Denim Dyeing with Indigo Dyes
Denim garments were first to become very popular during the 18th century due to its durability and the resistance to tearing. Now denim has become a part of modern culture and fashion from ordinary cloth. Denim has embraced in our daily life like no other.
Firstly, let’s know what is denim?
Denim is a rugged, sturdy fabric in which the warp yarn is dyed, and the weft yarn remains undyed. It is generally 3/1 warp-faced twill fabric. Denim is different from other cotton fabric due to having a diagonal ribbing on its face side.
‘Serge de Nimes’ is a French word from which ‘Denim’ is derived. It refers to the city of Nimes.
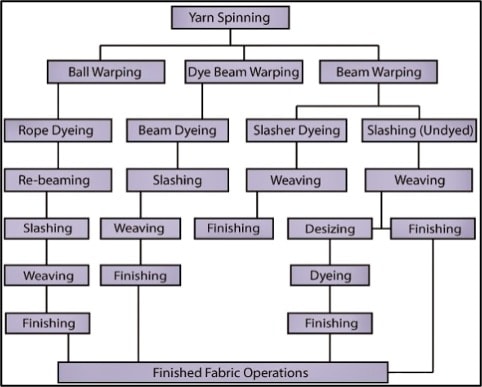
Here is the Process Flow Chart of Denim Manufacturing given above
Now, let’s talk about denim dyeing. Generally, warp yarns are dyed with indigo dyes.
What is Indigo Dye?
Indigo dyes were previously extracted from “Indigofera tinctoria,” i.e., leaves of indigo plants. Later, a German chemist named ‘Adolf von Baeyer’ developed first synthetic indigo dyes during the 1880s.
- Indigo dyes are insoluble in water, diluted alkalis, and acids.
- As they have intra and intermolecular hydrogen bonds, indigo dyes have low solubility.
- They have a minimal affinity towards the cotton fabric.
- The natural form of indigo dyes is insoluble in water (undyeable); hence the leuco form is soluble (dyeable).
Approximately almost 80% of the total types of denim are dyed with indigo and sulfur dyestuff. These dyes are pretty similar to vat dyes in terms of dyeing mechanism.
Steps of Indigo Dyeing
Step 1: Insoluble Indigo
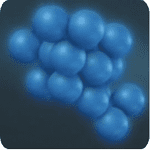
Step 2: Reduction of Indigo Dyes, Converted to Soluble Form
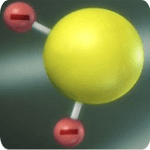
Step 3: Soluble Leuco Indigo
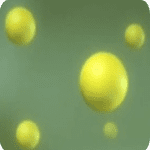
Step 4: Leuco Indigo Applied
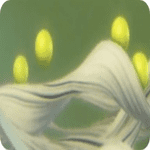
Step 5: Air-Oxidation of Leuco Indigo, Converted to Insoluble Form
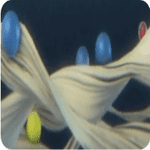
Step 6: Indigo Dyed Fibre
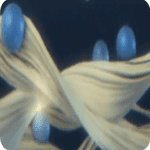
Auxiliaries in Indigo Dyeing
Reducing Agent: It makes the insoluble dye soluble by reduction. The most commonly used reducing agent is sodium dithionite (Na2S2O4).
Alkali: It helps to maintain a higher pH of 10.5-11.5 to obtain the ionized form of the dye. Mainly, Caustic soda (NaOH) is used.
Dispersing Agent: It prevents the agglomeration and aggregation of undissolved particles.
Wetting Agent: It helps to wet the fabric by reducing the surface tension of water.
Sequestering Agent: It makes hard water soft by deactivating the metal ions present in water.
Effect of Different Parameters
Dye-Bath pH
As leuco Indigo is a weak acid, the ionization of the dye increases with the increase in pH. The optimum pH for higher substantivity for cotton remains around 11. pH around 10.5-11.5 gives a satisfactory result, and the depth and hue are not affected. Further increase in pH may affect the depth and hue.
Amount of Reducing Agent (Na2S2O4)
The penetration of the indigo dye into the fiber is affected by the amount of Na2S2O4. Excess Na2S2O4 present in the dye-bath maintains the stability of leuco Indigo.
Immersion Time
Up to a specific limit, the dye uptake increases with the increase of immersion time and then falls. 30 second immersion time seemed to be adequate. Prolonged immersion time reduces color depth as the re-reduction of oxidized Indigo occurs, which is retained by the cotton.
Dye-Bath Temperature
Maximum dye uptake occurs in room-temperature. The affinity of solubilized Indigo for cotton is reduced due to the increase in temperature. Typically, the re-reduction of oxidized Indigo does not occur at a lower temperature.
Time of Airing
A part of the reduced dye is released due to lesser airing time. Optimum airing time for oxidation is ≥60 sec.
Denim Dyeing Methods
Four denim dyeing methods with Indigo are available.
- Rope/Ball warp/ Chain dyeing
- Slasher/ Open warp/ Sheet dyeing
- Loop dyeing
- Beam dyeing
At least 95% of world denim production is done by rope and slasher dyeing.
1. Rope Dyeing
It was first started in USA at 1915. It is a supirior dyeing technology in which the warp wars are pre-treated and dyed in rope form.
Rope Dyeing Process
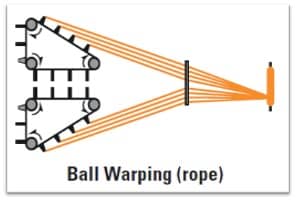
- The warp warns are passed through a special comb and lease rods and wound in the form of ropes in ball warp.
- The rope length generally remains upto 2500 meters. Each rope contains 350-400 ends.
- Machine capacity is up to 36 ropes and 14400 threads depending on the size and the width.
- The ropes are dipped into 6-8 dye baths.
- Multiple dipping of the ropes are carried out for ensuring better penetration.
- Skying of the ropes are carried out after each dip for air-oxidation. The shade is build up due to this.
- The yarn count ranges from 1-16 Ne
Schemetic diagrams of rope dyeing are given below –
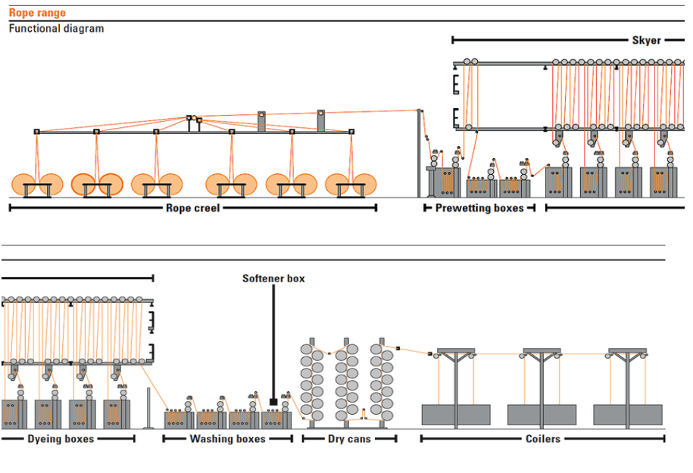
Advantages of Rope Dyeing
- No cross-shade variation
- Wastage of thread is low
- Productivity is high and flexible production
- Less reducing agent consumption
- No time loss during lot change
- Versatility in denim production
Disadvantages of Rope Dyeing
- A lot of space is required
- Immersion time and oxidation time is comparatively higher
- An additional step of opening ropes after dyeing is necessary
- Less flexibility in changing color
- The production cost is high
2. Slasher Dyeing
This continuous process was first introduced in 1970. The warp yarns are pre-treated and dyed in the form of a yarn sheet. This is multi-dip, multi-nip, and multi-airing indigo dyeing.
Beam Warping ⇒ Pre-Treatment ⇒ Washing ⇒ Warp Sheet Dyeing ⇒ Airing for Oxidation ⇒ After-Wash ⇒ Pre-Drying ⇒ Warp Yarn Sizing in Sheet Form ⇒ Weaving ⇒ Finishing
Slasher Dyeing Process
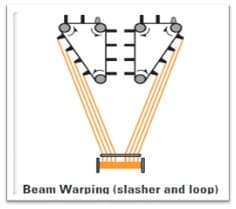
- 6-10 dye-baths per vat. Less time is required as each yarn is independently subjected to treatment.
- Warp beams supply warp yarns. The machine capacity is 9500 warp yarns having 300-750 warp yarns per beam.
- Yarn count and denim fabric design determine the number of total warp yarns.
- The yarn count ranges from 1-30 Ne.
Schematic diagrams of slasher dyeing are given below –
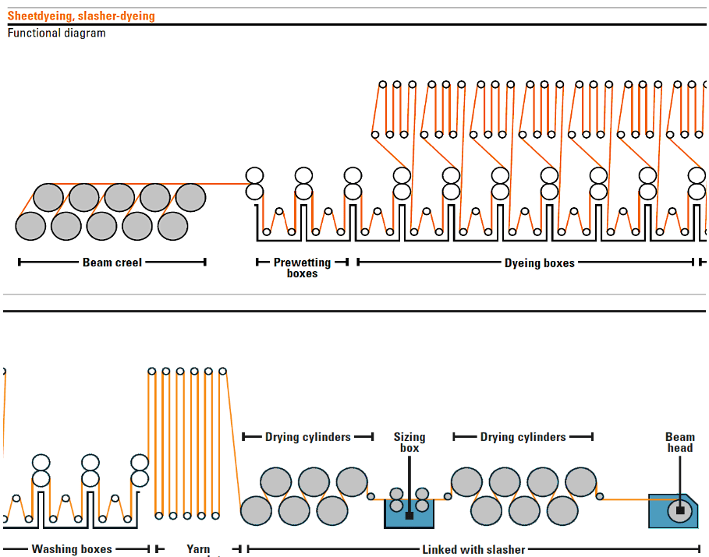
Advantages of Slasher Dyeing
- Less space is required due to compact design
- Oxidation and immersion times are less
- Continuous process
- Flexibility in changing color
- Production cost is low
Disadvantages of Slasher Dyeing
- Possibility of cross-shade variation
- Possibility of yarn rupture
- Productivity and flexibility in production are low
- Extra time needed for lot change
- No versatility in denim production
- Reducing agent consumption is high
3. Loop Dyeing
Looptex Co., Italy in 1903 first developed it. It is almost similar to slasher dyeing, except it has only one dye bath.
Loop Dyeing Process
- The process consists of multiple dips and layered skying.
- Warp yarns are dyed in sheet form.
- Air oxidation after each dip.
- The warp sheet circulates in the form of closed-circuit, which looks like a loop.
- Substantial fall in dye and chemical concentration after each dip, instant fortifying of the bath is necessary for developing the required shade.
- The high initial concentration of the indigo bath is necessary.
Schematic diagrams of loop dyeing are given below –
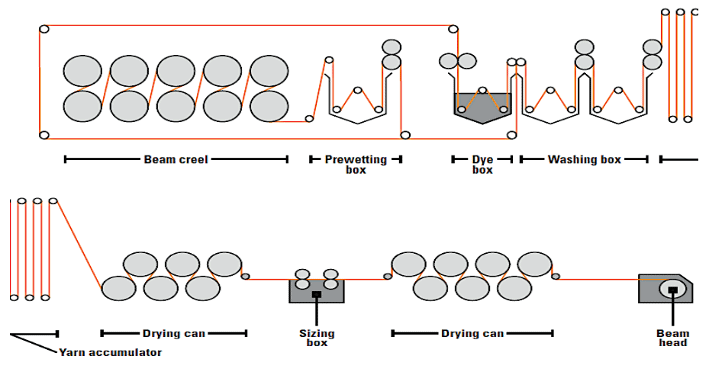
Advantages of Loop Dyeing
- Less space required as it is a compact system
- The initial investment is low
- Maintenance and energy costs are low
- The consumption of water, dyestuff, and chemical are minimal
Disadvantages of Slasher Dyeing
- Possibility of selvage center variation and yarn breakage
- There is thread loss during the change of article
- Lot change requires more time
- Flexibility limitations and low productivity
Combination Dyeing Methods
For bottoming and topping, a combination of indigo dye with another dye in different dye-bath can be used. The most common process in sulfur bottoming/ topping.
Bottoming and topping are done when high intensity in color with acceptable fastness is required. As a diverse shade of blue color is very demandable, it is done.
Bottoming Effect (Sulfur Dye + Indigo)
Initially, dyeing with sulfur dye is done, followed by indigo. In this process, darker shade can be produced with less amount of indigo. There is a possibility of large removal of sulfur dyes in indigo dye-bath due to Sodium-dithionite.
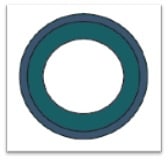
The picture shows the inner layer with sulfur dye and outer layer with indigo dye.
Topping Effect (Indigo + Sulfur Dye)
Initially, dyeing with indigo is done, followed by sulfur dyeing. Much darker color than sulfur bottom can be obtained. The colors include black, blue-black, yellow-brown, and green. Slub appearance can be produced.
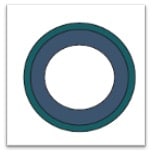
The picture shows the inner layer with indigo and outer layer with sulfur dye.
Ring Effect
It is surface dyeing of yarn with indigo. As indigo dyes lack affinity towards fiber, they tend to adhere to the surface. If too much surface dyeing is done, it leads to poor color fastness.
Frequently Asked Questions
You might still have some queries regarding denim dyeing. We have tried to provide the answers in this section.
1. Is denim a jean?
Denim is made of 100% cotton and twill structure, whereas jeans are one type of garment which is made of denim fabric. Denim can be defined as either pants, jackets, skirts, or shorts. On the other hand, jeans are specially defined as pants.
2. Is indigo dye sustainable?
Natural indigo is sustainable. After dye extraction, the residue can be composted and used as fertilizer. But synthetic indigo is not a natural dye.
3. Is indigo more blue or purple?
Nowadays, indigo color in referred to as color between blue and violet. Halfway between blue and purple is violet. So, indigo can be said as three-quarter blue and quarter purple.
4. Is synthetic indigo dye toxic?
Synthetic indigo dye is extracted from the Indigofera plant. Several toxic chemicals are required for synthesizing indigo dye, which also includes formaldehyde.
5. What does the Indigofera plant look like?
They are a shrub which are one to two meters high. Depending on the climate of the place, they can be of different types such as annual, biennial, or perennial.
REFERENCES