Disperse Dyes – Classification | Properties | Dyeing Mechanism
Disperse Dyes
The development of disperse dyes was carried-out to permit the dyeing of hydrophobic thermoplastic fibers (ex. acetate, triacetate, nylon, polyester, acrylic) and other synthetics.
These dyes are mostly substituted azo, anthraquinone, or diphenylamine compounds that are sparingly water-soluble and non-ionic.
Short History
- 1922: Green and Saunders- The dyestuffs suitable for cellulose acetate such as Ionamines colors
- 1923: Baddiley and Shepherdson- S.R.A (Sulpho ricinoleic acid) colors
Above, both colors were found to be applicable to polyester. However, as polyester has a very compact structure, the dyes being inferior to them. So, it was necessary to modify the original cellulose acetate dyes from their fastness and dyeing character point of view.
In one of such developments, the application of the insoluble dyes in the form of micro-fine dispersion called as disperse dyes were brought into commercial practice.
Classification of Disperse Dyes
Disperse dye can be categorized based on:
Field of Application
- ‘No suffix’ dye: It is not suitable for polyester, but ideal for acetate and nylon.
- Group A dye: It has poor sublimation fastness (~Grade 2), suitable for acetate and nylon, but may be used for polyester.
- Group B dye: It shows moderate sublimation fastness (~Grade 2–3), is suitable for acetate and nylon. Well-leveled shades on polyester, coverage on ‘configurational barre’ is excellent, and so is invariably applied on textured polyester.
- Group C dye: It has good sublimation fastness (~Grade 3–4), is suitable for all methods to dye polyester, e.g., carrier, HTHP, thermosol, and other processes, where maximum sublimation fastness is not required.
- Group D dye: It has maximum sublimation fastness (~Grade 5). Exclusively for dyeing of polyester in HTHP or thermosol technique but not in carrier method.
Chemical Nature
- Azo disperse dyes
- Anthraquinone disperse dyes
- Other disperse dye classes
- Nitroarylamino disperse dyes
- Coumarin disperse dyes
- Methine disperse dyes
- Naphthostyryl disperse dyes
- Quinophthalone disperse dyes
- Formazan disperse dyes
- Benzodifuranone disperse dyes
Different Properties (Polyester Dyeing)
Classification | Molecular Weight | Polarity | Dyeing Rate | Sublimation Fastness |
---|---|---|---|---|
Low energy | Low | Low | High | Low |
Medium energy | Moderate | Moderate | Moderate | Moderate |
High energy | High | High | Low | High |
Properties of Disperse Dyes
- Disperse dyes are low molecular weight substances, mostly derived from azo, anthraquinone, and diphenylamine.
- They are crystalline materials of a high melting point (>150ºC).
- They are marketed in both powder and liquid forms.
- These dyes are electrically neutral, thus non-ionic in nature. No strong solubilizing groups like sulphonic or carboxyl groups are present. However, weak solubilizing groups like aromatic or aliphatic –NH2, −NHR, and –OH groups may be present and do not have an affinity for any fiber.
- They have particularly low water solubility (sparingly soluble).
- They must be dispersed in water using a dispersing agent. Otherwise, a carrier must be used.
- These dyes have a relatively high saturation level in the fiber (30-200 mg/g of fiber).
- Due to the absence of ionizable groups, these dyes tend to sublime without decomposition. Consequently, the color of disperse-dyed fabric may fade while ironing.
- Certain disperse dyes tend to fade when stored in an atmosphere having fumes from gas heaters.
- The dyes having identical chromophores (indicated by C.I. number) produced by different manufacturers. They may not give identical shades on dyeing. The shade produced depends on several factors like shape, size, and volume of the dye crystals, colored impurities or isomers, type and amounts of dispersing agents, and products added for standardization.
Fastness Properties of Disperse Dyes
Both the light fastness and the fastness to washing of these dyes on synthetic and acetate fiber is usually moderate to good.
Fastness Property | Comment |
---|---|
Washing | Good |
Light | Good |
Crocking/Rubbing | Moderate to good |
Gas fume fading | Moderate |
Chemical Constitutions of Disperse Dyes
- Most of these dyes have low molecular weight. They are mainly mono azo and anthraquinone derivatives.
- The reason behind the huge number of azo disperse dyes is that the number of possible substitution patterns in different diazonium ion and coupling components are high.
- Anthraquinone disperse dyes are usually 1-hydroxy or 1-amino derivatives having bright colors ranging from red to blue.
Polyester Dyeing with Disperse Dyes
Disperse dyes are one of the best dyes for polyester fabric.
- Polyester is undyeable below 70-80°C and the rate of diffusion of disperse dyes into polyester below 100°C is so low.
- HTHP Method: 130°C temperature is required for its dyeing. For dyeing using the HTHP method, special equipment is needed, which can withstand such conditions.
- Carrier Method: The fiber can be dyed in a boiling dyebath at atmospheric pressure in the presence of the carrier. The main function of the carrier is to reduce the Tg of the fiber.
- As these dyes are insoluble or only slightly soluble in water, they are applied from an aqueous dispersion in the presence of a dispersing agent.
- They require slight acidity for their exhaustion into the fiber. The acidity is achieved by adding acetic acid (pH of 4.0–4.5).
Mechanism
The mechanism of the disperse dyeing of a hydrophobic fiber such as PES can be considered to comprise five sequential stages. They are:
- Dissolution of dye molecules from the surface of dispersed dye particles and the establishment of a monomolecular state in the aqueous dyebath.
- Convective diffusion of the dissolved dye molecules through the bulk dyebath to the fiber structure.
- Diffusion of the dye molecules through the diffusional boundary layer present at the fiber surface.
- Adsorption of the dye molecules onto the surface of the substrate.
- Diffusion of the dye molecules within the fiber interior.
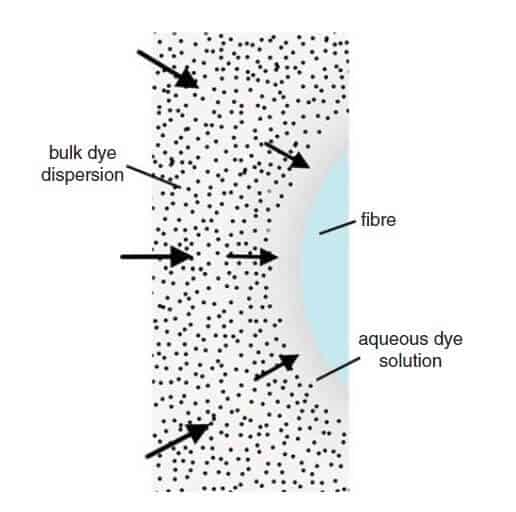
Reduction Clearing
In the case of disperse dyeing on PES fibers,
- Particulate disperse dye molecules accumulate at the surface of the dyed substrate because of the dye’s low aqueous solubility
- Dye auxiliaries may also be present at the surface of the dyed PES material
So, reduction clearing is carried out. The process requires,
- An aqueous alkaline (NaOH) solution of Sodium hydrosulfite (Na2S2O4)
- Non-ionic surfactant
- 50ºC–80ºC temperature
- Rinsing and neutralized using dilute CH3COOH
Mechanism of Reduction Clearing
In the case of azo disperse colorants, reduction clearing breaks the azo bond producing colorless amino compounds.
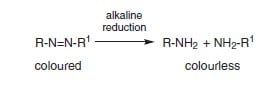
For anthraquinone, the dyes are converted into the virtually colorless, water-soluble, low substantivity, and leuco variant.
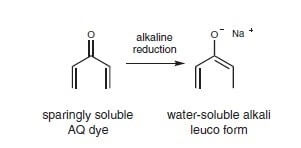
References
- K.R. Choudhury, Textile preparation and dyeing: Science Publishers, United States, 2006.
- D. Broadbent, Basic principles of textile coloration: Society of Dyers and Colourists, England, 2001
- L. Needles, Textile Fibres, Dyes, Finishes and Processes: Noyes Publication, United States, 1986.
- M. Burkinshaw, Physico-chemical Aspects of Textile Coloration: Society of Dyes and Colorists, UK, 2016.
- J. Houser, Textile dyeing: InTech, Croatia, 2011.
- N. Chakraborti, Fundamentals and practices in coloration of textiles: WPI, India, 2015.
- O. Glenz, W. Beckmann, W. Wunder, “The Mechanism of the Dyeing of Polyester Fibres with Disperse Dyes”, The Journal of the Society of Dyers and Colourists, Vol. 75, pp. 141-147, March 1959.
- Clark, Handbook of textile and industrial dyeing: Woodhead Publishing, England, 2011.
- M. Al-Etaibi, H.S. Alnassar & M.A. El-Apasery, “Dyeing of Polyester with Disperse Dyes: Part 2. Synthesis and Dyeing Characteristics of Some Azo Disperse Dyes for Polyester Fabrics”, Molecules, Vol. 21, 2016.