Vat Dyes | Properties | Dyeing Mechanism – A Comprehensive Look
Vat Dyes
Despite their higher cost, vat dyes have been gaining popularity these days. Now you may argue that we are using indigo dyes for producing colored denim for quite some time now. So, isn’t Indigo a vat dye?
Yes and No! It is true that Indigo is a member of the vat dye class, but they fail to exhibit any affinity towards cellulosic substrates – even in reduced and solubilized form [1].
The focus of today’s article is only concentrated on vat dyes. Because its superior fastness property has made it the only choice of color when you need to achieve excellent cross-staining results.
Why Vat Dye is So Called?
First things first, we need to know how the name came into being. You see, historically, this type of dyeing was carried out in wooden vessels or vats. Thus, the dye got its name from that. I’ll discuss that ancient process briefly below.
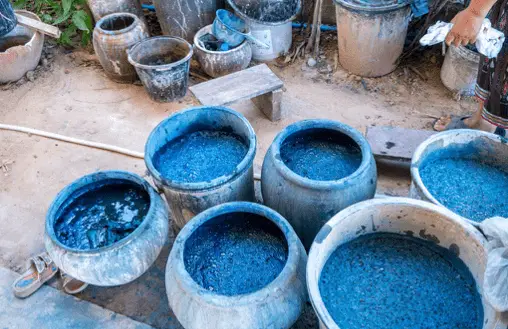
Fermentation Vat
This whole process of dissolving Indigo takes 2-3 days. They used the bacteriological process to convert Indigo to its solubilized form. First, saccharides were added into the dyebath. These saccharides were converted into lactic acid by fermentation. Then, the lactic acid is split up into butyric acid, carbon dioxide, and hydrogen.
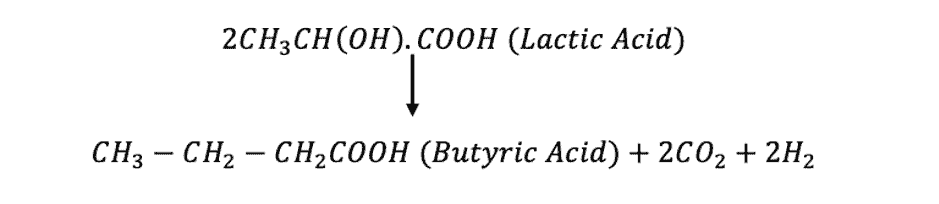
This liberated hydrogen is what ultimately reduces Indigo to indigo white. Later, slaked lime Ca(OH)_2 was added to dissolve indigo white, which in turn produced the yellow solution that was used for dyeing [2].
What Is Vatting?
You’ll hear the term “vatting” quite a lot in this article, so it’s imperative that we know exactly what it means before going any further.
In simple terms, vatting is the process of converting the insoluble vat dyes into its soluble form. Because our ultimate goal is to dye the substrate evenly in an aqueous medium. And the insoluble vat dye displays no substantivity towards cellulose, but the soluble form does.
With the help of a suitable reducing agent and alkali, we can convert the insoluble vat dye into its soluble leuco form. This usually results in a change of color.
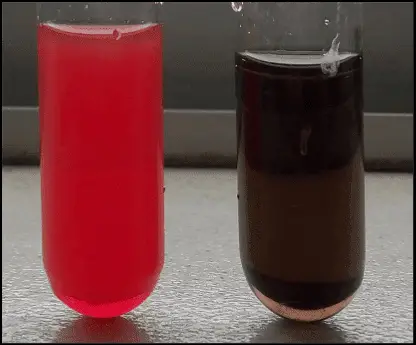
What Does Leuco Mean?
Leuco is a Greek word, which means white. You have already learned about indigo white in the previous section of this article. Since indigo white is produced after vatting, the term leuco or white is still used today to indicate the reduced form of dyes. However, very few of them turn out to be white these days.
Stereochemistry of Vat Dyes
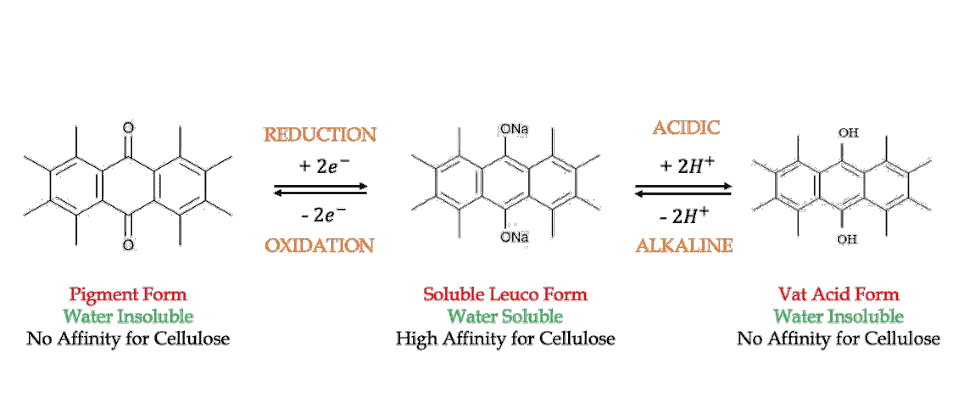
How Do You Define Vat Dyeing?
If you have read the previous sections, then you already have a rough idea. Instead of defining it in a long, complex sentence, we’ll try to define it in a comprehensive step-by-step way.
- It is a water-insoluble dye, usually containing a keto group
- Converted to water-soluble form by a process called vatting
- Applied to the substrate from an alkaline aqueous solution
- Subsequently, oxidized in the fibre to the insoluble form
Properties of Vat Dyes
- Dyes are mostly soluble in hot water, and a few are soluble in the presence of little Na2CO3.
- Solubility can be improved by adding urea at 50–60°C temperature.
- Dyes are liable to be hydrolyzed at higher temperatures and are important for dyeing cotton in pale shades only.
- Exposure of dye bath to sunlight should be avoided as dyes are sensitive to light, and ester groups are affected to develop dye prematurely.
- Shades are brilliant and fast – fastness is equivalent to those with corresponding vat dyes.
- Due to a negligible affinity for cellulose, Na2CO3 is added to enhance dye uptake.
- Though few dyes show levelling at a lower temperature, dyeing at higher temperatures promotes levelling of shades.
- Dyes are costly, but the levelling property is excellent. Range of shade is limited to blue, orange, purple, pink, yellow, green, and golden – all in light shades.
- Tinctorial power of these dyes is too low. So, the increase in concentration by many folds increases shade depth a little.
- Dyes are available in two physical forms – powder and paste.
- Powder form is less stable, stabilization with alkaline salts increases stability whereas paste form is stable in dark places, stabilization can be improved by adding Na2CO3 and NaOH.
Common Phases of Vat Dyeing (Exhaust Method)
You have to follow these 4 steps to know how to how to used vat dyes.

Classification of Vat Dyes
Vat dyes can be classified based on the following –
- Chemical Constitution
- Application Condition
Now let’s talk about the chemical constitution first –
1. Classification Based on Chemical Structure
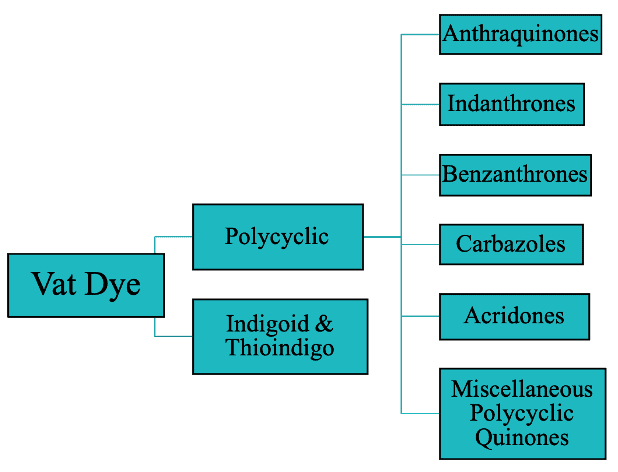
I. Polycyclic Vat Dyes
These class of dyes based on anthraquinone & related polycyclic systems generally exhibit outstanding fastness properties.
- Provides hues covering the whole of the visible spectrum
- Main commercial products are found within the blue, green, brown and black sectors
- Some of the relatively simple yellow and orange dyes cause phototendering
- High stability permits many of them to be used as pigments
- Many of them are suitable for use on cellulosic fibres for infrared camouflage[4]
i. Anthraquinones
Over 200 anthraquinone vat dyes are at present in commercial use, and the constitutions of about 130 of them have been disclosed. They represent a wide variety of chemical types.
- Provide shades ranging from yellow to black
- Complex dyes with structures that may contain up to 19 condensed rings
- Chiefly important in application to cellulosic fibres by dyeing and printing processes
- Varying of vatting conditions, but the only reducing agent of practical importance is alkaline sodium hydrosulphite (Hydrose)
Let’s take a look at one of the many anthraquinone vat dye structures –
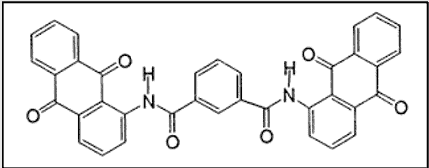
ii. Indanthrones
The discovery of the first vat dye, Indanthrone, is a landmark in the history of synthetic dyes. It was named indanthrene, a name coined from those of Indigo and anthracene.
- Based on anthraquinone
- Marketed by BASF as Indanthren Blue R (CI Vat Blue 4)
- Excellent fastness properties[4]

iii. Benzanthrones (Boasts the Green Vat Dyes)
Dyes from benzanthrone are actually substituted indanthrone, which is used as a dye. Several important vat dyes have been manufactured from benzanthrone. Among these are dibenzanthrone (CI Vat Blue 20) and Caledon jade green (CI Vat Green 1 or violanthrone) [5]. These dyeclass is particularly important for the green vat dyes.
- Good levelling properties
- Excellent fastness to light and wet treatments
- Some colors (mainly green) with these excellent fastness properties cannot be produced by any other means[6]
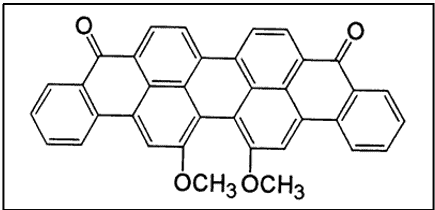
Diphthaloylcarbazole derivatives constitute this important group of vat dyes.
- Good all-round fastness properties
- Provide hues ranging from yellow to black
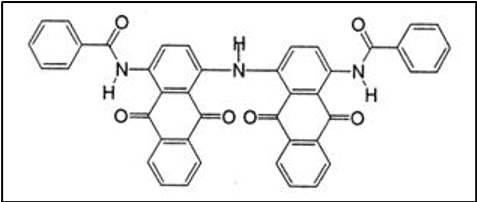
iv. Carbazoles
v. Acridones
The first anthraquinone vat dye containing an acridone ring system was synthesized in 1909 by Ullmann.
- Excellent lightfastness
- Only moderate resistance to alkali due to the keto-enol equilibrium
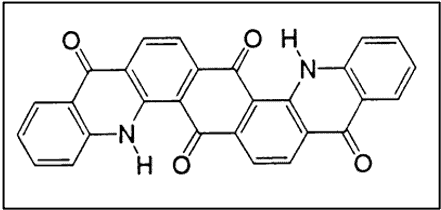
vi. Miscellaneous Polycyclic Quinones
Flavanthrone, Pyranthrone, Anthrathrone, etc. are also of commercial interest.
- Flavanthrone boasts excellent lightfastness but is prone to slow oxidation, lower wash fastness, photochromism
- Pyranthrone, a phototenderer, sports brilliant orange hues of good fastness properties [4]
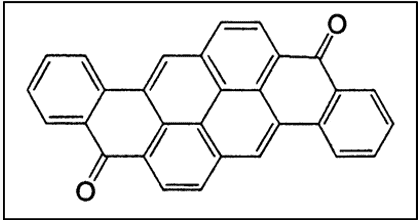
II. Indigoid & Thioindigo Vat Dyes
This is the dye that was produced from the plant of Indigofera genus. It was called Indigo. The first commercially successful operation was achieved by BASF in 1897 using a process based on the fusion of o-carboxyphenylaglycine with caustic potash and oxidation of the resulting indoxyl.
- Gives a bluish shade
- The dye is of considerable commercial importance, especially in warp dyeing for woven cotton denim
- Moderate light fastness, but even when it fades, it stays in tone
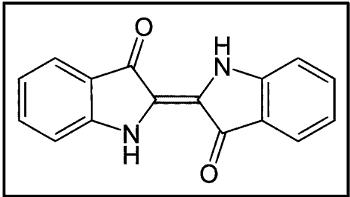
2. Classification Based on Application Condition
I. The IN (Indanthrene Normal) Group of Dyes
- Dyes require the use of concentrated NaOH and high vatting (60°C) and dyeing temperature (60°C)
- No salt is added to the dyebath because of the high substantivity of the leuco dyes for cotton fibres
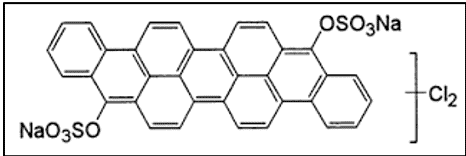
II. IW (Indanthrene Warm) Group of Dyes
- Require only moderate amounts of NaOH and lower vatting (50°C) and dyeing temperature (50°C)
- The leuco forms of these dyes have moderate substantivity for cotton
- Some addition of salt is needed during dyeing to aid exhaustion

III. IK (Indanthrene Cold)
- Dyes only need a low concentration of NaOH with low vatting (40°C) and dyeing temperature (20°C)
- Have low substantivity for cotton
- Needs considerable salt for good dyebath exhaustion
- Some have an amide group that would be hydrolyzed under fine the vatting and dyeing conditions used for IN and IW dyes
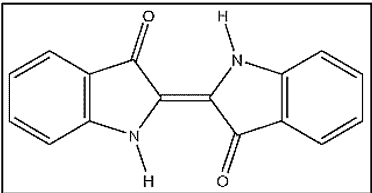
IV. The IN Special Group
- Only difference with IN group is that these dyes require more amount of alkali [7]
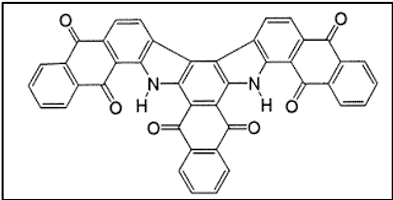
Dyeing of Cotton with Vat Dyes (Exhaust Method)
Now, we’re going to discuss how vat dyes are applied on cotton. First, let’s look at a typical dyeing curve of vat dyeing –
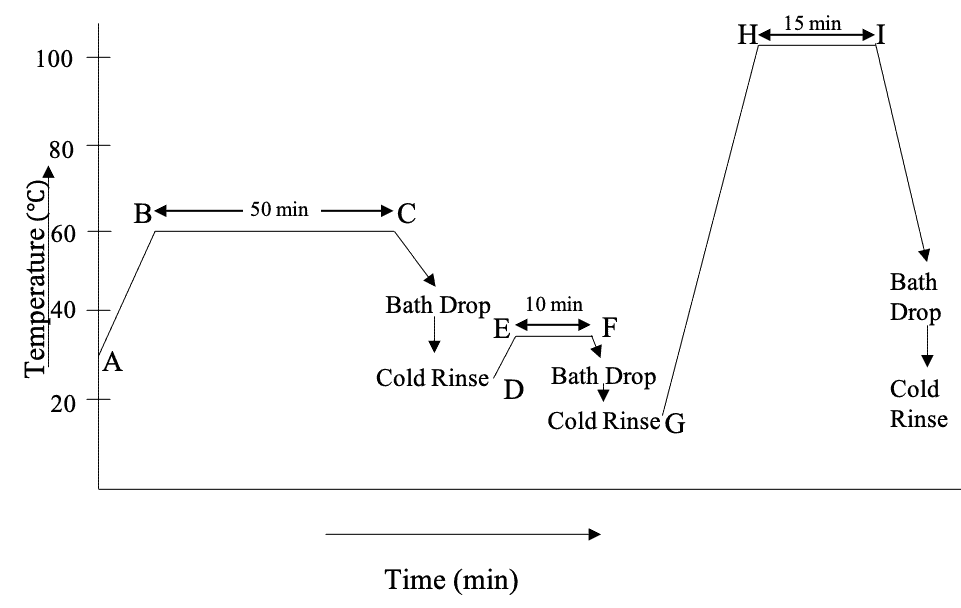
A Typical Vat Dyeing Recipe & Dyeing Curve for Exhaust Method
Let’s look at a recipe first with 3 different depth of shade (%) –
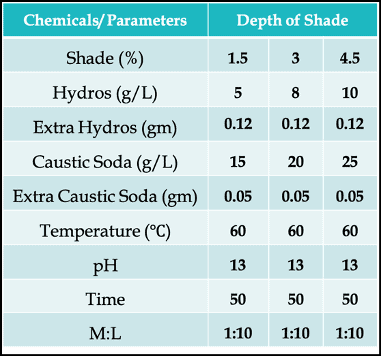
Why Do We Need to Add Extra Reducing Agent & Alkali?
You can immediately notice that we have added extra Hydros (reducing agent) and extra Caustic Soda (alkali). That’s because the dyeing vessel has free space. And due to the presence of oxygen in the air of that open space, some of the reducing agents will get re-oxidized. The oxidative decompositions are given below –
????????2????2????4+????2+2????????????????=????????2????????3+????????2????????4+????2????
2????????2????2????4+????2+4????????????????=2????????2????????3+2????2????
The decompostion products (in bold) are acidic in nature. As a result, the pH get decrease as well. So, we have to add more alkali.
So, to make up for that loss in reducing agent and alkali, we’ve added the extra amount beforehand.
How Do We Calculate the Extra Amount of Reducing Agent and Alkali Required in Vat Dyeing?
Now, we’ve calculated the required amount of reducing agent and alkali based on some recommended values, which, of course, are subjected to change.
But I’ll share them in detail below –
Calculation for Reducing Agent (Hydrosulfite/ Hydros)
Recommendation: 1.7 Kg for each 1 m3 of air
Now, let’s assume for a cylindrical vessel,
Height of the free space of the vessel, h = 2.5 inch
Diameter of the vessel, d = 1.5 inch
So, volume of the free space in vessel = πd²h/4 = 4.42 inch³ = 7.24 x 10-5 m3
Now, for 7.24 x 10-5 m3 we need = 1.7 x 7.24 x 10-5 Kg Hydros
= 1.23 x 10-4 Kg
= 0.1231 gm
Calculation for Alkali (Caustic Soda)
Recommendation: 2.0 liters of 36°Be for each 1 m3 of air
Similarly, for the same dyeing vessel,
for 7.24 x 10-5 m3 of air we need = 2 x 7.24 x 10-5 litre of caustic soda
= 1.448 x 10-4 litre
= 0.1448 milliliter
= 0.06 gm [36°Be = 417 gm/L]
= 0.0604 gm
1. Reduction of Dyes/ Vatting
As you already know, in this stage, the insoluble dye will change into soluble leuco by reduction with suitable reducing agent & alkali combination. And for this instance, they are Hydrose and Caustic Soda, respectively.
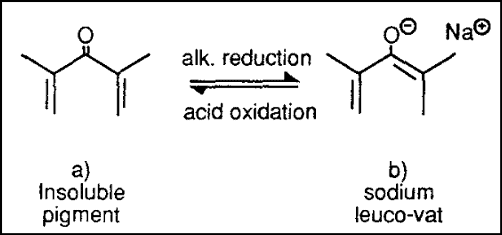
For the anthraquinone type of dyes, the above change takes place while reacting with Hydros or Sodium Dithionite.
Here the hue change takes place because the conjugation of the dye molecule changes.
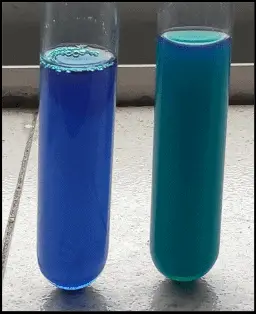
You can learn more about that in this post.
The best result can only be obtained by using the appropriate reducing agent and monitoring the ORP (Oxidation Reduction Potential) value of the bath.
We’ve discussed this subject extensively in another post.
2. Uptake of the Leuco Dye/ Diffusion
Here, the leuco is adsorbed by fibre, and then it is diffused into the fibre. Adding sodium sulfate (electrolyte) could increase the dyeing absorption rate, and surely it is also a good promoter. So it can be added into the dye baths with medium or low immediacy according to the demand.
3. Leuco Oxidizing/ Oxidation
Once the leuco vat dye has entered the fibre, all that remains is to convert the dye from the water-soluble, or leuco form, back to the pigment, or water-insoluble form.
This is usually accomplished by placing the cellulosic fibre in an oxidizing bath. These small ions enter the fibre quickly, and the pigment form of the vat dye is locked in the fibre both mechanically and through secondary or hydrogen bonding.
Oxidations can be carried out in two ways –
I. Air Oxidation
The dyed material is subjected to oxidation by atmospheric oxygen. This is known as air oxidation, airing or skying.
Advantages
- The oxygen in the air is an adequate oxidizing agent for returning the reduced form of vat dyes to the original pigmentary form
Disadvantages
- Slow action
- Non-uniform
- Not ideal for compact structures like yarn packages or beams
- Unwanted side reaction can change the final shade
II. Chemical Oxidation
Here, the dyed material treated with a suitable chemical oxidizing agent.
Advantages
- Rapid action
- Less possibility of unwanted hue change
- Uniform oxidation
- Ideal for any form of material
Disadvantages
- Costly compared to air oxidation
Accelerated chemical oxidation may be carried out by acidified sodium or potassium dichromate (now obsolete), sodium hypochlorite or peroxygen compounds such as hydrogen peroxide (most commonly used).
Now you have to know that alkali carried forward by the substrate does not allow oxidizing agents to release free oxygen, so shades produced in this way will lack desired fastness.

That’s why before applying the oxidizing agent, a thorough wash needs to be ensured. Otherwise, part of the peroxide gets wasted by the following reaction –
Na2S2O4 + 2NaOH + 3H2O2 = 2Na2SO4 + 4H2O
A typical chemical soaping with Hydrogen Peroxide can be –
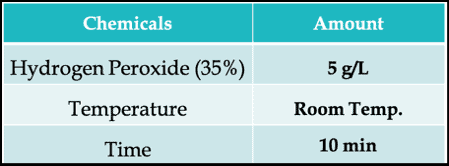
What Is Over-Oxidation?
For some vat dyes, in some circumstances, the oxidation potential of hydrogen peroxide solutions is too great, and over-oxidation (beyond the oxidation state of the original pigmentary form of the dye) can take place.
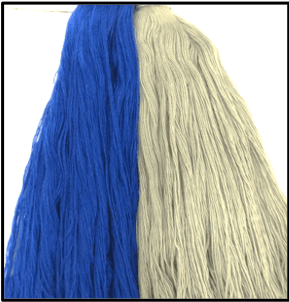
4. Soaping/ After-Treatment
After the oxidation has been accomplished and the pigmentary form of the vat dye is left embedded within the cellulosic fibres, then comes soaping.
And the most interesting part about soaping for vat dyes is it doesn’t actually require the use of soap! Yes, it can describe any treatment in near-boiling aqueous solutions containing a surfactant. Boiling off with only water can be sufficient as well.
Here is a typical recipe –
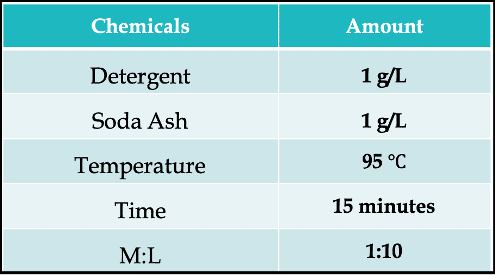
Our goal is to achieve a stable shade and good color fastness through this process. However, shade change does occur in this stage for some dyes, which is not desirable for practical application.
We don’t want any more changes in terms of depth or tone of the shade to maintain reproducibility. All the changes should occur in the oxidation stage.
Two factors are important in practice –
- The efficiency of the soaping process is determined solely by the temperature and duration of the treatment and is not influenced by the pH
- Dyes that show only a small change in color are particularly useful for continuous processes, in which only a limited time is available for soaping
Precautions in Vat Dyeing
Here are some things we need to be careful about –
• To get uniform level dyeing results, the concentration of sodium hydrosulfite and caustic soda must be in exact quantity to reduce the dye bath during the whole process.
• The presence of little excess reducing agent, which is a must, can be tested by vat yellow paper in dyebath. Change in yellow color to deep blue shows the presence of excess reducing agent.
How the Vat Paper Works?
The yellow paper is basically a filter paper dyed earlier with Vat Yellow 3RT dye [CI Vat Orange 11]. Now you already know that vat dyes change color when they’re reduced. As there’s the excess reducing agent in the bath, this dye will For this yellow dye will change into a bluish one.
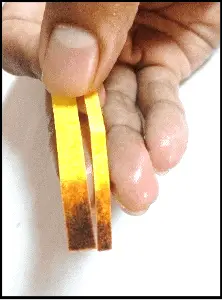
- Excessive quantity of reducing agent and alkali decrease the exhaustion rate of the dyeing. And in extreme cases will over-reduce the vat dyes.
- Excess amount of oxidizing agent can lead to over-oxidation as well.
How to Strip Vat Dyes?
Despite having exceptional fastness properties, vat dyes can stripped into lighter colors for re-dyeing. All we to do is resolubilize the pigmented form of the dye. A typical recipe may contain Sodium Hydrosulfite of 5 g/l, Caustic Soda of 12-15 g/l, and a suitable detergent. The process should be run at 60-70ºC for 30 minutes.
Why Can’t We Dye Wool with Vat Dyes?
We already know, vat dyes require a strong reducing agent and alkali. Unfortunately, wool gets dissolved in high pH solutions, such as caustic soda.
However, you can dye them using low-affinity dyes like Indigo dyes (marketed as Vat Blue 1), maintaining a mild alkali. But you’ve to remember that strength less can occur to a certain extent.
Vat Dyes Advantages and Disadvantages
Advantages of Vat Dyes
- Excellent cross-staining fastness
- Can sustain intense washing & hypochloride bleaching
- Good resistance to sunlight fading
- Finds application in sewing threads
Disadvantages of Vat Dyes
- Requires extra preparatory process, i.e, vatting
- The dyeing vessel needs to be air-tight
- Lengthy dyeing process
- Prone to over-reduction and poor dyeing if ORP value is not monitored
- Difficult to use for printing as it’s susceptible to
- Very costly
Use of Vat Dyes
As you already know, vat dyes exhibit excellent wash fastness and resistance to cross-staining, they are extensively used in places where these properties are the primary concerns. Here are some examples –
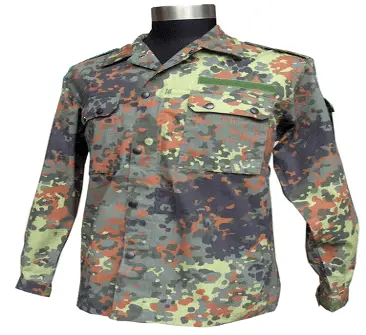
- Workwear and uniforms for armed forces, police, fire, nursing services, etc., which are subjected to severe laundry washing and bleaching with hypochlorite and long exposure to sunlight.
- Clothing and household articles such as shirtings, sportswear, toweling, bed sheets, tablecloths.
- Furnishing requiring high fastness to light.
- Outdoor fabrics requiring high weather fastness such as parasols, tenting, tarpaulins.
- Yarns like sewing threads and for colored threads for weaving, which are subsequently piece – bleached with hypochlorite.
- Shirting fabrics with white stripe go to mercerizing in fabric stage after weaving with dyed and grey yarn.
- Yarns used for the border of dhoti, towel, etc. [3].
Frequently Asked Questions
1. How to Mix Vat Dyes?
In order to mix vat dyes, you need to know the manufacturer’s recommendation first. Different vat dye manufacturer produces different dyes that need different vatting temperature and process. Once you know the temperature requirement for solubilizing them, you’ll be able to mix them easily. That is because the rest of the process is more or less identical for all vat dyes.
2. What is Vat Printing Process?
The vat printing process has become popular because of its high cross-staining fastness attribute, i.e., the color doesn’t bleed to stain adjacent colors. In this process, after the applied vat paste is fixed or dry-steamed at around 110°C. The steaming time is set at around 15 minutes.
Subsequent soaping is carried out in open width washing machines.
3. What is Sulphurised Vat Dyes?
These dyes resemble the intermediate structure of these two type of dyeclass. You can apply the sulphurised vat dyes either as vat dye or sulfur dye. However, the reduction or dyeing process has to be the same as the vat dyeing process.
These dyes boast excellent fastness properties.
4. What is the difference between sulphur and vat dyes?
Although the application process of both the dyes is similar they differ in other aspects. Let’s look at the difference between sulphur and vat dyes in the following table –
Sulphur Dyes | Vat Dyes |
---|---|
Doesn’t come in a wide variety of shades, mainly used for dyeing black shades | Comes in a wide range of shades, even green shades are possible |
Generally, it requires a weak reducing agent | Most of the time, it requires a strong reducing agent |
The effluent load is huge, thus prohibited in most places. | The effluent load is comparatively low, thus widely used. |
Poor wash fastness | Excellent wash fastness |
Comes at a cheaper price. | One of the most expensive dyestuff. |
5. What is the difference between vat and reactive dyes?
Unlike sulphur dyes, vat dyes have almost no similarity with reactive dyes. The main difference between vat and reactive dyes is its application process. Let’s take a look at the below –
Reactive Dyes | Vat Dyes |
---|---|
Reactive dyes don’t require any sort of extra preparatory processes. | Vat dyes require vatting. |
Doesn’t require to be dyed in air-tight conditions | Requires to be dyed in air-tight conditions |
Prone to hydrolysis, thus huge amount of dye wastage | Prone to over-reduction, needs ORP value monitoring |
Cross-staining fastness isn’t as good as vat dyes. | Excellent fastness to cross-staining |
Comparatively less expensive than vat dyes | One of the most expensive dyestuff |
REFERENCES
- Chakraborty, J. N. (2015). Fundamentals and practices in colouration of textiles. WPI Publishing.
- Shenai, V. A. (1983). Chemistry of dyes and principles of dyeing.
- Mahapatra, N. N. (2016). Textile dyes.
- Shore, J., & Society of Dyers and Colourists (Eds.). (2002). Colorants and auxiliaries: organic chemistry and application properteis. Vol. 1: Colorants (2. ed.). Bradford, West Yorkshire: Society of Dyers and Colourists.
- CHATWAL, G. R. (2016). SYNTHETIC DYES. Place of publication not identified: HIMALAYA Publishing House.
- Shore, J., & Society of Dyers and Colourists (Eds.). (1995). Cellulosics dyeing. Bradford, West Yorkshire, England: Society of Dyers and Colourists.