What is Fusible Interfacing | Types of Fusible Interfacing
To make pieces of clothing from fabric, the goal of joining of interfacing with the different pieces of the garments and their procedure is essential. Especially if the interfacing is joined by sewing in the shirt’s collar or at the forward portion of a coat, interfacing might be shrunk, and puckering may occur along the sewing line.
In a request to avoid these difficulties, fusible interfacing is used. In this article, we’ll exclusively talk about fusible interfacing. So, if you want to know about interfacing in general then refer to our previous post on what is interlining. Also, if you’re wondering, can I use felt instead of interfacing, do check out that post also.
What is Fusible Interfacing?
The interfacing which is applied to the principle fabric with the assistance of heat and pressure is known as fusible interfacing.
Here a tiny layer of thermoplastic resin is applied to the fabrics. The fabrics which are utilized for fusible interfacing might be woven, knitted, or felted. And in these fabrics, there may have natural fibers, synthetic fibers, or a mix of them. Various types and of different characteristics of resins are utilized as thermoplastic resins.
- After putting the fusible interfacing appropriately on the garment’s parts, then the heat and pressure are applied. The thermoplastic resins melt. Because of the heat and pressure, it helps in getting the interfacing together with the fabric of the garments. And the melted gum goes about like glue. The framework cannot be utilized for various sorts of pieces of clothing and fabrics. Yet this procedure is being used wherever in the vast majority of the cases.
- During the time of combining the fusible interfacing, heat, pressure, and time, these three components are adequately controlled, otherwise fusing isn’t done appropriately.
- During fusing, the temperature ought to be on such a scale; thus, the pitch can soften.
- If the temperature does not precisely match the requirement, resin doesn’t liquefy appropriately, causing the separation of holding among interfacing and the pieces of clothing.
- If the temperature is higher than the requirements, the resin will dissolve in a more noteworthy sum, and because of the pressure, chances of strike back or strike through may occur.
Properties of Fusible Interfacing
Different characteristics are available there in different kinds of interfacing. The choice procedure of the types of interfacing relies upon the fabric of the garments, types of fusing machines, utilization of the garments, and properties of the garments. The basic properties for interfacing are referenced underneath.
- Here, the fusing is finished by utilizing perfect temperature so that there is no hampering of fabric shading.
- The most extreme temperature of fusing should not be more than 175°
- The base temperature of this interfacing should not be under 110°
- The base temperature should not be applied during fusing. Otherwise, it will make an issue in the holding between garments and interfacing during the washing or end-user of articles of garments.
- The bond of fusible interfacings should not be opened or hampered because of washing or dry cleaning.
- After finishing this sort of interfacing, it should contain the solidness and drape properties of garments.
- The shade of fusible interfacings must be white or transparent. However, it tends to be diverse in shading, as indicated by the fusing prerequisites.
- The interfacing should not poisonous to the human body during the end-use of garments
- The desired rigidity and handle after fusing of the interfacing should be obtained.
Advantages of Fusible Interfacing
The advantage you can get from fusible interfacing over sewn interfacing are listed below –
- Joining the fusible interfacing with the principle fabric, the time required is minimal. So higher output with lower labor is achieved.
- The procedure of joining the fusible interfacing is effortless and for doing this, there is no need to hire a specialized worker, or there is no need for giving special training to the workers.
- Consistent shapes, outer beauty, these qualities are found in the fabrics, which are manufactured by fusing interfacing. But in sewn interfacing garments, these qualities are sometimes missing.
- The beautiful appearance and better qualities are found in fusible garments. Compare to sewn garments.
- From time to time, the utilization of fusible interfacing works as a working aid. For instance, making of the waist belt, the use of slotted interfacing helps the belt making.
- You can find plenty amount of fusible interfacing in the market for buying.
Conditions of Fusing
There are many types of fusing methods to join the fusible interfacing with the principle fabrics. But the way the fusible interfacing is done, the aspect has to be good and beautiful. For fulfilling these orders, some condition is required to be achieved during the fusing operation. And they are mentioned below
- Beauty: The garments which are made by fusible interfacing becomes beautiful aesthetically. Along with this beauty, there is the quality of stiffness, draping, handling, etc. of the piece of garments where fusing interfacing is used. Understandably, fusible interfacings can’t render the performance of the strongest fabric stiffener, but it gets the job done in some instances. And which are determined before the production of the garments. Mostly, which type of fusible interfacing is being used, which kind of garments, you have to choose carefully. Hence expected appearance and merits will not be achieved.
- Strength: Applying resin bond the principle fabric and fusing interfacing. The object of fusible interfacing is done. The strength should be such (of the resin bond) that the resin doesn’t detach from the garments during manufacturing, using, and the time of washing. Significantly it is needed to hold the strength till the standard time of the fabrics. Else, if the bond is separated from the fabric, then there will be uneven. As a result, the garments will look bad. This type of problem occurs due to under fuse or wrong selection of the interfacing. The type of interfacing that has a higher level of strength is often used as the best tape for cloth.
- Proper Fusing: You should take care during fusing, so that strike back or strikethrough doesn’t occur. If the temperature and pressure are high during the fusing, then melted resin may come out in the Infront garments, which is called strike through. If the melted resin goes down, then it is called strike back. Both strike back and strike through are unfavorable for the garments and fusible machine.
- Shrinking in Heat: For the most part, the resin is done at 150 to 170 – degrees centigrade temperature. However, a few fabrics may shrink at this temperature. In this way, you need to check the texture doesn’t contract while doing fusing. Else problem will be great for producing the garments. Also, the garments will be shorter in size than the standard size.
- Fabric Color: Care should be taken so that the color doesn’t change where fusing has been done. But, if the color changes eventually, then the garments will be rejected due to shade matching problems with the garment.
- Likeness in outside appearance: especially, due to the fusing of heaped fabrics, the heap of the fuse part may deviate. Since fusing both weight and temperature is applied. If the heap digresses because of weight, at that point, after the production of garments, the distinction may show up among fused and non-fused garments.it must be under tight restraints, so likeness in appearance isn’t hurt
- Special Quality: Special features in the fabric are created through finishing; you should deal with that the exceptional features are not destroyed during fusing. For instance, while joining the fusible interfacing with the showerproof fabric, the showerproof quality may harm because of temperature
- It should be applicable for both regular wash and dry wash
- It should not harm public health especially children
To fulfill the conditions mentioned above, appropriate determination of what type of interfacing is to be used in what type of fabric is necessary. The types of fusing machine used is also important. And while fusing the pressure, temperature, and timing should be adequately controlled. In addition to that, sometimes testing is required to check that the fusing is done properly. Because sometimes the fault cannot be understood seeing in open eyes.
Types of Fusible Interfacing
Numerous kinds of fusible interfacing are utilized in the garments industries. A wide range of fusible interfacing can be grouped from multiple points of view. Yet universally chiefly dependent on the types of resins, the classification of fused interfacing is principally utilized. Because of the characteristics and properties of the resin, the order of fusible interfacing is talked about beneath:
Let’s look at their application first, then we’ll go into the details one by one.
Types of Fusible Interfacing | Application |
---|---|
PVC (polyvinyl) Coated | Coat/Suit |
PVA (polyvinyl Acetate) Coated | Mostly on ready-made garments |
Polyethylene Coated | Neckline of garments, the cuff of the shirts |
Polyester Coated | Standard for almost all types |
Polyamide Coated | Apparels that need dry cleaning |
Polypropylene Coated | Clothing that’ll be washed by water |
PVC (polyvinyl) Coated Interfacing
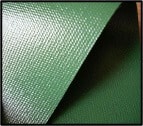
- The coating of polyvinyl chloride is used in the various amount on the principal fabric of the interfacing.
- Washing and fry cleaning both can be easily carried out in these as they are not damaged in water washing or dry cleaning.
- It is vastly utilized for coat/suit type clothing.
PVA (polyvinyl Acetate) Coated Interfacing
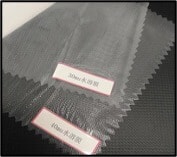
- A light coating of plasticized PVA (Polyvinyl Acetate) is mainly used as the resin coating.
- Dry-cleaning can not be carried out in Polyvinyl acetic acid derivation covered interfacing. Also, it has restricted launderability. But it can be mild water washed
- Low temperature and pressure are required for this reason. This type of interfacing is used in leather or in far.
- This interfacing is once in a while utilized in the RMG industry.
Polyethylene Coated Interfacing
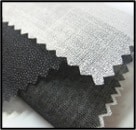
In this type of interfacing, there is a resin of polyethylene coating. The amount of polyethylene coating on base fabric varies according to the fabric. You may get surprised to know that the strong fabric tape that you see in stores can contain polyethylene as a coating material.
Because of the measure of Polyethylene covering, Its characteristics perhaps high or low. The more prominent measure of covering, in the wake of fusing the interfacing, the fused part will be hard up to quality.
The impact of fluctuating the thickness of the resin is to give progressively conspicuous assurance from cleaning solvents and a higher melting point with growing flexibility.
The fabric annexed to this kind of interfacing is washable in water, yet they can’t be launder. Yet, on the off chance that the measure of resin is high, at that point, dry cleaning should be possible.
By and large, this kind of interfacing is utilized in the neckline of garments, the cuff of the shirts.
Polyester Coated Interfacing
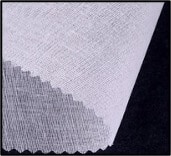
On account of polyester coated fusible interfacing, Polyester(PES) is utilized as a resin coating. The difference of qualities between the interfacing depends on the amount of polyester coating.
Fusible interfacing of Polyester coating can be utilized in a wide range of garments. Because the interfacing is not damaged if it is washed by water or it is washed by dry cleaning. Polyester coated fusible interfacings are also known as standard interfacings and for good reasons. The most pronounced one is its resistance to water and dry-cleaning.
It is accessible in the market, however expensive.
Polyamide Coated Interfacing
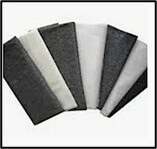
On account of Polyamide covered fusible interfacings, the Polyamide is utilized as a resin coating
Polyamide covered interfacing is generally used in those garments which are done by dry cleaning.
But it can also be used in those garments which can be washed below the temperature of 60-degree centigrade. In this case, high-temperature fusible interfacing has to be used.
Polypropylene Coated Interfacing
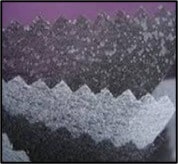
Polypropylene fused interfacing is like the properties of Polyethylene covered interfacing.
In this method, the temperature is high. Like the Polyethylene covered interfacing.
This kind of interfacing is utilized in those pieces of clothing which are washed by water.
Methods of Resin Coating
Fusible interfacing is made by applying the layer or coating of resin on the base fabric. There is differentiation in quality dependent on the kinds of coating of the resins. In different manners, resin coatings should be possible. In any case, the most generally utilized technique for coating is talked about here.
Scatter Coating
Resin is splashed in little particles on the base fabric by a showerhead.
At that point, temperature and pressure are utilized to melt the resin. Furthermore, the melted resin is joined appropriately with the fabric by pressure.
The atomic size of the resin differs between 150 to 400 microns, which are greater than different strategies.
Properties of interfacing aren’t all through uniform in this kind of coated interfacing. Hence, this sort of interfacing is less expensive than others. But that the consistency of the quality and flexibility of the interfacing is similarly low.
Dry–Dot–Coating
The fine Powder of resin is applied on the base fabric in dot form by an engraved roller.
Then the base fabric is passed through an oven. Due to temperature, the resin melts. And due to the pressure of roller, the resin sticks well on the base fabric. There may be different types of temperature and pressure for different types of resins.
The number of dots per centimeter ranges from 3 to 12. And the size of resin particles varies from 80 to 200 microns. The small size of dots is used for light fabrics, and big size of drops is used for a coarse type of fabric.
The property of this type of interfacing is all through uniform.
Paste Interfacing
The fine resin powder is changed over into paste by the utilization of chemicals and water. At that point, the paste is imprinted on the base fabric of the interfacing, looking like little dots in a particular example. By applying temperature, water and chemical compounds are evaporated from the base fabric.
Accordingly, the dots of the resins are joined together with the Fabric. Fine dots are delivered by printing procedure with a resin size of 1 to 80 microns.
The resin coating is finished with the minimum sizes of dots. Property is all through uniform.
Film Coating
Resin is first melted by the utilization of heat and afterward applied on the base fabric as a fine film on one side of the fabric by machine. Generally, Polyethylene as a resin is utilized for film coating. The flexibility of film-coated interfacing is very less of what others
Emulsion Covering
The resin powder is made as an emulsion with the assistance of chemicals and water. At that point, through the container of the emulsion, the base fabric is passed, which picks up the emulsion. By the utilization of pair of press rollers, emulsion take up is controlled. At that point, the fabric is gone through an oven where the interfacing is dried. And, the coating of resin adheres reasonably on the two sides of the fabric. The very hard hand feeling is obtained, after the resin of this kind of coated interfacing.
REFERENCES