Straight Knife Cutting Machine (The Most Economic & Popular)
Straight Knife Cutting Machine
Straight Knife Cutting Machine is one of the most popular and versatile machines used in the cutting sections of garment industries around the globe. The machine is pretty much significant to bulk cutting.
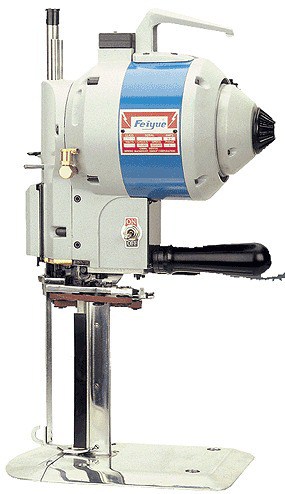
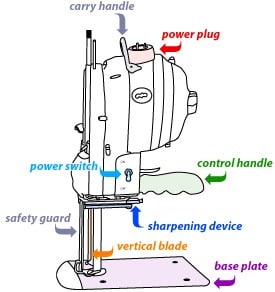
Different Parts of Straight Knife Cutting Machine
Base Plate
The Whole machine stands on it. Usually it has small wheels for easy movement on the cutting table surface.
Upright
It’s the part that carries the straight vertical knife. The knife may have different type of edges (straight, sawn, wavy or serrated) considering the application. A knife guard is also used.
Blade Dimensions
Height: 10-33 cm
Width: 1.5-3 cm
Stroke: 2.5-4.5 cm
Thickness: 0.5 mm
Electric Motor
A motor is there to drive the blade. Overhead cable is used as an important precaution.
Handle
- Transporting handle above the motor; to carry the machine.
- Operating handle underneath the motor; to cut lay accordingly.
Grinder
It sharpens the blade (If required during cutting). Using a continuous abrasive belt gives unique bevel and sharpness.
Power Transmission Mechanism of Straight Knife Cutting Machine
Motor power gives drive to the reciprocating blade. This power is influenced by the height of lay, fabric characteristics, stroke of the blade, and the cutting line curves. Sharp curves causes in the cutting process, as the rear of the blade (backside) presses against the cut fabric plies. A large amount of power transmission requires a big motor, resulting in a heavier machine. And also a tall upright with greater width and increased cross section adds to the constraints of forward motion, while cutting a curve.
Operator power is needed to direct the blade through the lay. Handle height, upright shape, motor weight, blade stroke and sharpness affect the operation. Base plate sliding (by means of rollers) is facilitated using glazed paper below the bottom ply. Great blade movement helps operator to push easily against fabric lays. Not surprisingly, greater movement of blade needs excessive power.
Knife Selection
Usually knife with straight edges are available for cutting. Knitted, synthetic and loose woven fabrics are cut with sharp knife edges, while dense woven and coated fabrics are cut using coarser edges. Wavy edges in knife are introduced to prevent heat generation, and also minimizing fusion while cutting synthetic fabric. Blade strokes can also be changed to reduce fusing. Variable speed machines are used if natural and thermoplastic fabrics are to be cut with a same machine. It also helps in cutting long or tight curves.
Advantages
- High speed of blade provides large production.
- Easy maintenance.
- Portable and cheap.
- Reasonable accuracy of cutting on curves and sharp corners.
- Fabric can be cut from any angle.
- About 70 percent length of the cutting blade can be utilized.
Is a Straight Knife Cutting Machine Suitable for Creating Different Types of Sewing Stitches?
Yes, a straight knife cutting machine is suitable for creating different types of sewing stitches. It can efficiently cut various types of fabric and materials to produce a wide range of sewing stitches, making it a versatile tool for creating unique and intricate designs.
Disadvantages
Cutting with higher speed causes in the process as knife deflection occurs. It can be prevented with a reduced lay height. Fabric characteristics, skilled labor and motor weight are also concerned. Accidents are very often occurrence while cutting with straight knife cutting machine.
Reference:
The Clothing Manufacturing (Harrold Carr and Letham Barbara)