Draw Frame : Functions|Drafting Arrangement|Roller Setting|Autoleveller
What is Draw Frame?
Draw Frame is the machine where the slivers are doubled or combined, blended & mixed, leveled and attenuated transiently through a series of pairs of rollers. In the drafting arrangement each pair of rollers move faster than the prior one.
The key purpose of implementing draw frames to spinning procedure is to develop the yarn quality, particularly yarn evenness through increasing sliver quality. A couple of draw frames are generally used in the dealing out of doubling and drafting of the card slivers known as breaker draw frame and finisher draw frame. In combing process, these draw frames are denoted as pre-comb draw frame and post-comb draw frame respectively.

Doubling: The practice of merging two or more slivers, roving or yarns into one. This stint is not limited to the arrangement of two units only.
Drafting: The process of decreasing the thickness or linear density of the input material by attenuation is known as drafting. The feed supplies may be lap, sliver and roving etc.
Drawing: The process of combining and attenuating the slivers simultaneously is denoted as drawing. A drafting without doubling is not a good practice for the slivers and vice versa.
Drawing= Drafting + Doubling
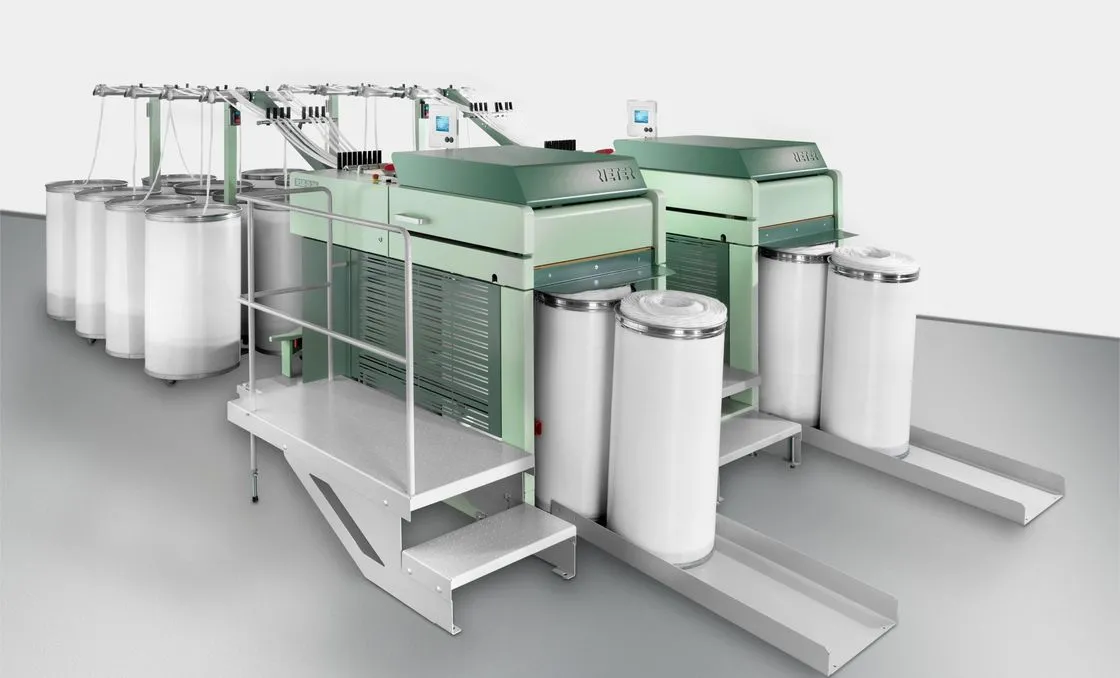
Functions of Draw Frame
Equalizing
One of the focal responsibilities of the draw frame is refining evenness over the short, medium and long term. Card slivers served to the draw frame possess a degree of unevenness that cannot be acknowledged for producing yarn.
Parallelizing
Attaining an optimum value for tenacity in the yarn, the fibers need to be aligned parallel in the fiber strands by drafting process.
Blending
Into the bargain of equalizing influence, doubling also offers a top notch of compensation of raw material disparity by blending. Here diverse types of fiber can be combined altogether to acquire a particular blend ratio. E.g. 65:35 PC, 55:45 CVC etc.
Dust Removal
The draw frame is an upright dust eliminating instrument. High performance draw frames are fitted out with proper suction systems. The draw frame extracts more than 80 % of the incoming dust.
Differences Between Carded Sliver and Drawn Sliver
Carded Sliver | Drawn Sliver |
---|---|
The fibers are oriented in all direction. | The fibers are oriented to the sliver axis. |
Sliver contain leading hook, tailing hook and both end hook. | The hooks are straightened. |
Many fibers are projected out from the sliver | Less fibers are projected out from the sliver |
Irregular weight/unit length | More regular weight/unit length due to doubling and auto leveling |
Passage Diagram of Draw Frame
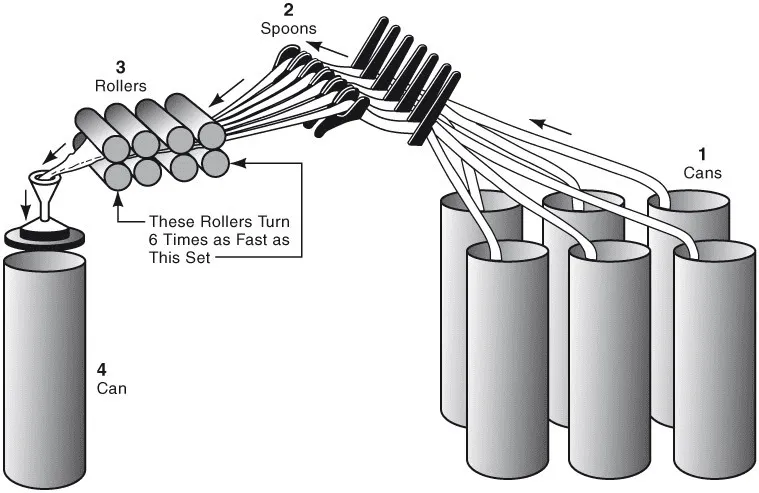
Elements of Drafting Arrangement
The primary elements of draw frame’s drafting arrangement are stated below-
1. Bottom roller
2. Top roller
3. Top roller pressure
1. Bottom Roller
Bottom rollers are made of steel driven from main gear transmission. The bottom rollers are following type:
a. Axial flutes
b. Spiral flutes
c. Knurled flutes
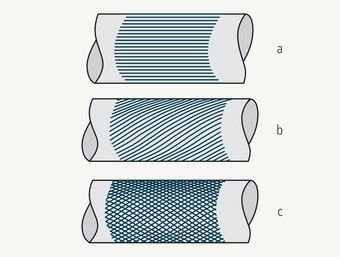
2. Top Roller
Top rollers are not positively driven. They are driven with the surface contact of the bottom roller. Top rollers are coated with synthetic rubber. The hardness of rubber should be adjusted carefully. Hardness is specified in terms of degree shore.
Soft 60-70 o shore
Medium 70-90 o shore
Hard above 90 o shore
3. Top Roller Pressure
To clamp the fibers, the top rollers must be forced at a high pressure towards the bottom rollers. The pressure can be generated by following means.
- Dead weight (Now obsolete)
- Spring loaded (The most usual form)
- Hydraulic system (Rarely used)
- Pneumatic system (Rieter)
- Magnetic (Saco Lowell)
Types of Drafting Arrangement
- Conventional 4-o-4 roller drafting system.
- 3-0-4 roller drafting system.
- 3-0-3 roller drafting system with pressure bars.
- 4-0-3 roller drafting system with pressure bars.
- 5-0-4 roller drafting system
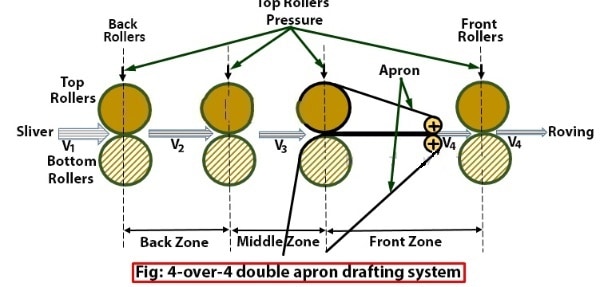
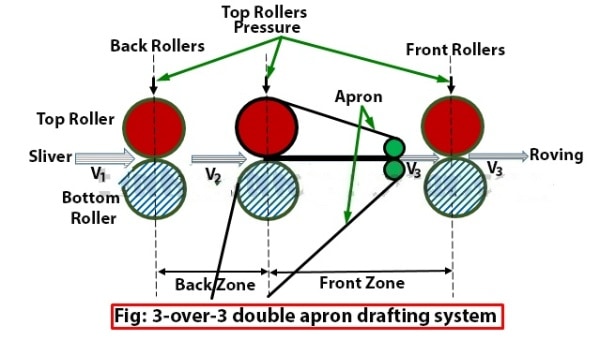
Roller Setting
The distance from the center of one roller to the center of another roller is known as the roller setting.
Principle of Roller Setting
- Longer staple length wider setting and vice versa.
- Greater the bulk of the material wider the setting.
- Faster the drafting roller speed wider the setting.
- Higher the degree of compactness wider the setting.
- For harsh and rough type of fiber setting will be wider as they don’t pass easily.
Drafting Wave
When the sliver is passed through drawing rollers the short fibers causes a succession of an alternate thick and thin place due to the irregular movement. This thick and thin place gives a wave in the surface of sliver. This wave is called drafting wave.
The amount of drafting wave depends on:
- The amount of draft.
- The roller setting.
- The doubling.
- The bulk of the material
- Degree of orientation
- Character of fiber.
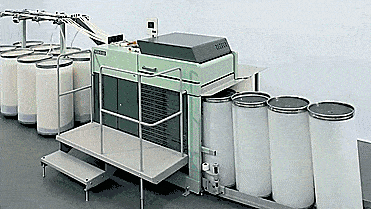
Effect of Doubling and Drafting On Sliver Irregularity
In the spinning preparation, correction of these variations is normally undertaken by equalizing or leveling or averaging effect through doubling at the draw frame. There is only a small possibility that all thin places, and separately, all thick places of slivers will coincide during doubling. Rather, they will tend to be distributed and hence to compensate each other.
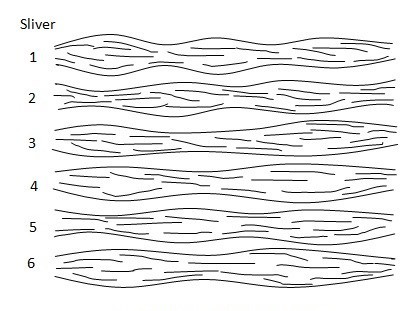
However, doubling has some limitations:
- Doubling can average out only short-to-medium term variations, not long-term variations.
- It cannot correct periodic variations when repeatedly occur side by side.
Doubling can only reduce the coefficient of variation value of any occurring variation by the root of the total number of doublings. At the input to the draw frame, the following law of doublings can be applied:
CVl = X ̅cv /√n
CVl = CV of all n slivers at the input to the drafting elements
X ̅cv = mean value of the CV values of all the single slivers
= (CV1+CV2+CV3+….+CVn)/n
n = number of doubled slivers
Example 1: A Drawframe is fed with 8 cotton slivers of 4 ktex each. Accordingly, the sum of all CVm values of the single slivers CV1+CV2+…+CV8 = 22.4%; the mean value X ̅cv is 2.8%. The irregularity CVO at the output from the drawframe is 2.5%. How large is then the irregularity which is produced by the drafting elements of the drawframe?
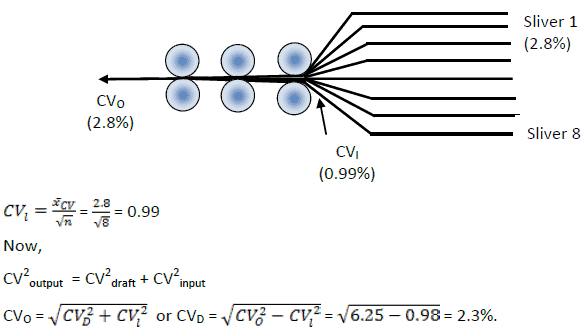
However, the doubling of fibre assemblies is undertaken primarily to introduce some parallelization between the fibres and to achieve good count constancy between bobbins. It offers, however, no possibility of drastically reducing the CVm value.
Example 2: The CV of a ring-spun yarn type is found to be 13.6% that is produced from a roving with a CV of 4%. Then the CV added by the drafting zone of ring-spinning machine is:
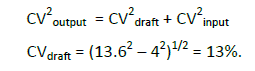
Autoleveller to Minimize Count Variation of Yarn
Purpose: The motive for the application of autolevellers at carding machine and draw frames is to uphold the complete sliver fineness that eventually decreases count variation in the yarn.
Function: An autoleveller processes the sliver width variations and then constantly adjusts the draft by servo-controlled drafting system so that additional draft is exerted to the thick places, and a reduced amount of draft to thin places with the end result that the delivered sliver becomes more even.
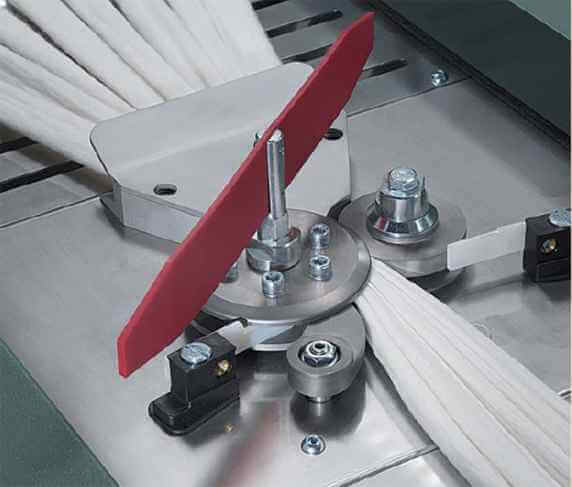
Classification: Autoleveller can be categorized into three main sets in line with the basic principle of operation:
1. Open loop autoleveller,
2. Closed loop autoleveller and
3. Combined loop autoleveller.
1. Open-Loop System
In this system, there is no measuring on final sliver. In other words the alterations in draft are uniquely established on the mass deviation in the feed material. Almost all of the autoleveller draw frames are functioning on the principle of OPEN LOOP control system.
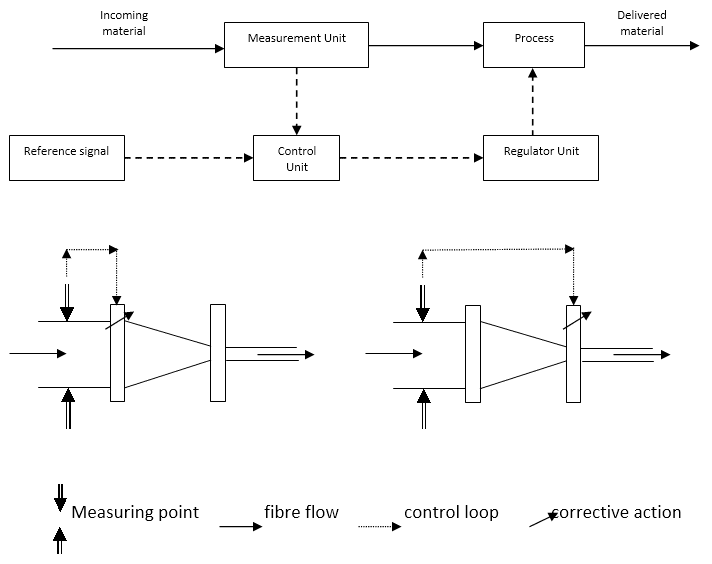
2. Closed-loop system
In this system, the checking is completed on the product of the progression i.e. on delivered sliver. In other words, the closed loop autoleveller measures the consequence of its specific accomplishment.
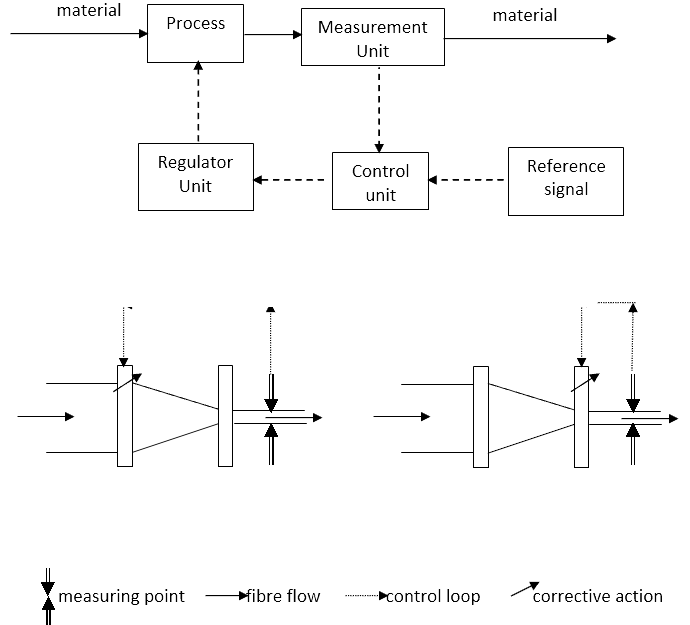
3. A Combined Loop Autoleveller
This system is premeditated to accurate long, medium, and short-term deviations. Numerous loop arrangement can be considered, for instance, the amalgamation of an open and closed loop with the intention of adjusting short-term abnormalities with a fast response (by open loop system) and long term anomalies (by closed loop system) together (Figure a). Additional arrangement may be the mish mash of two distinct closed loops (fast and slow) as shown in Figure b.
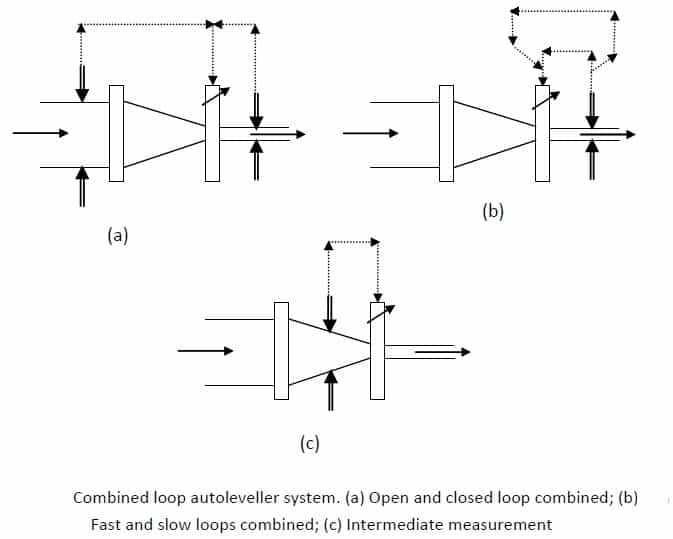
A supplementary member of this group associates both open and closed loop features arises as soon as the measurement is completed on the material of intermediate thickness between the back and front rollers of a drafting zone (Figure c). The sliver width at the point of check depends on both the feed and delivered material densities, therefore, this is a combined loop autoleveller.
Start-up Machine with Autoleveller
Mechanical draft should be chosen appropriately in autoleveller draw frames. To adopt the power-driven draft, draw frame should be started first with the autoleveller turned off. The gears should be altered so that the sliver weight is as per the need without autoleveller.
Almost all of the modern autolevellers can rectify 25% feed deviation. It is a common practice to feed 12% deviation both in thick and thin side to check A%. This is called as Sliver test. The A% should not be more than 0.75%. A% is calculated as follows; If the number of sliver fed to draw frame is N, check the output sliver weight with “N”, “N+1”, “N-1” slivers. Then,
A% = {(g/m(N-1) – g/m(N)} / g/m(N) x 100
A% = {(g/m(N+1) – g/m(N)} / g/m(N)} x 100
Advantages of Using Autoleveller
- All kind of deviations (short-, medium- and long- term) are rectified.
- Count CV% of yarn will be constant throughout the lot.
- Less thin places and thick places in the sliver as well as in the yarn.
- Ring frame breaks will reduce.
Rieter RSB Autoleveller Draw Frame (based on Open-loop principle)
Instabilities in sliver bulk of up to ± 25% can be well-adjusted by means of digital, high-precision RSB autoleveling. Variations in the physique of the input slivers are sensed by “tongue-and-groove” scanning discs. In this case the signals are composed at short, continuous intervals, as a result make sure very high precision, even at maximum speed.
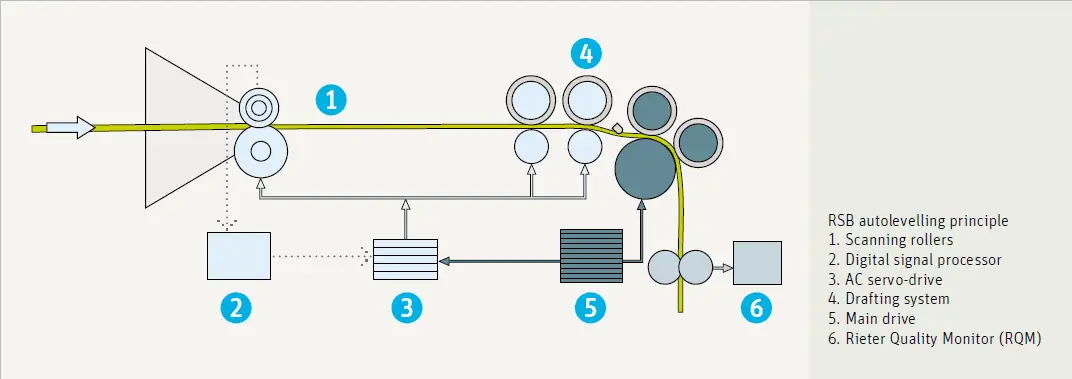
The autoleveling mainframe uses the measured signals to calculate an essential speed for the extremely dynamic AC servo drive. This assessment is conveyed to the drive precisely when the length of sliver measured touches the drafting point in the primary drafting zone. The resultant sliver is comprised without any short term, medium term or long term abnormality.
Production Calculation of Draw Frame
Problem-01:
If, Delivery roller speed =600 m/min
Sliver Hank = 0.110 Ne
Wastage = 0.5%
Efficiency = 85%
Production = ?
Solution:
Production (kg/hr) = (600*1.0936*60*0.85) / (840*0.110*2.2046)
=163.74 kg/hr
Problem-02:
Find out the DCP if,
Feed Sliver weight = 62 gr/yd,
Delivery Sliver weight = 60 gr/yd sliver,
Delivery speed = 400 m/min
No of doubling = 8
Draft constant = 320
Solution:
We know that,
Draft / Doubling = Feed wt. / Delivery wt.
Draft = (Feed wt. x Doubling) / Delivery wt.
= (62 x 8) / 60
= 8.267
Again we know that,
Draft = Draft constant / DCP
DCP = Draft constant / Draft
= 320/ 8.267
= 37.99 T
» 38 T
Frequently Asked Questions
1. What are the main differences between breaker draw frame and finisher draw frame?
The main difference between a brekaer draw frame (pre-comb draw frame) and a finisher draw frame (post-comb draw frame) is- normally breaker draw does not possess the autoleveller device where as finisher draw holds it to reduce the mass variation of slivers. There are no other such differences between the draws.
2. Why autoleveller is used only in breaker draw frame but not in finisher draw frame?
Since autoleveller is a costly device and the finisher draw frame or post-comb draw frame is the last machine to improve the sliver quality hence yarn qaulity, that is why autoleveller is used only in finisher draw frame.
3. Why doubling and drafting is done altogether?
It has been observed that due to doubling the irregularities in sliver are reduced and mass variation is average out due to multiple number of slivers. On the other hand, drafting increases the irregularities in lengthwise throughout the end product. That is why to compensate these irregularities due to attenuating, drafting and doubling are done altogether.