Fully Continuous Reactive Dyeing Process in Padding Method by Padding Mangles
Despite the immense development that has happened in the batch dyeing machines, it’s still way behind its continuous counterparts in terms of water consumption. The lowest liquor ratio that you can go with for batch-wise dyeing is 5:1. However, some unique machines(ULLR equipment) can get as low as 3:1, but their commercial implementation is yet to be seen.
Anyway, padding method is the way to go, if you’re really concerned about water consumption. With this method, you can dye with a liquor ratio of 1:1 to even 0.5:1.
Therefore, in this article, we’ll take a look at the different semi-continuous & fully-continuous reactive dyeing processes that take advantage of padding angles.
Before getting into it, check out our previous post on dyeing machines to have a better understanding of the inner working of a cloth dyeing machine.
Pad–Dry Dyeing Process
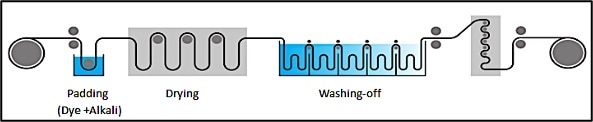
- Only compatible with reactive dyes that have high reactivity
- For dyes of lower reactivity, the dried fabric must be baked to promote further fixation
- In pad dry process, the fabric is first padded with a dye solution containing sodium bicarbonate
- During drying, bicarbonate is converted into carbonate, which gives a higher pH and more effective fixation.
Pad–Dry–Bake Dyeing Process | CPB Dyeing Process

- Suitable for less reactive dyes such as MCT dyes.
- Used mainly in combination with the application of disperse dyes to cotton/polyester materials using the thermosol process.
- Typical baking temperature for cotton-polyester blend dyeing (cpb dyeing process) is 200–220 °C for 1 min, but for only cotton dyeing, it’s much lower, at 150–170°C
- When dyeing deep shades, the degree of fixation is usually lower.
- Fabric tends to yellow at high baking temperatures and this can influence the hue of pale shades.
Pad–Steam Dyeing Process
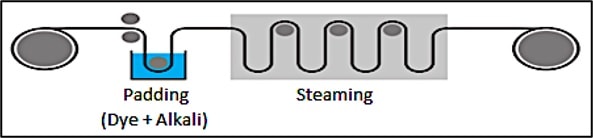
- In pad steam process, substrates are padded with a solution containing the reactive dyes, salt, and the appropriate alkali.
- Only selected dyes are suitable and the manufacturer’s recommendations should be followed.
- The hot humid conditions during steaming tend to cause excessive hydrolysis of the reactive group and thus lower the color yield.
Pad–Dry–Pad–Steam Dyeing Process

- It is the predominant fully continuous reactive dyeing process.
- The fabric is padded with a neutral solution of the reactive dyes, dried,and then padded with the alkali solution containing salt before steaming.
- The dye solution is quite stable because there is no alkali present in the dyebath.
- Salt or anti-migrant agent helps to minimize migration of the dyes to the yarn surfaces during the initial stages of drying.
- intermediate drying ensures a uniform and high pick-up of the alkaline salt solution and minimizes bleeding of dye into the chemical pad.
- After drying, the fabric must be cooled on cold cylinders to avoid heating the chemical pad solution.
Pad–Batch Dyeing Process

- The process is a mi-continuous one.
- Can run fabric roll of moderate length at a pretty decent cost.
- Actually, this is pretty similar to the exhaust method because almost all the dyebath is involved with the substrate at ambient temperature.
- The method involves padding the fabric with a pre-mixed alkaline solution of the reactive dyes and then winding up the impregnated fabric on a suitable roller.
- Dye and alkali solutions are usually mixed just before padding using metering pumps to maintain the correct ratio.
- Fixation occurs during the storage of the batched fabric at ambient temperature.
- The slow dye fixation achieved during the storage of a roll of impregnated fabric at room temperature (4–24 h) results in better dye diffusion and penetration into the fibers.
- Obviously, the dyes must have adequate reactivity under the batching conditions to give good fixation within about 24 h. The more reactive dyes give effective fixation within 2–6 h.
To avoid evaporation from the exposed surfaces and edges of the roll, the fabric is stitched to a somewhat wider end-cloth that is padded and finally wrapped around the entire wet roll before it is covered with a plastic film.
Frequently Asked Questions
Now, let’s finish this article answering some frequently asked questions.
1. Why continuous process is not used for knit fabrics?
Knit fabrics aren’t dimensionally stable. The longitudinal tension that’s applied during the padding process will alter the dimensions of knitted goods. That’s the main reason behind knitted fabrics being dyed in batch machines.
2. What types of fabric can be dyed with continuous dyeing machines?
Woven and non-woven fabric types are mainly dyed with this process. However, by applying some modifications, knitted goods are being dyed with these machines.
REFERENCES