Understanding Different Types of Yarn Winding Technologies & Their Applications
Irrespective of the type of production plant, winding technologies are employed in various stages of the manufacturing process. And among all of them, it’s the yarn dyeing plant which continues to boast the very best that this technology has to offer.
However, it’s not a surprise as the requirements of a soft-wound package is very stringent. Any irregularities in these packages may result in catastrophic consequences – resulting in the stoppage of the entire production chain.
So, without further ado, let’s get to know the different yarn winding technologies and their intended purpose.
What is Winding
Basically, it’s the process of storing a material (yarn, sliver, etc.) by any preferred form (cone, cheese, pine, spool, etc.) to facilitate further processing. The requirements mainly depend on the subsequent process it’s going to go through.
What is Soft Winding
The package yarn dyeing machines require a suitable form of package that’ll meet the machine and processing specifications. For example, the input package density, dimension, form, etc. vary from machine to machine. Thus, the yarn package must be made in accordance with those specifications.
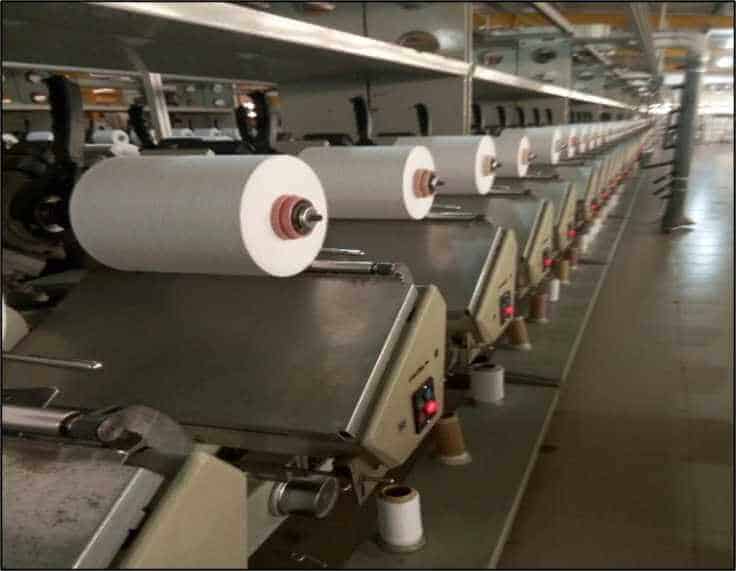
So, in simple words, we can say it’s the process of winding yarn packages to different types of bobbins according to the dyeing machine’s requirements.
Preferred Winding Technology in Soft Winding
- Precision Winding
- Step-Precision Winding or Digicone Winding or Hybrid Winding
What is Hard Winding
Here, the dyed yarn is wound as per the fabric manufacturing machine’s requirements, such as knitting or weaving machines. The requirements here are a little less stringent compared to the parameters of the soft winding section.
Parameters Required to Specify Cone Packages
- Traverse Length
- Base Diameter
- TaperThe most widely used tapers are 3º30′, 4º20′, 5º57′, 9º15′
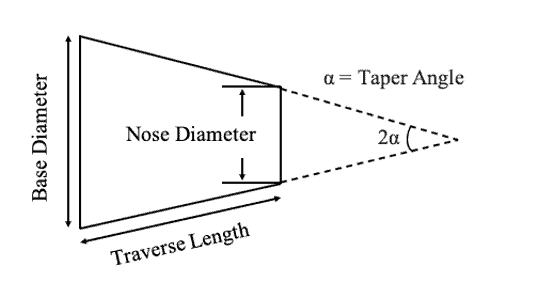
Parameters Required to Specify Cheese Packages
- Traverse Length
- Diameter
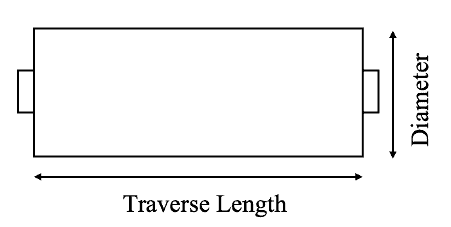
Generally, cone packages are preferred for most of the subsequent processes. This way, we can avoid friction while unwinding the yarn from the package.
Preferred Winding Technology in Hard Winding
- Non-Precision Winding or Drum Winding
Terminologies Related to Winding Technology
Before getting into the types and details, we must get acquainted with three terminologies first that are vital to grasp the concepts.
Winding Angle | Crossing Angle | Coil Angle
To define the winding angle, first, we have to visualize a plane that is perpendicular to our bobbins axis. Now angle that is made between the wound yarn and that axis is called the winding angle.
A = Winding Angle and B = Crossing Angle
You can just double the winding angle, aka angle of wind, to obtain the crossing angle of the yarn. However, don’t confuse it with the coil angle. The coil angle is made with a plane that is parallel to the bobbin.
Winding Ratio | Traverse Ratio or Wind per Double Traverse
The winding ratio simply means the number of rotations made by the yarn package while the feeding guide moves from one end to another (single traverse). In other words, it’s the number of coils laid on the package by a single traversing motion of the guide.
Now, the traverse ratio is also known as wind per double traverse because it’s just double of winding ratio. That means, it’s the number of coils made through the double traverse of the yarn guide.
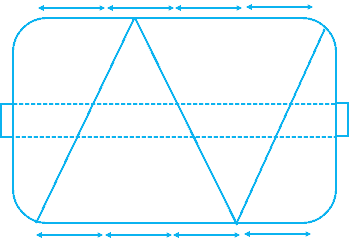
The winding ratio of the above package would be 1.5 because 1.5 coils are formed through a single traverse. Thus, the traverse ratio would be 3.
There are two types of traverse ratios. These are –
Closed Traverse Ratio or Close Wind
This type of cross winding results in “herringbone” or “honeycomb” or “diamond” pattern. It’s formed when the yarn is wrapped pretty close to one another, i.e, the displacement is equal or slightly higher than the yarn diameter.
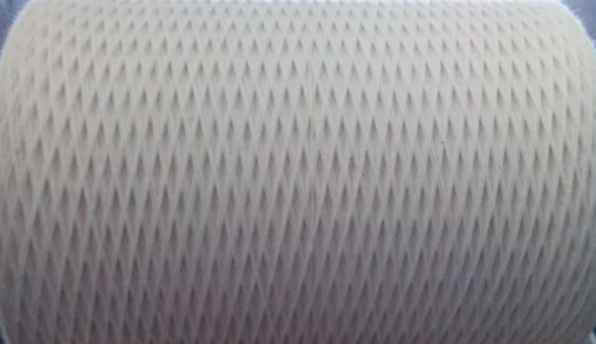
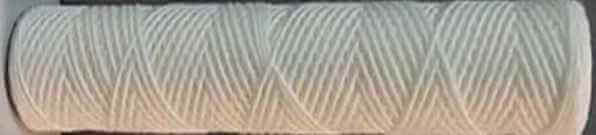
Open Traverse Ratio or open Wind
Here, the traverse ratio is set in a way that the displacement becomes at least 4 times the yarn diameter or higher. These traverse ratios are also called “Actual Traverse Ratio.”
For dyeing applications, open wind traverse ratio is preferred.
Frequently Used Closed Winding Ratio
- 4.990
- 5.4950
- 5.3295
- 5.9990
Frequently Used Open Winding Ratio
- 4.6335
- 5.2900
- 6.4365
- 7.8715
Traverse Length
It’s the easiest terminology to comprehend. The traverse length is the distance that the yarn feeding guide travels for a single traverse. Most of the time, it remains constant. But for pineapple package making (FADIS), the traverse length gradually decreases as the package builds up.
Patterning or Ribboning or Picture Zones
This is one of the most important concepts to understand. Because of this particular defect we needed to invent these other winding technologies. If the yarns keep winding on the same exact positions in the subsequent traverse motions then we call it patterning or ribboning.
The density of material on that portion gets excessively high, which creates problems in dyeing. The liquor can’t be uniformly distributed because of those high-density zones.
Why Does Patterning or Ribboning Occur?
When the traverse ratio (coils per double traverse) is of a whole number (integer), then the yarn keeps winding on the same place. Because at the end of the cycle, there’s no displacement/ gain, so it comes back following the same path.
So, the angular displacement at the end of the traverse or gain is vital to ensure ribboning free package. And to do that we must keep the winding ratio in fractions. However, remember to avoid 0.25 and 0.5, as these also susceptible to patterning.
Types of Winding
If you have read the above sections carefully then you may already have noticed there are 3 winding principals. These are –
- Non-precision Winding
- Precision Winding
- Step-precision/ Digicone (SSM)/ Conotronic (FADIS) Winding
We’ll discuss them one by one. But before getting into that we must get acquainted with two terminologies first that are vital to grasp the concepts.
1. Non-Precision Winding / Random Winding / Drum Winding / Wild Winding
This is one of the oldest winding technologies. Here, the package is rotated through the surface contact of a grooved drum. This grooving provides the traverse motion of the yarn.
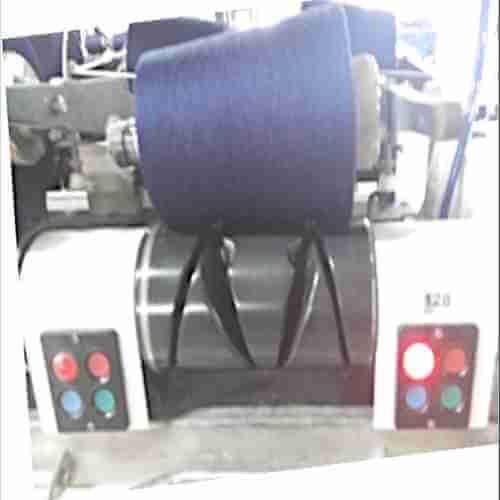
In this mechanism, the drum rotates at a constant RPM. As a result, the package gets the same surface speed but not the RPM. Meaning, at the initial stage, the package RPM and the drum RPM will remain the same, but as the package builds up (i.e., the diameter increases), the RPMof the package will fall.
Now, this eventually leads to an unfortunate event, however. What’s that?
PATTERNING !!!
You see, the grooving on the drum is done to make the winding ratio (no. of coils per double traverse) constant. But as the diameter increases the winding ratio decrease. So, at some point, it’ll get to an integer value. And that is when patterning occurs. It occurs intermittently in random winders.
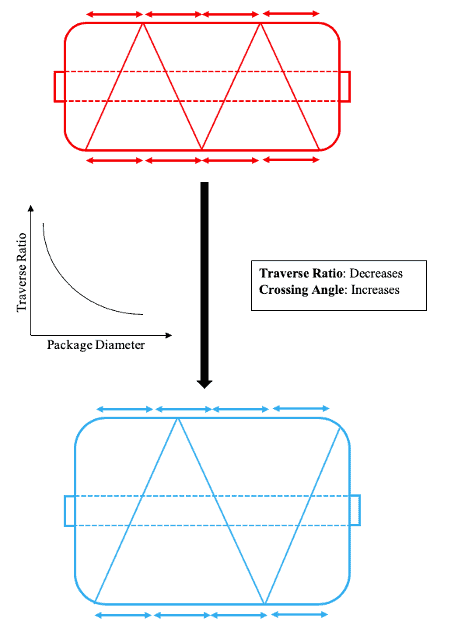
Pros
- Even density
- Pretty stable package
- Offers the production of large packages
Cons
- Prone to patterning or ribboning, creating dyeing and unwinding problems
- Friction drive, thus mostly suitable for spun yarns
- Susceptible to hard edge formation
- Allows slippage
To counter the issue of patterning, manufaturer invented the following two ribbon-free winding techniques.
2. Precision Winding
To counteract the disadvantage of drum winders, manufacturers implemented this system where the winding ratio is kept constant. A fixed and fractional winding ratio gets rid of the patterning issue. However, other issues started to come up.
The mechanism works by varying the RPM of the spindle as the package builds up to adjust its surface speed. It adjusts the surface speed in a way that the winding ratio always remains constant. Meaning, the same number of coils are formed each time the feeding guide moves from one end to another.
Now, as the diameter of the package is increasing, the crossing angle is decreasing. That means the yarns are now pretty close to each other, resulting in an increase of density. This gradual increase in density can create problems in synthetic yarns, especially polyester as those are generally hydrophobic in nature.
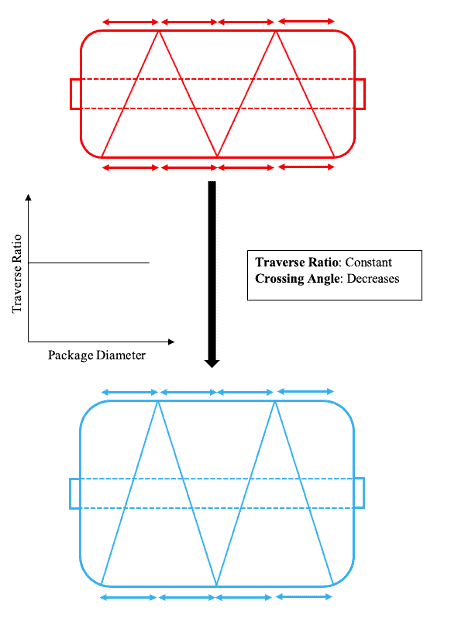
Pros
- Zero patterning
- Suitable for spun yarns
- Winding ratio remains constant
- Excellent unwinding properties
Cons
- Winding angle decrease, so the density in the outer layer increases
- Not the most suitable tecninique for filaments
- Mostly applicable to build small packages as the package tends to get fragile with the increase of diameter
3. Step Precision/ Digicone/ Hybrid/ Conotronic Winding
As you can guess by the name, this is the latest technology. It merges the benefits of both techniques. What do I mean by that?
Well, in this process, we set the crossing angle value because −
As far as I know, there aren’t any soft winding machines available that let the user select the traverse ratio. The value is preset by the manufacturer.
What the machine does is it starts winding with the preset traverse ratio value. Now, we know that the winding angle decreases as the diameter increases. When the angle reduces to a certain extent the traverse ratio will be changed to a new lower value so that the crossing angle gets closer to our set value.
So, for example, if we set a crossing angle value of 14º, the package will start winding at 14º and will maintain a preset winding ratio. But as the package’s diameter increases, the crossing angle will start to decrease. But as soon as, the crossing angle starts to fall too much away from the mean 14º, it’ll set a new lower traverse ratio. In this way, the winding ratio won’t become an integer value at any point.
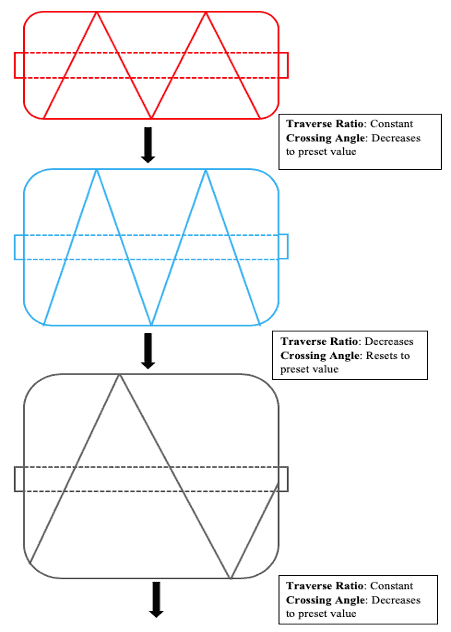
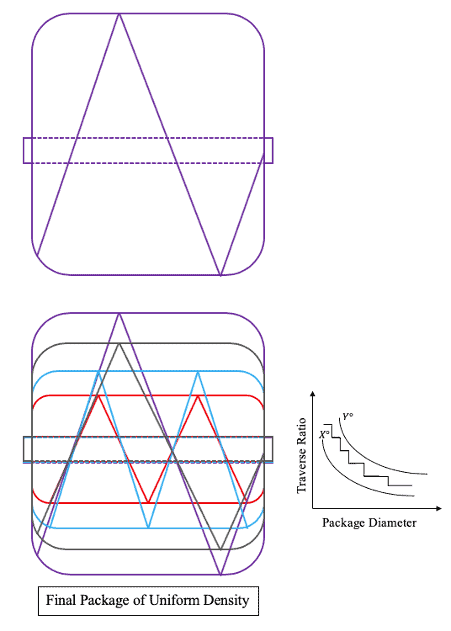
Mechanism of Hybrid or Digicone or Conotronic Winding
As the traverse ratio drops in steps, keeping the crossing angle in a narrow range, it’s called step precision winding.
Pros
- Best system for winding any type of yarn, including synthetic filaments
- No patterning or ribboning
- The layer to layer density of the package remains fairly constant
Cons
- Not any that I know of
Random Winding vs Precision Winding vs Step-Precision Winding
Properties | Random Winding | Precision Winding | Step-Precision or Hybrid Winding |
---|---|---|---|
Crossing Angle | Constant | Decreases | Almost constant |
Winding Ratio | Decreases | Constant | Almost constant |
Package Density | Higher at the patterning zones | Gradually increases | Almost constant |
Mechanism | Pretty straightforward | Slightly complex | Highly complicated |
Which Winding Technique Should You Select?
Among the two techniques (Precision and Digicone), we’ll have to select the one that fits our requirements. Let’s wade through those.
Type of Yarn
Generally speaking, you’ll be better off using the Digicone system for soft winding polyester filaments. The lower angular distance between the filaments can have significant impacts on dyeing. So, avoid precision winding your polyester filament batches to maintain a sufficient angular distance.
Count
Again, coarser yarns occupy more space, thus the Digicone winding technique will be suitable for it as well. You have to remember, the yarns which shrink when wet will increase in diameter. Thus, creating more obstruction of dye liquor.
If your yarn is coarser that 18/1 Ne or it’s a double yarn, go for Digicone. For home use, you can use the best ball winder to do the job.
Frequently Asked Questions
1. Are Hybrid, Digicone, Conotronic are all the same?
YES! The principal is called hybrid winding. But different manufacturers use different names for employing it. ‘Digicone’ is used by the Swiss manufacturer SSM. And ‘Conotronic’ is used by the Italian brand FADIS.
2. What are the defects of soft wound packages?
These are the most common defects of soft winding packages (provided we don’t use random winders) –
- Bulging
- Hard Edges
- Cross-threading
- Sloughing off
- Cauliflower Effect
3. What are hard edges?
Mostly, in drum winders, the yarns stay at the edges at the reversal points for a longer time. This results in more yarn being laid at the edges. Therefore, the density at the edges tends to get higher than the rest of the package, creating hard edges. This problem is attributed to the slowing down and reversal of the yarn guide at the ends of the package.
4. How to prevent hard edges?
The problem can be tackled if the machine has a mechanism for widening the edge area. Typically, it’s achieved by a lateral movement device employed in the winding arrangement where it lets the cradle or the package holder move laterally ever so slightly. We’re talking about mere millimeters here.
Final Words
By now, I hope you’ve got a pretty good grasp on the different yard winding types that are employed in the soft winding and hard winding sections of a yarn dyeing plant. Understanding these principles will let you troubleshoot your dyeing problems faster.
REFERENCES