Parameters and Programming of Soft Winding Machine (SSM)
If you’ve read our previous articles on winding machines then you must be interested in learning the parameters that the machines take as input. These factors reflect the package that we want. By trying out different combinations, we can get to our desired soft winding recipe for a particular yarn type and yarn count. That way, you’ll be able to get the package ready as per the requirements of the best weaving looms or knitting machines.
In this article, we’ll discuss extensively on those parameters and how to program an SSM soft winding machine.
Parameters of Soft Winding
We’ll discuss the most relevant parameters, which directly influences the shape and quality of our wound package.
Yarn Length
As you already know from our previous article on Winding Speed Calculation that we can input only the yarn length, not the weight. The formula to calculate that is also mentioned in that article. Here, you need to remember the count and its relation to yarn length in mind.
It’s better to settle for lower package weight for finer count yarns. For example, let’s imagine we will make 900 gm packages with 20/1 and 50/1 yarns.
Length of 20/1 900g package = 20 × 900 × 1.69 = 30420 m
Length of 20/1 900g package = 50 × 900 × 1.69 = 76050 m
Now, do you see the problem?
The length for the 50/1 yarn is more than double the amount of 20/1. That means you’ll have an increased total surface area of yarn. As a result, there’s a higher chance of unlevel dyeing.
In these instances, consider lowering the package weight to ensure uniform dyeing.
Traverse Length
This will depend on the bobbin. Set it according to the length of the perforation of the bobbin. If you set it too high than liquor won’t pass through that protruding area with the same pressure. Thus, creating uneven dyeing.
And if you keep the traverse length lower than the perforation length then it’ll result in a pressure leak. In that situation, water will act like electric current. Most of it will flow through the uncovered holes (where’s less resistance).
Diameter
You’ll have to set two diameter values, namely –
Bobbin Diameter
There’s nothing much to explain here. Just measure the bobbin dia carefully (preferably, using a slide caliper), and put the value in.
Package Diameter
To set this value, we need to understand the spindle distribution of the carriers of our package dyeing machines. We can’t set a diameter where the packages will touch each other from the sides. Most of the time, it results in catastrophic consequences.
Thus, we must ensure that the diameter is set in a range where the packages don’t come in contact with each other from the sides when set in the carriers.
Surface Speed
It’s the amount of yarn taken up by the package per minute. And it’s directly proportional to production speed. For this reason, we want to keep this value as high as possible. But we’ll also have to pay close attention to the yarn count and the amount of tension it can withstand. Finer yarns may break repeatedly if the surface speed value is set too high. So, adjust it accordingly.
Initial Speed
Initially, the package has to start slowly to break the inertia and get up to the production speed. Plus, a higher amount of tension is applied initially to build a stable base, so the speed can’t be too high here. If so, the yarn may break repeatedly.
Production Speed
This is the speed at which the spindle operates most of the time. Thus, this will determine your production rate.
Full Package Speed
This is the speed at the final stage of the winding process. Again, we’ll have to set a lower value than the production speed. If we set it too high, the tension at the outer layer may increase too much as the tension value is higher at the final stage. Thus, it may cause the yarns of the middle layers to protrude outside. And this will lead to uneven dyeing.
Tension
Now, tension can be applied from different points at different levels at different intervals.
Initial Tension
At the very beginning, we’ll have to apply a very high amount of tension for a short time. To ensure a stable base for the package, the tension at the innermost layer should be higher than any other layer. Otherwise, the yarns will come off during handling or due to the pressure differential of the dyeing machine.
Initial Tension Time
As discussed, the initial tension should be kept for a very short period of time. In my experience, below 100 seconds is good enough.
Empty Tube Tension
After the initial yarn tension time is over, this value will be applied. You’ll have to experiment with it to get the optimum value. But from my experience, 35% − 45% should suffice.
Full Package Tension
At the final stage, the tension is kept lower than the empty bobbin tension.
Feeder Speed or Overfeed
Overfeed refers to the difference between the feed speed and production speed. It has an impact on the tension value. Check the following values and their interpretations to have a better understanding of how overfeeding works.
−100% Overfeed = The feeder will not rotate
0% Overfeed = Feed speed is equal to the production speed
+50% Overfeed = The feeder will not rotate 1.5 times higher than the production speed
Winding Type
We’ve already discussed extensively on winding technologies and their applications. You’ll have to select the type from the below options −
Precision (Winding Ratio)
For precision winding, you’ll have to select an initial and final winding ratio. Remember to select a value with fractions to avoid patterning.
Digicone (Crossing Angle)
For Digicone winding, you’ll have to select an initial and final crossing angle. Remember to the values close to each other. Too much difference in angles may create pattern zones.
How to Program an SSM Soft Winding Machine
Programming the SSM soft winder can be sub-divided into two parts. First, you have to create the recipe using a template, then you’ll have to edit the parameters to your desired settings.
Creating a New Recipe
This is an easy task once you understand the effect of the parameters. And if you’ve read the aforementioned sections carefully, you’ll find it ridiculously easy.
1. Turn the key to Enter
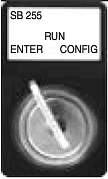
2. Select the Organize button in the Recipe function group
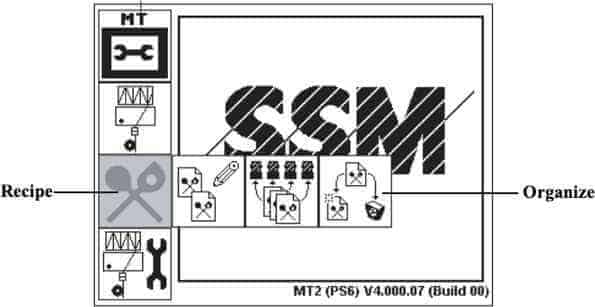
3. Now, select the New (1) button. The New Recipe menu will pop-up.
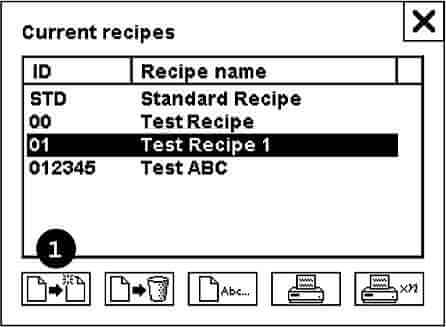
4. Select the Template button and choose an existing recipe as a pattern.
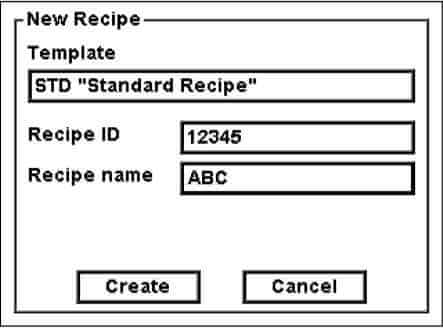
5. Tap the Recipe ID button and enter your preferred ID number up to 5 digits.
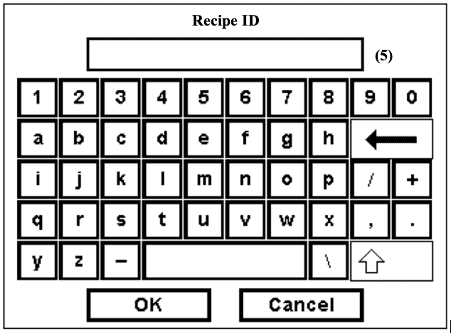
6. Select the Recipe name button and enter the required name.
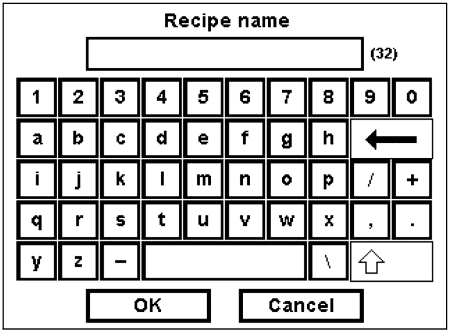
7. Tap the Create button to save the recipe
8. Now, the new recipe will appear in the list field and the parameters can be edited.
Editing the Recipe
Programming the SSM soft winder can be sub-divided into two parts. First, you have to create the recipe using a template, then you’ll have to edit the parameters to your desired settings.
1. Turn the Key to Enter
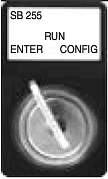
2. Select the Edit button in the Recipe function group
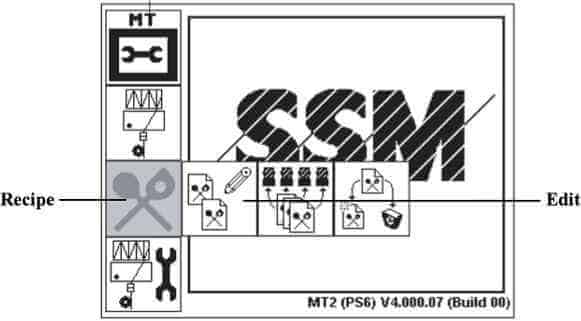
3. Call the Recipe button to display the list of existing recipes.
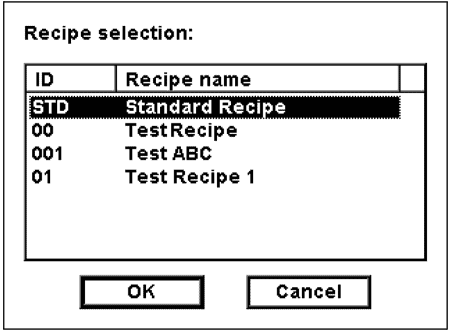
4. Each recipe is contained in a list with an ID and a recipe name. Select the recipe you wish to edit from this list.
5. Now, it’s time to get acquainted with the parameter windows. There are 8 windows in total. Once you put your required values in the following windows, the input gets saved automatically.
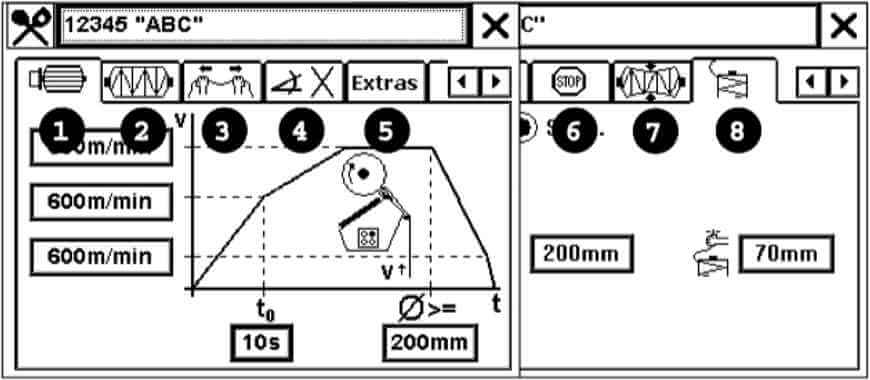
- Window 1: Drive Unit
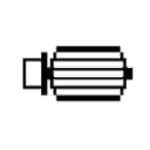
- Window 2: Package
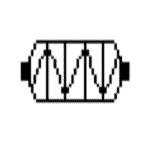
- Window 3: Yarn Tension
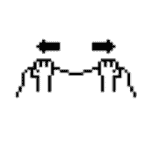
- Window 4: Winding Types
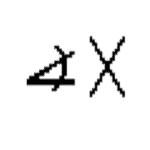
- Window 5: Extras

- Window 6: Stop
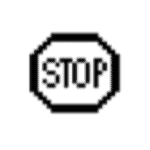
- Window 7: Density Monitoring
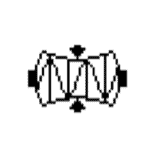
- Window 8: tensiso™
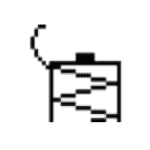
REFERENCES