Blowroom Machinery | Rieter Blowroom Line
Blowroom is the place where the spinning preparation begins. It is the initial step of yarn manufacturing. Firstly, opening the fibers into small tufts, then cleaning the trash out of the fibers including micro dust thoroughly and furthermore, blending them homogeneously with different grades of fibers altogether are the prime functions of blowroom.
Blowroom is comprised of a number of machines which serves a number of actions to provide properly opened, perfectly cleaned and uniformly blended fiber. In majority of the spinning mills all over the world, spinners use the blowroom line of either Rieter, Switzerland or Trutzschler, Germany. Well, both of them have established their reputation in the world spinning to a great extent. In this article, the blowroom line of Rieter will be discussed and most of its major machinery as well.
Rieter Blowroom Line
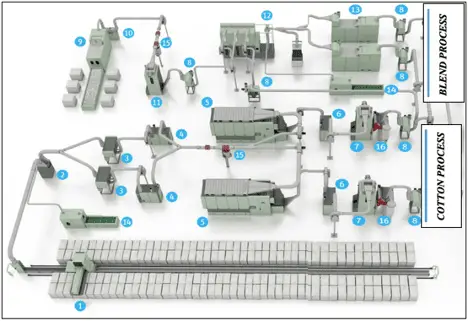
1. UNIfloc A 12; 2. Solid matter extractor A 49; 3. Condenser A 22; 4. UNIclean B 12; 5. UNImix B 76R; 6. UNIclean B 17; 7. UNIstore A 79R; 8. Condenser A 21; 9. Mixing bale opener B 34; 10. Solid matter extractor A 48; 11. UNIstore A 79S; 12. UNIblend A 81; 13. Mixing opener B 33; 14. Waste opener B 25; 15. Combo Shield; 16. Vision Shield;
Functions of Automatic Bale Opening Machines
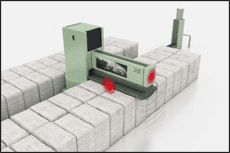
- Firstly, collecting material consistently from all the bales;
- Secondly, progressively opening the material smoothly;
- After that, opening up to the smallest flock;
- Besides, formation of tufts and micro-tufts;
- Moreover, interact with maximum bales in a single movement;
- Furthermore, it is universally appropriate, i.e. easy to operate;
- Hence, intermingle fibers right at the beginning of the process;
- Thus, allow fiber blend from numerous constituents (fiber origins).
Rieter Bale Opener UNIfloc A12
The A 12 is an exceptionally tough and steady novel invention. Bale profiling method of the UNIfloc A 12 uses distinctive technology. This equipment delivers impressive manufacturing quality from the start.
The bale opener is responsible for good cleaning in the blowroom. It eliminates awfully small tufts and micro-tufts from bales. These micro-tufts are de-dusted and the impurities in them are removed much more proficiently in the later processes.
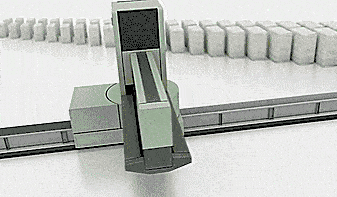
UNIfloc A 12 courses both natural and synthetic fibers to a primary length of 65 mm. The bales to be engaged off in a crosswise or transverse way on both right and left sides of the UNIfloc. The bale opener courses up to 4 diverse varieties.
Besides, the arrangement of the take-off unit containing the exclusive dual teeth and the grid confirms that the fibers are progressively opened up and gradually converted into micro tufts. For the period of each run, the take-off roller drops by a predetermined value. A fan pulls in the small flocks of fibers and pneumatically delivers it to the subsequent machine.
Rieter UNIfloc A12 supports more than 160 bales in a laydown and up to four segments (different bale types) per blend over a supreme bale layout measurement of 46 m to be processed. The A12 can course one blend or up to 3 blends instantaneously. The manufacturing rate is as much as up to 2400 kg/hr.
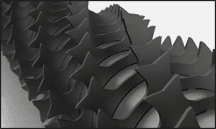
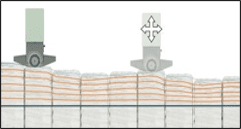
The feeding container and a pair of bottom rails are held to the floor. A frame, which travels to and fro on the guide rails, conveys a turret (2) that revolves through 180° and supports a fiber collecting assemblage (3) which can be elevated, pull up and down. The latter has independently changeable double-teeth and alters its course of revolution on reversal of the track of rotation of the frame, so that fibers can be collected in both ways of its route. Working principle of UNIfloc bale opener
Well, A microchip is delivered for entirely automatic collection of fiber from the bales. The manufacture rate and the entire weight of feed material can be go in manually on the statistical keyboard. On the source of the mechanically sensed bale heights, the device then analyses all data necessary for completely automatic operation, comprising the penetration distance for extraction. The bales are arranged out to the both sides of the machine and
- Fibers can be extracted from both right and left sides instantaneously into a single blend;
- From all sides at once into multiple blends or after a specific side only
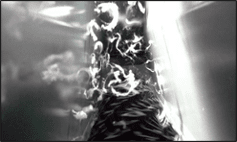
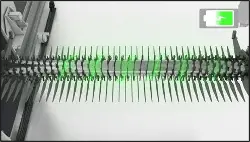
Technological Data of Rieter Bale Opener (UNIfloc A12)
Material | Cotton, man-made fibers up to 65 mm (2 1/2 inch) staple length | |
Production output* (maximum) | Cotton and viscose | Man-made fibers*** |
Range 1 | 2400 kg/hr | 2000 kg/hr |
Ranges 2 | 1800 kg/hr | 1400 kg/hr |
Ranges 3 | 1400 kg/hr | 1000 kg/hr |
Technical Data of Rieter Bale Opener (UNIfloc A12)
Design variants of the take-off unit | 2300 mm | |
Installed power | 17.4 kW | |
No. of bales per side | 1.5ML and 3ML B L | |
Net weight (10.00 m) | 4 050 kg | |
Additional duct length | +88 kg/m |
Machine Data of Rieter Bale Opener (UNIfloc A12)
Material feed Length (ML) | 6.0 – 46.0 m** |
Duct length | 10 – 50 m** |
* Line production (card production)
** in increments of 2.5 m
*** Depending on the type of man-made fiber, production can be lower (e.g. bulky polyester)
Abbreviations: ML= material feed length; B= bale width; L= bale length.
Rieter Pre-cleaner UNIclean B 12
The UNIfloc delivers micro tufts of fiber. The UNIclean makes the best usage of this large surface area. Positioned straightaway downstream of the bale opener, the UNIclean eliminates slack waste particles, fiber impurities and dust. It is intended for rigorous coarse cleaning.
The later progression stages have to get rid of only a minor fraction of the impurities. So, Simultaneously the fibers are cleaned smoothly. Results in run-through have exposed fiber realization to be up to 2% greater than conventional blowroom lines.
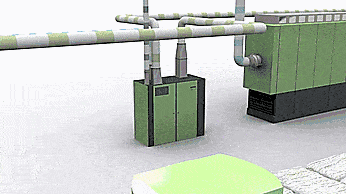
Besides, The elementary design links to that of the single cylinder cleaner, i.e. here is a feed channel at the top position (4), a big cleaning cylinder (1) with exceptional hooks, a waste draw device and an exit pipe (5). But in place of the fiber revolving three times inside the coarse cleaner, it’s enforced to circulate over and around the grids five times which always provides fresh surface areas to it. The micro tufts not only rotate over and around the grids five times but they also revolve over a specifically organized perforated area for five times. The compartment behind this sheet is a low-pressure hollow. The compressed air drag through this pane provides precise effective dedusting.
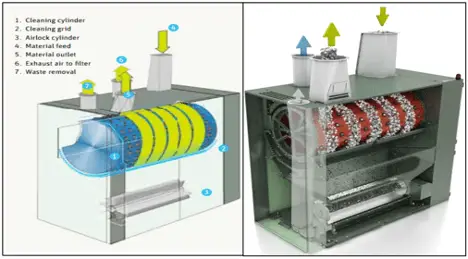
The trash and impurities are composed inside the cleaner and served to the waste transport by means of an airlock cylinder. Both link to constant suction and intermittent suction is available. The airlock restrains quality fibers from being sucked by the grid all through waste removal.
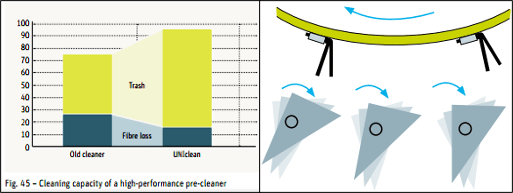
Hence, progressive fiber cleaning denotes cleaning only to the degree essential. The amount of cleaning points involved rely on the grade of impurities and trash. This saves the material from any excessive stress. Thus, fiber damage and length shortening are controlled. All the models of Rieter cleaning equipment, contamination is dug out intermittently. This collection technique inhibits quality fibers from being entered into the trash flow unintentionally—these consequences in raw material investments.
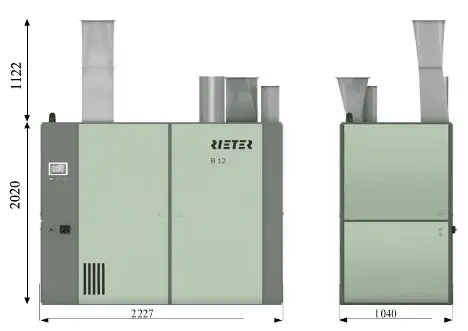
Technological Data of Rieter Pre-cleaner (UNIclean B 12)
Material | Cotton, cotton waste, linen |
Production volume | up to 1 400 kg/h |
Technical Data of Rieter Pre-cleaner (UNIclean B 12)
Installed power | 15.25 kW |
Connection values | 380/400 V, 50 and 60 Hz |
Machine Data of Rieter Pre-cleaner (UNIclean B 12)
Working width | 1 600 mm |
Clearer roller ∅ | 750 mm |
Speed | 480 – 960 rpm |
Length | 2 227 mm |
Width | 1 040 mm |
Height | 2 020 mm |
Weight | 1 185 kg |
Rieter UNImix B 76
The compressed mixing instrument B 76 is served from the pre-cleaner or straight from the bale opener UNIfloc A 12. The fibers are uniformly dispersed through eight mixing compartments. Due to unique three-point mixing progression, both natural and synthetic fibers are consistently mingled. To some extent, errors with the bale arrangement are compensated by the refined mixing process. The enormous storage size confirms a consistent feed to the subsequent blowroom machines. It can deliver up to 1200 kg of materials per hour.
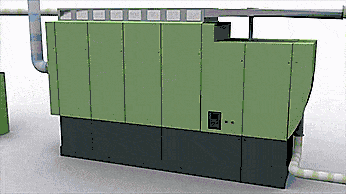
So, the fibers are consistently mixed at three diverse points:
- Micro tufts are fed through to the right angle of the duct. This origins the eight wavy layers in the direction of swing spatially and temporally. The result in a distinct long-term blend.
- The spikey lattice eliminates flocks from all the wavy layers all at once. This tender opening process outcomes in an additional, haphazard mixing of the tufts. The blend is by this time homogenously done at this phase.
- The remained tufts experience a third thorough mingling process in the mixing roller unit. This supplementary mixing process increases the fiber mingling even better.
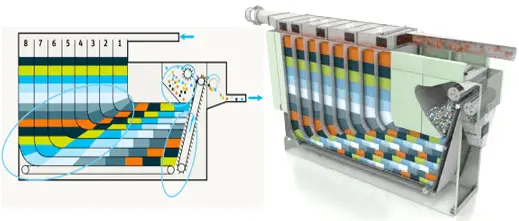
Since the absence of a mechanical modification point in the UNImix, therefore, it is stress-free to maintain. The space between the evener roller and the spike lattice, for instance, can be fixed at the operational unit, keeping the necessary manufacture output. The standards for raw materials and manufacturing settings can effortlessly be altered on the device display even though the machine is running. These conditions are replicate-able and thus upkeep contemporary quality supervision.
The amount of fiber clump opening can be enhanced for the raw material and whirl mechanism used. This is attained by means of the revolving speed and course of the mixing roller. The factors can be simply fixed on the instrument display.
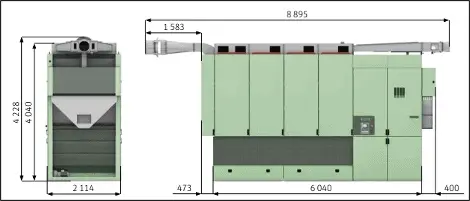
Technological Data of Rieter UNImix B 76
Material | Cotton, man-made fibers and blends |
Production volume 1) 2) | Cotton up to 1 200 kg/h, man-made fibers up to 1 000 kg/h |
Number of chambers | 8 |
Technical Data of Rieter UNImix B 76
Installed power | 4.7 kW |
Opening roller speed | 500 – 610 rpm |
Take-off roller speed | 660 rpm (constant) |
Spiked lattice | 21.6 – 216 m/min |
Feed belt | 0.0 – 0.7 m/min |
Machine Data of Rieter UNImix B 76
Length | 8 895 mm |
Width | 2 114 mm |
Height | 4 228 mm |
Working width | 1 800 mm |
Net weight | 5 515 kg |
- Line production (card production)
- If the blend has a high amount of waste or noils, i.e. more than 40% short fibers, the maximum production will be 800 kg/h
Rieter UNIblend A 81
The meticulous blender UNIblend A 81 arrangements the utmost quality for multi-component blends. Raw material proportions are assorted at a maximum amount of precision. An abnormality in the blending proportions of not more than 1% is definite.
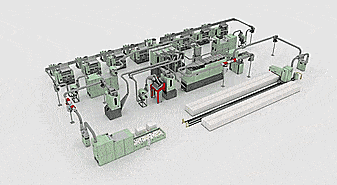
The blending machines stated above generate random blends. They are outstanding machines for blending single type of fibers (even though with some diversities), e.g. cotton, or only single color shade. Yet, they are inadequate when combines dissimilar constituents (e.g. cotton and polyester), or diverse shades are essential. These blends are formed primarily on breaker drawing frames, but then again can be formed in the blowroom as well. For these extraordinary circumstances, Rieter proposes its A 81 UNIblend.
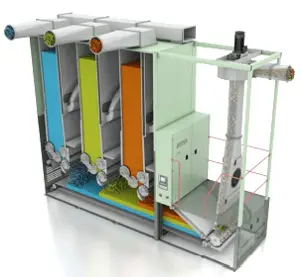
The UNIblend A 81 is similarly appropriate for average and extraordinary blends. It courses cotton, synthetic fibers, trash material as well as a varied sort of staple fibers, for instance, flax fiber with a length of up to approximately 65 mm. The extensive range of uses of the A 81 indicates that superior yarn formations are possible.
Dyed cotton fiber, uncommon and costly fibers or extreme blends, for instance, 98% to 2% can be carefully treated into special yarns. Cleaned fibers are served into the UNIblend A 81 in small, accurately defined measurements. Raw material expenses are condensed accordingly, and a uniform yarn quality is assured.
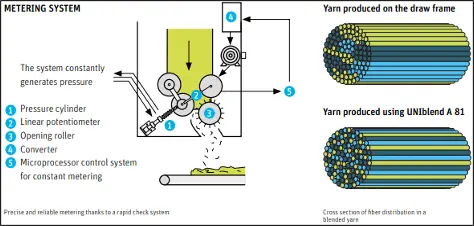
Well,the A 81 contains up to eight blending segments. Each section comprises a self-regulating, Rieter-patented metering method. This method produces a uniform fiber movement. One of the feed rollers is mobile and is compelled against a different roller, secure, roller with a uniform power. The leveling system senses any variation in material width initiated by diverse bulks and alters the rpm of the roller. As a result, the material movement is always constant.
Besides, One A 81 can manufacture up to four diverse blends, and that is why it can serve up to 4 dissimilar carding lines at the same time. Moreover, it handles several different staple fibers. So, this allows for a swift and cost-effective reaction to fashion drifts. It can deliver up to 1000 kg materials per hour.
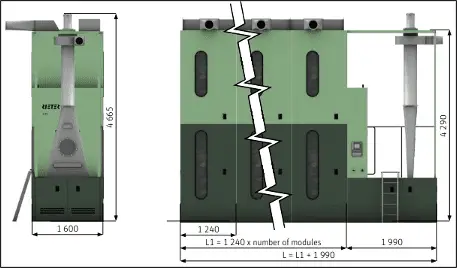
Technological Data of Rieter UNIblend A 81
Material | Various staple fibers up to 65 mm (2 1/2”) |
Production (dependent on mixing ratio): | |
– Module | 3 to 300 kg/h |
– Machine | up to 1 000 kg/h |
Technical Data of Rieter UNIblend A 81
Installed power: | |
Machine + two modules | 10.9 kW |
Plus for each additional module | 2.3 kW |
Machine Data of Rieter UNIblend A 81
Working Width | 1 200 mm |
Length | 4,470 mm – 11,940 mm |
Width | 1,600 mm |
Height: | |
Low version | 3,919 mm |
Standard version | 4,665 mm |
Weight: | |
1 module | 1,560 kg |
Opening Unit | 1,210 kg |
Control Unit | 250 kg |
Suction System | 220 kg |
Rieter B 60 UNIflex Fine Cleaner
A fan collects the micro tufts by means of suction from the previous machine and a revolving component discharges them into a filing chute (1). The back partition of the chute comprises of specific aluminum lamellae with slot-openings over which the compressed air can discharge (fist dedusting step). Hence a very consistent batting laydown is formed both in longitudinal and traverse direction. The variable chute depth regulates the lap weight necessary liable on production and nature of fiber.
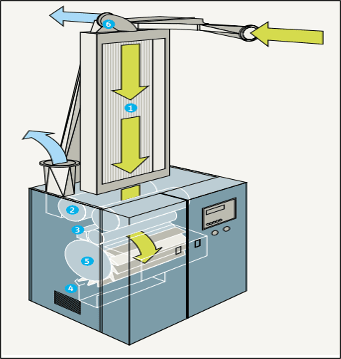
The chute is taken advanced by a perforated drum (2) (second dedusting step) and a plain drum. The instrument is armed with spontaneous lap intake. Thus no manual interference is desirable when initiating the fine cleaner. The displacement between feed roll (3) and opening cylinder (5) is adjusted by the program design to the material being processed. Thus, the feed trough supplies the material to the opening cylinder. The opening cylinder, which is accessible in diverse versions depending on the necessities of the material, takes over the material.
Using VARIOset, the spinner can set the revolution speed of the opening cylinder in accordance with his purposes and raw material. A grid bar (4) made of carding fragments and knives generates the cleaning surface and removes impurities. The carding fragments on the knives upsurge the amount of opening and subsequently, the cleaning. Once again, the operator can modify the setting of the knives on the grid in accordance with his purposes and raw material using VARIOset.
Rieter UNIstore A 79
The UNIstore A 79 is served from the upstream instrument through a dust collector or condenser. Firstly, The fibers come into the UNIstore storage component. Secondly, this section generates a material stock (buffer) and after that serves the S or R module. Hence, the A 79S variety processed the opening of man-made or synthetic fibers and the A 79R edition is required for the opening and cleaning of natural fibers. Furthermore, the material gets dust free as it goes into the dust collector, the perforated container of the condenser. Thus, at that time it is moderately opened and/or cleaned.
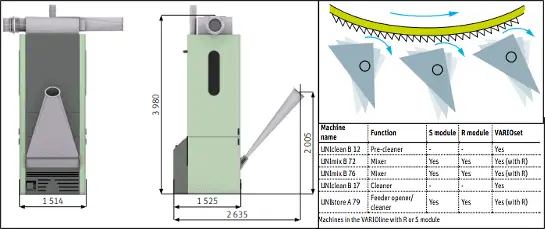
VARIOset can be encoded to get the maximum cost-effective settings for individual fiber material. The machine is extremely dynamic and courses up to 1000 kilograms of fiber per hour. The A 79 stocks up to 15 kg of clumps. This assures uniform delivery material for the cards.
Technological Data of Rieter UNIstore A 79
Material | Cotton, man-made fibers and regenerated material up to a staple length of 65 mm (2 1/2”) |
Production* | up to 1 000 kg/h |
Installed power | 12.6 kW |
Technical Data of Rieter UNIstore A 79
Installed power |
12.6 kW |
Machine Data of Rieter UNIstore A 79
Working width |
1 200 mm |
Opening roller ∅ |
320 mm |
Storage capacity |
15 kg of cotton; 10 kg of man-made fibers |
Dimensions | |
Length |
1 525 mm |
Width |
1 514 mm |
Height |
3 980 mm |
Net Weight | |
A 79S |
1 820 kg** |
A 79R |
1 870 kg** |
* Card line production
** With saw tooth rollers
Cleaning Efficiency of Blowroom
Cleaning Efficiency = {(Original Trash Content – Trash Content in the Delivered Cotton) x 100} ÷ Original Trash Content
Problem:
The trash content of a cotton is 3.6%. The waste extraction is 2.5%, of which 80% is trash. What is the cleaning efficiency?
Solution:
Of the 2.5% waste extraction,
(80÷100) x 2.5% = 2 % of the original trash has been taken out by beater.
Trash content in the delivered cotton = (3.6 – 2) % = 1.4%
Cleaning Efficiency = {(Original Trash Content – Trash Content in the Delivered Cotton) x 100} ÷ Original Trash Content
= {(3.6–1.4) x 100} ÷ 3.6 = 61.11%
Frequently Asked Questions
1. How cost effective is Rieter’s blowroom line?
The arrangement of microtufts, varioset and progressive cleaning creates the economic benefit to the spinner and save up to 1% of raw material cost. Liable on the prices of raw materials, savings on raw materials of under one percent are already value more than 10000 USD per year.
2. How quality consistent is Rieter’s blowroom line?
- Firstly, the fine quality of the fiber clumps is identified through the 312 dual teeth of the take-off roller and their revolving speed. Besides, constant and uniform take-off of the bale laydown material is additional requisite for even micro tufts. This is attained by the take-off component of the UNIfloc A 12, which traverse over the bales and identifies the scanning. The gradual opening of fibers keeps the quality intact.
- Moreover, the fibers are saved from any excessive stresses. The fibers have smaller quantity neps than with traditional blowroom systems. Fibers kept away from being shortening. The yarn is greater-quality and this has an obvious consequence on operating behavior for the duration of additional handling.
3. How energy efficient is Rieter’s blowroom line?
It has been claimed by the company that the VARIOline blowroom line by Rieter consumes around 40% less energy than solutions from other providers. For instance,
- Firstly, high energy effectiveness drives are set up in the bale opener UNIfloc A 12. This drive idea is built on torque-regulated servomotors. Energy depletion can be lessen by means of the machine’s in-built power recovery. The power-assisted brake, generated in the reversal of the take-off roller, is sent back into the electricity grid. This is one of the modifications that marks the A 12 exceptionally energy-efficient.
- Besides, the finest assortment and locating of the fans in the VARIOline confirms that the fiber material is conveyed in an effective, energy-efficient method.
- Moreover, the Smartfeed utility is incorporated into the UNIcontrol system manager. Smartfeed always maintains and enhances the flow of fiber. This decreases energy utilization.