.
Treatment of cotton with 11-16% Caustic soda or 15-25% Sodium Hydroxide with or without tension increases the affinity and luster of cotton.
Effect of Organic Solvent
Cotton is highly resistant to normal solvents, but Copper complexes such as Cuprammonium hydroxide, concentrated (70%) Sulfuric acid completely dissolves cotton.
Effect of Oxidizing Agent
Cotton is treated with oxidizing agents to destroy the natural coloring matter present in it. This process is known as bleaching, which may progressively cause chain scission and reduced tensile strength. The bleaching process can also affect the softness and overall texture of cotton fibers, potentially leading to increased wear and tear over time. Additionally, understanding how different treatments impact the quality of cotton is essential for consumers, particularly when it comes to luxury varieties like pima cotton. Pima cotton shrinkage explained highlights the importance of proper care to maintain its premium qualities, as improper washing methods can exacerbate fiber weakening and diminish its inherent softness. Furthermore, it is crucial for consumers to be aware of the differences between treated and untreated cotton when making purchasing decisions. For instance, preshrunk cotton shrinkage explained can provide insights into how pre-treatment processes can alter the fabric’s behavior during laundering, helping to preserve its original size and quality. By choosing the right cotton products and understanding their care requirements, consumers can enjoy the benefits of softness and durability in their textiles. Moreover, it’s essential to consider the blend of materials when selecting cotton textiles. For example, many consumers wonder if is polyestercotton fabric stretchy, as the addition of polyester can enhance flexibility and durability while maintaining cotton’s breathability. Understanding fabric compositions can help make more informed choices, particularly for items requiring greater elasticity or resilience in everyday use.
Effect of Micro-Organism
Cotton fiber is resistant to moths and most insects but can be affected by fungi and bacteria. In hot and moist conditions, Mildew and bacteria flourish on cotton. Additionally, while cotton is soft and breathable, making it a popular choice for clothing and other textiles, its susceptibility to mildew can be a significant drawback in humid environments. Therefore, understanding cotton suits benefits and drawbacks is essential for consumers and manufacturers alike when considering its application in various products. Proper care and maintenance can help mitigate these issues, ensuring the longevity of cotton items.
Cellulase produced by many of the micro-organisms causes biodegradation to cotton. Copper naphthenate and polychlorophenols can prevent the attack of micro-organisms on cotton.
Effect of Water
Polar -OH groups present in cotton easily attract water, and water easily penetrates into the cellulose network. The ready penetration of water between the fibrils and amorphous region causes swelling of cotton.
Cotton fiber show higher strength in wet condition than dry due to swelling. The screw shapes arrangements of fibrils in cotton are pressed more firmly against each other due to swelling.
Cotton is highly hygroscopic due to the presence of a large number of -OH groups and so contains moisture in normal dry conditions.
Other Properties of Cotton
Effect of Temperature
Cotton fiber is highly resistant to thermal decomposition, but it is dependent on the heat and time of the heating.
Prolonged heating at 100°C – No visible change.
Heating several hours at 120°C – Litlle or no change in strength. Begins to turn yellow.
Heating below 250°C – no effect in the crystalline region. Only the amorphous region is affected.
Heating at 250-270°C – The crystalline region starts to be affected.
Instant decomposition occurs if further heating is carried out over 300°c.
If exposed to flames directly, cotton balls are flammable.
Effect of Light
Cotton fibers turn yellow and gradually losses their strength due to long time exposure in sunlight. In the presence of atmospheric oxygen, particularly high temperature and moisture cause oxycellulose formation, and so degradation of cellulose occurs.
Shorter waves of visible light and UV light causes the main damage. Exposure to sunlight for 940 hours will cause a 50% loss of the strength of cotton.
This effect is dependent on the structure of the goods. The presence of metal content also increases the sensitivity of cotton to daylight.
Classification of Cotton
Based on Staple Length
#SL | Type | Length | Strength | Lustre | Diameter | Spinning count | Example |
---|---|---|---|---|---|---|---|
1 | Short staple | 3/8 inch – 1 inch | Low(Low-grade fiber) | Little or no luter | 13-22 micron | Coarser below 20s Ne | Inidan and asiaric cotton |
2 | Medium staple | 0.5 inch – 1.25 inch | Medium | Medium | 12-17 micron | Medium count 20s-34s Ne | American upland cotton |
3 | Long-staple | 1 inch – 2.5 inch | High(Top quality) | Lustrous | 10-12 micron | Fine count, 34s Ne and above | Sea island cotton, Egyptian cotton, American Pima. |
Types of Commercial Cotton
Sea Island Cotton
It is the highest and most valuable cotton, grows on the coast of the Gulf of Florida, Barbados. Cotton wadding made from this type of cotton fibers tend to be superior in quality.
- Length: 2-inch average.
- Diameter: 0.017mm average
- Color: White to cream
- Advantages: Uniform, high luster, soft, highly deloped twist.
Egyptian Cotton
Two kinds of Egyptian cotton are found, brown and white. Brown one is like sea island cotton. White Egyptian cotton is not so fine.
- Length: 1.5-1.75 inch.
- Diameter: 0.017mm average
- Color: Brown
- Advantages: Regular, less amount of dead fiber.
South American Cotton
- Length: 1-1.5 inch average
- Diameter: 0.019mm
- Advantages: Suitable for mixing with regenerated man-made fiber.
American Cotton
Cultivated in the USA.
- Length: 1-1.25 inch
- Diameter: 0.021mm
- Color: Good natural color.
- Advantages: Extremely fine count can be produced, perfect properties of cotton fiber in spinning.
Indian Cotton
Very short fiber length ranging from 0.6-0.8 inches. Not suitable for spinning.
China Cotton
Lowest grade commercial cotton, length ranges from 0.5-0.7 inch. It is harsh, and the twist is not highly developed. Not suitable for spinning and mixed with better qualities.
Bangladeshi Cotton
In Bangladesh, mainly American cotton is produced. Commercial hybrid cotton is produced in Maherpur, Thakurgaon, Rajshahi, Gazipur Kusthia, Jessore, etc. Quality textile processing is not possible by Bangladeshi cotton.
Some Important Parameters
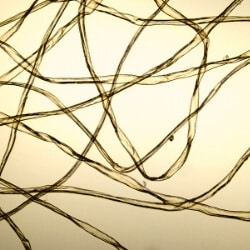
Fibrils
Fibrils are composed of microfibrils, which are the smallest morphological unit of the cellulose molecule. They constitute the cell wall of the cellulose. Generally, microfibrils are of 3.5nm diameter while finer microfibrils can be of 2nm.
Convolution
During the opening time of cotton balls, the fibers dry. The removal of intermolecular water and fluids from the lumen causes cylindrical fibers to form twists or convolutions. Cotton matured fibers dry into flat twisted ribbon form. Generally, 200-300 per inch convolutions are available in a fully matured cotton fiber.
Dead Fiber
When the growth of cotton fiber comes to an end before maturity, it is known as dead fiber. Simply, they are immature fibers. Thinner cell walls can recognize them. Also, immature fiber does not become kidney or oval-shaped. Often, they show ‘U’ shaped cross-section. In commercial cotton, 10-30% of immature fibers are present.
Neps
Neps are detectable entanglements having hard central knots. The mechanical processes such as harvesting, ginning, cleaning, carding, and combing affect the amount of neps in cotton. The immature fiber is more flexible and tends to bend and tangle to form neps.
The fiber properties, mainly its fineness and maturity along with the level of biological contamination(seed coat fragments, barks, stickness), are responsible for the tendency of cotton fiber to nep. They will appear as defects in yarns and fabrics, so neps are undesirable. Removal of neps is generally very costly and sometimes impossible.
Linters
Second layers of short fuzzy hairs in some cultivated cotton are known as linters. The length of the linters is less than ¼ inch. They should be removed by combing to produce high-quality yarn.
They are used for making special photographic papers, and also as the raw material for acetate fibers.
We hope we were able to provide you with enough knowledge about the properties of cotton and other important factors. Consider reading our other piece about banana fiber and its properties as well.
REFERENCE:
Cotton Fibre Structure