Microfiber : Properties | Application | Manufacturing Process
First off, there is no exact definition for microfiber. However, microfibre is commonly defined as the fiber that’s finer than one denier (1 denier per filament) or one dtex. They tend to range from 0.25-1.0 denier.
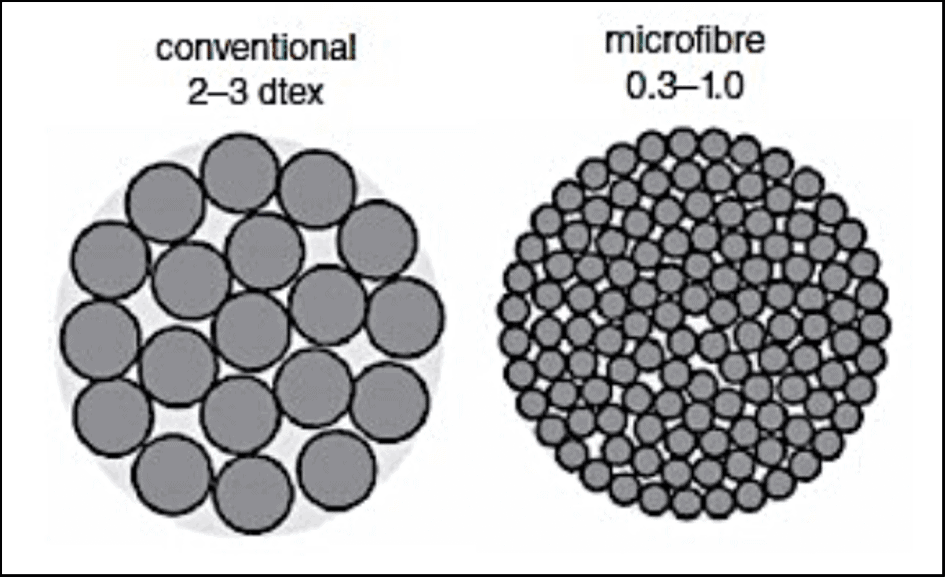
Now, from the above picture, you can clearly see that the microfiber has higher number of fibres and is more densely-packed than the conventional ones.
Let’s learn about microfiber textile in detail.
Why Is Microfiber Necessary?
We all know that synthetic fibers can not provide comfortability. Microfibres arouse a very pleasant feeling when in contact with the skin. They offer all the conveniences of the synthetic fibers, but they look like natural fibers and are very comfortable.
What Are the Properties of Microfiber?
- More filaments in yarn result in more surface area and so more compact
- Microfibres are extremely flexible, and for the same reason microfibre yarns impart excellent drapability to the fabric
- Yarn produced from microfibres show higher strength as there is a higher number of fibers per cross-sectional area
- Fabrics produced from microfibre yarn are relatively lightweight and extremely durable
- Soft and full handle, comfortable to wear
- Low weight per unit area
- Easy care as excellent resistance to wrinkle and good dimensional stability
- Waterproofness, windproofness, breathability
- Microfibre fabrics are washable and dry-cleanable
- Super absorbent, absorbing over seven times their weight in water
- Microfibre dries in one-third of the time of ordinary fibers
- Microfibre is hypoallergenic, and so does not create problems for those suffering from allergies
- Microfibre is non-electrostatic
What Are the Applications of Microfiber?
1. Clothing
Microfibres are commonly used in blouse weight garments, tailored suits, hosiery, and evening wear as the color and appearance resemble silk. It can be used to create fashionable outwear for women, fabrics with a new hand, and smooth drape.
2. Protection Against the Weather
Used to produce sportswear that can breathe but also provides windproofness and water repellency. They are also used for rain clothes and tents due to improved water impermeability and lower air permeability.
3. Synthetic Game Leather
When compared to natural leather and game leather, they show significant advantages such as excellent uniformity, dimensional stability, ease of care, colorfastness. They also show a lower mass.
4. Filtration
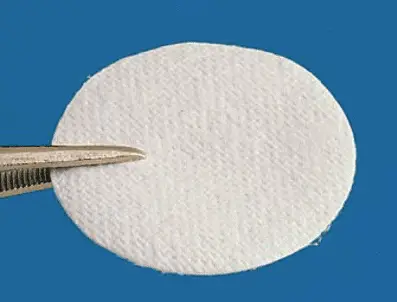
As microfiber has a very fine and compact structure, they show excellent filtration properties when used for air and fluid filtration.
5. Microfiber for Cleaning
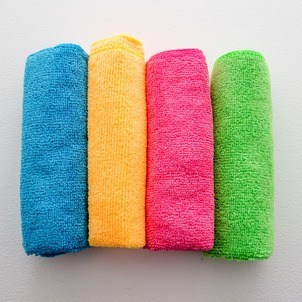
Can be used for producing cleaning cloths. Microfibre cleaning cloths trap dirt and dust inside the cloth and do not spread dust or dirt around. The user can clean the cloths with water alone; no chemicals are needed.
6. Medical Applications
They are used for hospital surgical drapes and gowns, protective facemasks, gloves, surgical packs, and bedding & linens. They are lower in cost, easier to use, more versatile, safer, and features of better disposability.
What Are the Limitations of Microfiber?
- Fabrics of microfibres are delicate and require careful treatment.
- Microfibers can be dyed, but a higher dye concentration bath is needed to produce a given depth of shade.
- They show decreased fastness to light, fastness to rubbing, water, and ozone.
Finally, What Are the Microfiber Manufacturing Processes?
Conventional spinning techniques can produce microfiber (melt, wet, and dry). But the polymerization, spinning, and drawing should be maintained carefully and strictly. Many holes of very fine diameter should be present in the extrusion spinneret.
The other processes are,
- Direct spun type
- Dissolved type
- Split type
- Super drawing technique
- Sheath-core spinning method
- Flash-spinning method
- Solution flash-spinning
- Emulsion-spinning method
- Jet-spinning method
- Centrifugal-spinning method
- Turbulent forming method
- Conjugate-spinning method
Now we will discuss some significant methods of manufacturing microfiber.
Direct Spun Type
- Produced in melt spinning technique.
- Careful selection of polymer and strictly maintained polymerization, spinning, and drawing is required.
- The spin line tension level should be kept low.
Parameters: The increase is take-up velocity, and the fiber line length between the spinner and the take-up device is required to gain minimum fineness.
Dissolved Type
- Produced from the bi-component fibers of different kind of polymers
- Thick bi-component filaments containing different incompatible polymers are spun.
- Fabrics are made from the bi-component.
- Chemical treatment with solvent dissolves one component, and the other remains as microfiber.
Split Type
- Bi-components are used, and splitting is done in filament form.
- Suitable polymer combinations are polyester/polyamide and polyester/polyolefin.
Super-Drawing Technique
- The main principle is yarn stretching.
- Drawing carried out at minimum crystallizing temperature.
- Special drawing technique (temperature range and type of heating the fiber) is maintained.
- Stable fiber with 0.5dtex can be produced.
- No molecular orientation is obtained.
Sheath-Core Spinning Method
- One component (core) surrounded by another (sheath) component is produced by mixing, melting, and mix-annealing of two polymers under specific conditions.
- The sheath portion is then removed.