Carding: Functions|Actions|Clothing|IGS Grinding|Coiling|HP Card
There are two famous sayings in the world of spinning. Firstly, ‘The card is the heart of the spinning mill’ and the secondly, ‘Well carded is half spun.’ Well, these proverbs exhibit the massive impact of carding on the ultimate outcome of the yarn manufacturing process.
What is Carding?
We can define carding as the process of lessening the entangled flocks of fibers to a filmy web by executing the flocks between two narrowly spaced, comparatively moving surfaces covered with sharp-edged wire points.
You wouldn’t find any other machine in the spinning factory that has the ability to compensate for the defects that initiate from carding. That makes it essential that the carding should accurately choose, open, clean, and parallelize fibers without degrading or damaging them.
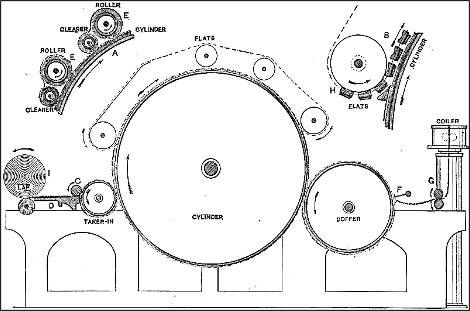
Functions of the Carding Machine
Why carding is necessary? The primary functions of the carding machine can be listed as follows –
- Individualization of the fibers and bringing them to single fiber state
- Disentanglement of the fiber neps
- Removal of the contamination of fibers
- Elimination of the trash, dust and micro dust
- Identification of the shortest fibers that lack the spinning ability and eliminate them
- Forming the fiber blending
- Formation of fiber orientation and alignment
- Generating sliver in order to facilitate the subsequent processes
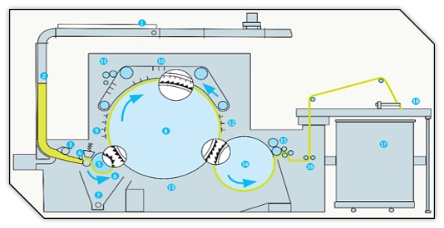
Working Principle of Carding Machine
- The raw material, i.e., the chute, is delivered by means of pipe ducting into the feed chute (2) of the carding frame. A uniformly compacted batt of about 500 – 900 ktex is made in the chute.
- A carrying roller (3) passes this material to the feeding zone (4). This comprises of a feed roll and a feed plate intended to forward the sheet of fiber gradually into the operating range of the T-in (5).
- These flocks are forwarded over the grid tool (6) and transported to the core cylinder (8). The flock material drops the majority of its contaminations. Suction channels (7) take away the impurities.
- The flocks themselves are passed along with the core cylinder and opened up into a single fiber state between the flats and the cylinder. The flats (10) consist of 80 – 116 separable carding bars joined into a belt moving on a never-ending track.
- In the course of this coming back, a cleaning component (11) takes out fibers, contaminants, neps, dirt, trash, dust, and foreign matters from the flats’ bars.
- The doffer converts the individualized and separated fibers into a web due to its considerably lower surface speed in relation to the core cylinder.
- A stripping instrument (15) pulls the filmy web from the doffer. After calendar rollers (16) have compacted the sliver to some degree, the coiler (18) dumps it in sliver cans (17).
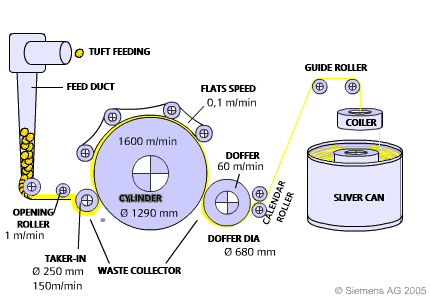
Actions in Carding
Carding Action
- This action occurs between the flat and the cylinder
- Wire direction is reversed between them
- Flat and cylinder movement directions are reverse as well.
Consequences of Carding Action
- Supreme individualization of fibers is attained in this action.
- Entanglement of fibers, short fibers, dust are eliminated
Stripping Action
- This action occurs between licker-in and cylinder; doffer and stripper as well.
- Wire direction is identical between them.
- Movement directions are reverse as well.
Consequences of Stripping Action
- Impurities and micro-dust are eliminated by stripping action.
Doffing Action
- This action occurs between doffer and cylinder.
- Wire direction is reverse between them.
- But doffer and cylinder movement directions are identical.
Consequences of Doffing Action
- To collect the singular fibers from cylinder and convert into a filmy web
- Formation of sliver is executed by this action
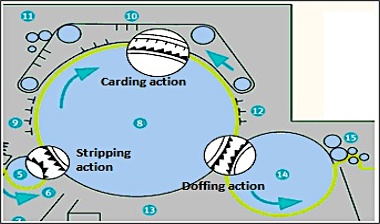
What is Card Clothing?
A number of unlimited fine, narrowly spaced, exclusively bend & sharp-edged wires are used to protect the external surface of licker-in, core cylinder, flats as well as doffer of a carding machine is said to be card clothing.
Categories of Card Clothing
1. Flexible Clothing
This provides round hooks or oval shaped hooks’ sharp edged wire that is set into elastic, flexible, multi-ply cloth backing. All of the hooks are twisted into a U-shape and are bent with a knee that moves when the bending load is applied and comes back to its primary spot when the load is detached. In the present condition, short-staple and medium-staple spinning factories use this clothing just around the flats bar.
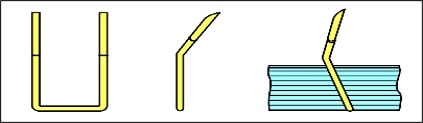
Benefits of Flexible Card Clothing
- Density of wire point is extraordinary.
- Better carding action is obtained.
- Flexibility of wire point is remarkable.
- Fiber damage is exceptionally lower.
- Not much expensive.
- These clothing are repairable.
Drawbacks of Flexible Card Clothing
- Elastic rubber or textile cloth is used as base material.
- Consistent sharpening or grinding is essential.
- High probability of teeth loss since wires are loosely attached.
- High probability of wire and foundation material degradation due to remarkable flexibility.
Base Materials Used for Flexible Card Clothing
There are mainly two types of base materials are used for flexible card clothing:
- Leather
- Plied Fabric
Leather as Flexible Card Clothing
It is the finest and utmost widely used base material.
Benefits of Leather as Flexible Card Clothing
- We don’t need oil and water to join this clothing.
- It is reasonably of superior quality.
Drawbacks of Leather as Flexible Card Clothing
- Very expensive to use.
- Elastic characteristics are not up to the mark.
Plied Fabric as Flexible Card Clothing
1. Double Ply (2 ply) Base
a) Warp – Cotton or Linen and Weft – Woolen
b) Back cloth – Cotton
2. Triple Ply (3 ply) Base
a) Face cloth – Cotton
b) Warp – Linen and Weft – Woolen
c) Back cloth – Cotton
3. Quad Ply (4 ply) Base
a) Face cloth – Vulcanized rubber
b) Cotton cloth
c) Warp – Linen and Weft – Woolen
d) Back cloth – Cotton
4. Penta Ply (5 ply) Base
a) Face cloth – Vulcanized rubber
b) Cotton cloth
c) Cotton cloth
d) Warp – Linen and Weft – Woolen
e) Back cloth – Cotton (Single)
Characteristics of Base Materials
- Satisfactory strength and flexibility.
- Adequate width and stiffness to grip the wires in their spot.
- Unaffected to lubricant, temperature, humidity and early ageing.
- Ample resiliency.
2. Semi-Rigid Card Clothing
Semi-Rigid Card Clothing resemblance to the construction of flexible card clothing. But, it occupies higher layers of cloth as well as comprises hooks of wire having squared X-sections. Here, there is no existence of a knee is in this clothing system. At times it comprises of reinforced round wire where a knee could be present.
If we compare this to flexible clothing, we see semi-rigid clothing got advantage. Flexible card clothing choke with fiber whereas it doesn’t and consequently remove less flat stripping. Furthermore, Semi-rigid card clothing does not need to grind as much as flexible card clothing needs to do.
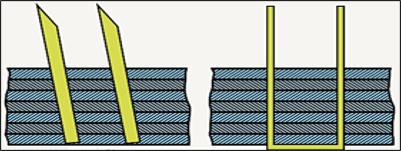
3. Rigid or Metallic Clothing
These are uninterrupted, self-sufficient wire assemblies where the teeth are cut at the minimum probable spacing. No foundation material is needed in this system. The wire appearance like saw tooth since they doesn’t possess any knee. Recently, the licker-in, core cylinder as well as the doffer are covered with metallic or rigid card clothing.
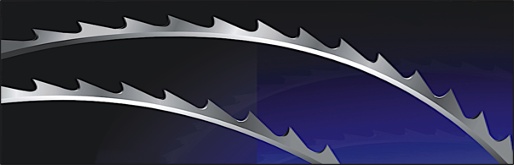
Benefits of Metallic Wire Card Clothing
- Rigid or Metallic card clothing doesn’t require any foundation material.
- Probability of teeth loose tends to almost zero.
- Rigid clothing requires a reduced amount of sharpening and stripping.
- It has the flexibility to connect each carding angle.
- Since it requires a reduced sharpening and stripping, production is much higher.
Drawbacks of Metallic Wire Card Clothing
- Metallic wire point become harsh on the fiber and damages them to a great extent.
- It is not easy to rectify the wires in the factory if needs repair.
- The entire clothing needs to rewind if any share of the wire is broken at that time.
- Rigid card clothing is very expensive to use.
What is Grinding?
The wires of taker-in, core cylinder, flats and doffer are consistently in action with fiber and its contaminants. After a certain time or definite amount of cleaning cycles, they gradually start to lose their sharpness and progressively become blunt. As a result grinding becomes essential for the card clothing wires to sustain its sharpness so that optimum cleaning can be achieved.
Significance of Grinding
- Maintaining the optimum sharpness of the clothing wire points.
- Retaining the identical stature of the wires points.
- Achieving consistent carding action and even sliver constantly.
Categories of Grinding
- Traverse wheel grinding
- Long roller grinding.
Integrated Grinding System (IGS)
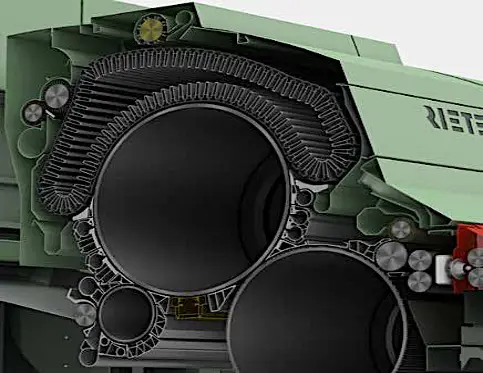
Rieter, Switzerland offers a unique feature that is Integrated Grinding System (IGS) that makes sure uniform quality card sliver as well as increases the serviceability of the card.
The repeated wear of the card clothing start to lose the sharpness as the production gets higher. The Integrated Grinding System (IGS) resolves this situation exact from the beginning by maintaining the clothing eternally sharp.
In the IGS-classic, a grinding rock is mechanically progressed across the cylinder clothing in the course of production. This action is executed 400 times over the anticipated service life span of the card clothing.
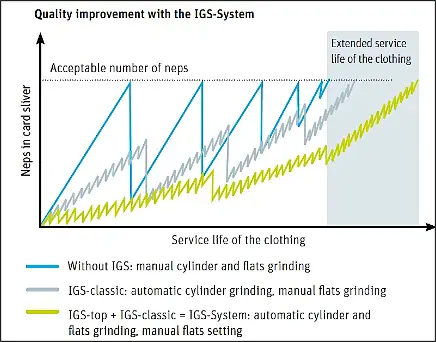
The IGS-top hones the flats’ card clothing entirely mechanically. The control component estimates the grinding cycles over the pre-elected service life time of the flats’ card clothing. Several minor grinding actions make sure that the quality is more constant than in a flat grinding roller.
We can prolong the life phase of the cylinder clothing by 10 – 20% in all executions by means of the usage of IGS-classic. Moreover, we may offer the management a vibrant fund added from the lesser repair requirements. Furthermore, we can use the machine stoppage time required for labor-intensive grinding.
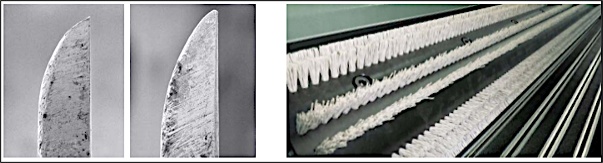
Mounting: Mounting is the process of setting new wire around the carding parts like taker-in, core cylinder, and doffer, etc. rather than repairing the existing one. Similarly, we execute mounting when the grinding is not enough to sustain the optimum quality of the delivered materials.
What is Coiling?
The procedure through which a sliver is dumped, collected, and stored in sliver can like a coil shape is called a coiling mechanism.
Significance of Coiling
- The motive of coiling is to place the compressed sliver in a well-ordered method in a cylindrical sliver can.
- While unraveling slivers from the deposited cans at the next process they come out without becoming knotted or overextended.
Categories of Coiling
Over Center Coiling
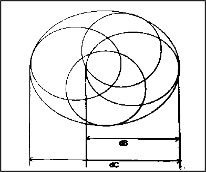
The coiling system where the radius of the can is smaller than the diameter of circle of the sliver is said to be over center coiling. Normally for over center coiling, we use Small to medium shaped cans.
Under Center Coiling
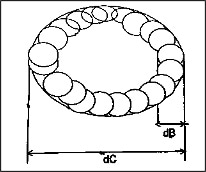
The coiling system where the radius of the can is greater than the diameter of circle of the sliver is said to be under center coiling.
Neps Removal Efficiency (NRE)
The neps/gram which is eliminated from the carding machine is stated as proportion to the neps/gram in the carding matt is known as the NRE i.e., neps removal efficiency.
NRE%= {(Neps/gram in Feed Material – Neps/gram in Delivered Material) ÷ Neps/gram in Feed Material} x 100%
Differences Between Carded and Combed Yarn
Following are the differences between carded & combed yarn –
Carded Yarn | #SL | Combed Yarn |
---|---|---|
We attain this yarn lacking combing. | 1. | We attain this yarn by combing. |
Comparatively the eminence of carded yarn is not up to the mark. | 2. | Combed yarn is superior to carded yarn in terms of quality. |
Higher percentage of short fiber is present. | 3. | Comber combs out the short fibers. |
No need to use lap former. | 4. | We need to use super lap former. |
Comparatively the tensile properties of carded yarn is not up to the mark. | 5. | Combed yarn is superior to carded yarn in terms of strength with same TPI. |
Irregularity is comparatively higher. | 6. | Combed yarn is more regular. |
Technical Data of Three High-Performance Cards
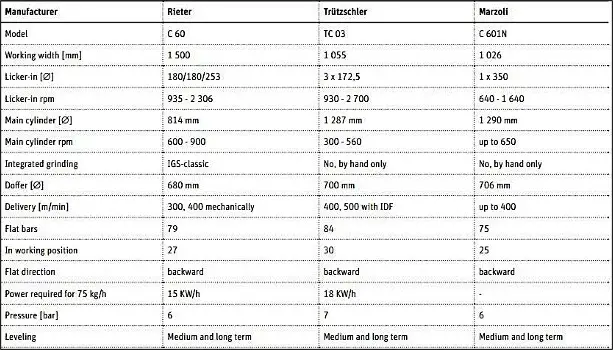
Rieter HP Card C 75 Machine Data
There are carding machines that are able to produce 100 kg/hr card sliver or more. We call them HP card. HP stands for High Performance or High Production. Rieter C 75 is a HP card. This is one of the state-of-the-art machine. Here some data are provided regarding the machine.
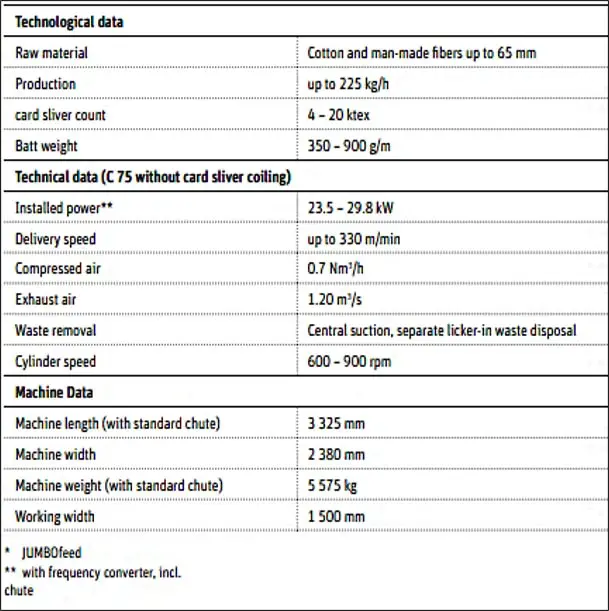
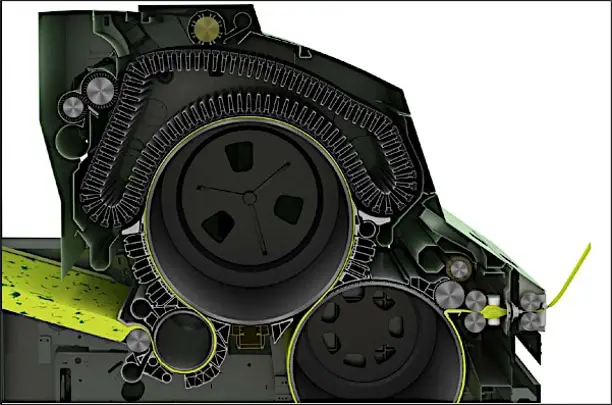
Card Production Calculation
Problem-01: If, Delivery roller speed = 220 m/min;
Sliver hank = 0.09 Ne;
Efficiency = 85%;
Find out the production of carding machine.
Solution:
Production (kg)/hr = {(220 x 1.0936 x 60 x 0.85) ÷ (840 x 0.09 x 2.2046)} kg/hr = 73.62 kg/hr
Problem-02: Find out the production per day in lbs. of a modern carding m/c
From the following data –
Doffer speed = 200 m/min;
Delivery sliver weight = 68 grains/yd;
Waste = 3%;
Efficiency = 95%:
Tension draft =1.1
Solution:
Production per day = {200 x 1.09 x 60 x 24 x 68 x 0.95 x 1.1 x (100-3)} ÷ (100 x 7000) lbs = 3091.13 lbs
Problem-03: If, Lap hank = 0.012 Ne;
Sliver hank = 0.11;
Find the draft of carding machine.
Solution:
Draft = Delivery ÷ Feed = (0.11 ÷ 0.012) = 9.16666
Frequently Asked Questions
What is the prime function of a carding machine?
The primary function of the carding machine is to individualize the fibers from the batt. Here, carding brings the material into the single fiber stage. Since it separates all the fibers completely and hence the neps i.e., entanglement among the fibers are also eliminated from the material. This action occurs between the reversal movement of flats and cylinder.
Why carding is called the heart of spinning and well card is half spun?
If we observe the imperfections of a yarn, we will found that there are some major faults such as thick places, thin places, neps, slubs, hairiness, etc. Among all of them, neps is the most dangerous one. And carding helps to remove this fault.
So, if we don’t remove the neps properly in carding, then this fault will exist in the whole process like in the fabric production, dyeing, printing as well as finishing. And lastly, at the winding the number of cuts by the EYC, i.e., electronic yarn clearer will be exceptionally high. The splices in these cuts will generate more faults.
So, it is clear that if neps remain even after the carding, then it will deteriorate the final yarn to such extent that the yarn will become of no use. That is why we call carding the heart of spinning. And well card is half spun.
Why Rieter Card C 75 is much ahead of its competitors?
Rieter Card C 75 has the highest working width than any of its competitors, and this unique feature makes it become the most productive card in the spinning industry. It also provides more ACI that is active carding index; besides, it also provides Integrated Grinding System (IGS), which prolongs its clothing’s service life to a great extent.
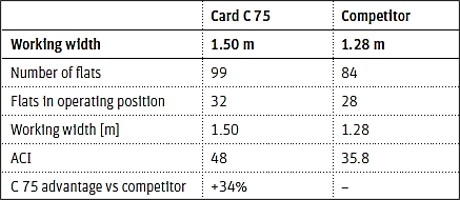
What is the usual production rate of a carding machine?
Generally, it depends on the raw material quality, the carding machine’s performance quality, and the required parameters of the end product. But then again, in conventional machine’s man-made fibers provides more production rate than cotton fibers in the spinning mills.
Management keeps production rate a little lower than its capacity for achieving greater quality. But nowadays, with the introduction of HP cards, production has gone beyond even more than 100 kg/hr.