Outlier Bobbins: Causes & Possible Solutions
A noteworthy contrast between spinning factories and other industrial processes is the number of production positions. The majority of the well-renowned ring spinning factories have more or less 1 lac ring spindles in addition to cards, draw frames, combers, simplex, and winding machines. Along these lines, there is a high likelihood that spinning mills create countless bobbins each day having some variations among themselves.
What is Outlier Bobbin?
We may portray a bobbin as outlier that surpasses one or a few resistance limits as for hairiness, imperfections, evenness, foreign fibers, and so forth. The explanations behind outliers are generation positions which are defective or shattered, mixed up of bobbins in the spinning procedure, contaminated crude material, and so on.
Furthermore, we can consider a bobbin as an outlier when the yarn of the bobbin is converted into a woven or knitted fabric and imperfections either in grey fabric or after dyeing can be detected by the naked human eye. The quality features of these outliers deviate from the acceptance limit, all through the bobbin, and may as well lead to production difficulties in later processes.
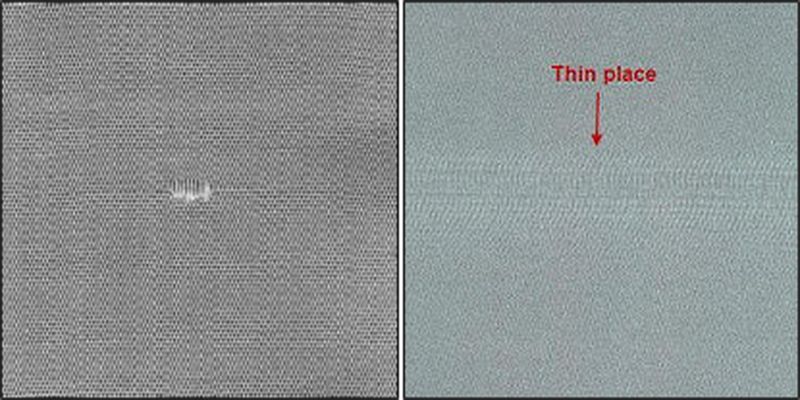
How Outlier Bobbin Generates?
A ring spinning factory or mill is different from numerous other factories due to the large number of production positions. In order to yield up to 20 tons of yarn every day, the prerequisite is to set up around 30’000 ring spinning positions that are functioned 24 hours every day, i.e., all day long and all 7 days in the week. The day-to-day production amount relies very much on the average yarn count produced.
For that reason, the possibility of having damaged or malfunctioning machine parts like carding clothes and wires, draw box rollers, plastic or metal travelers, ring spindles, etc., that lead to the generation of outlier bobbins to a great extent.
If a single thread crosses the acceptance limits in the weaving or knitting process, it can cause the whole fabric to be viewed as defected. For that reason, there is a significant awareness in every spinning mills to spot those bobbins and to exclude them from being processed.
Almost every ring spinning factories possess around 25,000 to 1 lac ring spindles. Besides, carding machines for neps removal and fiber individualization. A couple of drawing frames for hook straightening, doubling and drafting for better sliver evenness. Comber for short fiber removal, simplex for producing roving and winding machines for processing cone packages.
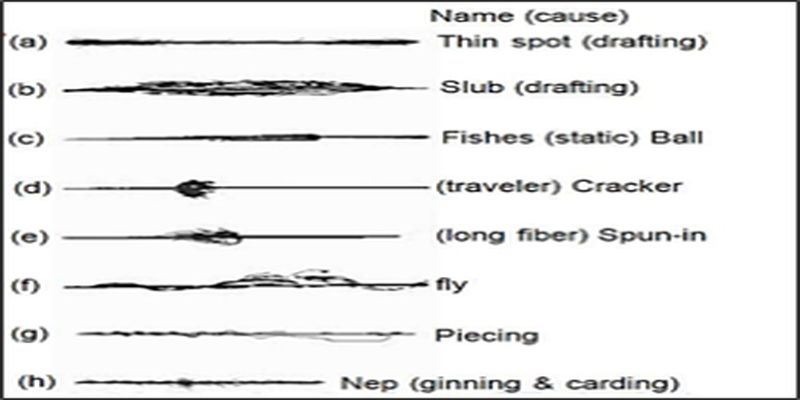
Reasons
Hence, there is a greater chance that a substantial quantity of outlier bobbins are manufactured every day. The ins and outs for outliers are numerous manufacture positions that are faulty or damaged out, mixing up of bobbins for the duration of the spinning progression or impure raw materials, etc.
Nevertheless, in a spinning factory with 26 ring spinning frames, there are 25 frames that deliver unidentifiable outlier bobbins to the testing lab via the winding machine at a definite date. If there is a task in the factory that what sort of bobbins were treated on which winding frames, it also permits the task of the type of problems at least to a precise ring frame.
So, if a spinning factory practices link methods, the back tracing of the outliers to the ring frame is a very easy task. In spinning factories with separate winding machines, it is dependent on the management of the mill.
How to Overcome Outlier Bobbins?
Hence, to boost up in the acknowledgment of outlier bobbins, the aptitudes of on-line and off-line methods need to be combined. The subsequent tables demonstrate the characteristics of off-line and on-line methods.
Off-line
- Sample Testing
- High Reproducibility
- High Accuracy
- Interlaboratory Comparison
- Comparison with Benchmarks
On-line
- 100% Monitoring
- Detection & Elimination of Seldom-occurring Events
- Enormous Amount of Data
- Sound Statistical Platform
- Trend Analysis
At the time of practicing on-line methods for the quantity of 100% of all bobbins, we need to differentiate the following:
- There are more or less infrequent, or random occurring yarn faults that are existent in a fabric, and that should be removed with a yarn eye clearer on the winding frame.
- There are a few degradation of quality features of a bobbin that can significantly lessen the quality of the fabric, and that alarms the complete bobbin.
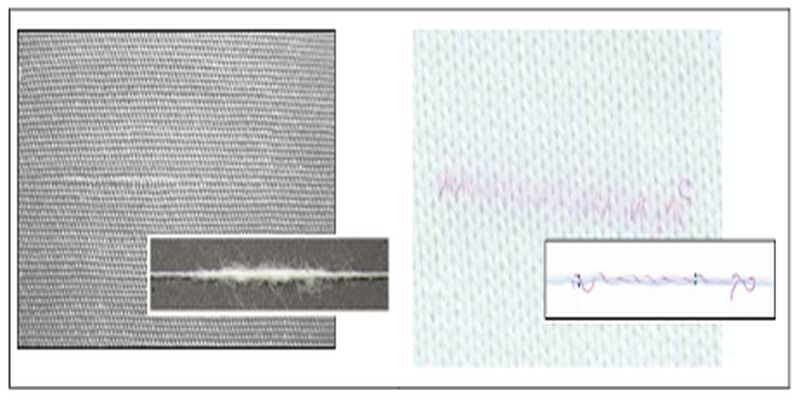
We must omit the alarming faults on the winding frame. On the other hand, a splice joins every single cut in the winding frame. The quantity of cuts in every 100 km differs in the yarn manufacturing in the middle of 10 and 70 for all of the above-stated yarn faults.
Remedies for Outlier Bobbins
Bobbins that possess quality complications such as higher irregularities, higher amounts of thick or thin- places, extreme hairiness, periodic faults, extraordinary cut rates, have to be banished at the winding machine since these substandard quality features exist all through the bobbin.
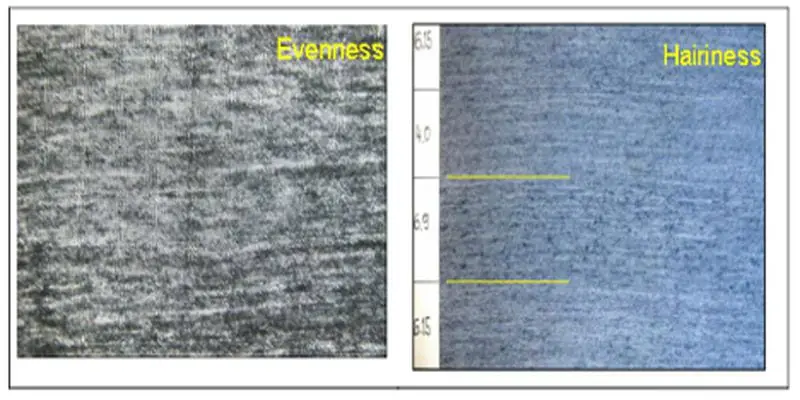
The yarn eye clearer possesses the capability of determining irregularities, thick-thin places, hairiness, neps, etc., and, which is why it can isolate the bobbins with extreme quality variations.
The subsequent image signifies on a historical impression the varieties of alarming faults can be modified directly on the winding frame since they are random occurring incidents.
We can identify the bobbins of below-average quality characteristics. Subsequently, we may separate these bobbins from the lot at the winding frame.
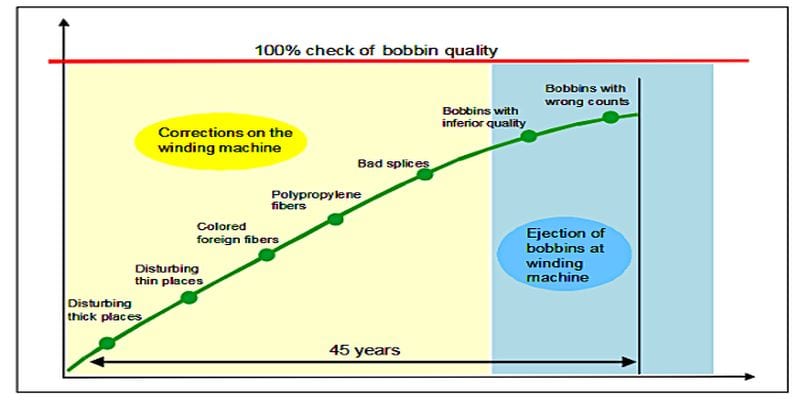
Bobbins that surpass the certain thresholds of quality features have to be taken out of the winding frame. For this persistence, a state-of-the-art yarn clearer detects the following features:
- Irregularities/ Unevenness %
- Repeated thin places
- Repeated thick places
- Regular and irregular neps count
- Yarn hairiness
- Periodic faults
- Unnecessary cuts
- Clusters of irregularities
A Dedicated Maintenance Team
Hence, a well-efficient spinning factory comprises a maintenance department and repair squad that progressively recovers outliers among the manufacturing positions.
The repair squad, however, requires involvement from the laboratory staff. They prepare a systematic quality investigation. The subsequent image demonstrates the principles of operation in a state-of-the-art spinning factory.
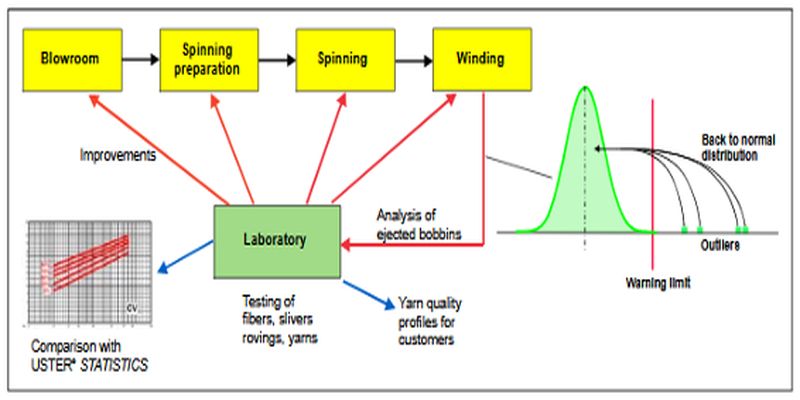
They label the bobbins of different spinning frames. This helps to detect the manufacturing positions where the ejected bobbins originated from. They transport the ejected bobbins to the yarn quality laboratory. Hence, they asses the quality complications. Furthermore, they write down the findings on an order sheet for the repair squad as well. The aim is to bring back the outlier bobbins into the normal distribution.
Winding frame is the bottom last machine in the spinning progression. The speed of winding is precisely high as much as up to 1600 m/min. It is sensible to look after the yarn on the winding frame to lessen the number of cuts. If number of cuts are higher then winding frame will eject the outlier bobbins.
Plotting the Data in a Bell Curve
Quality features, for example- the unevenness, the imperfections (thick place, thin place, and neps), the amount of hairiness, have a “natural” difference that can be denoted by a bell curve. Outlier bobbins have quality characteristics that are significantly beyond the boundaries of the bell curve. As a result, they fixed a warning limit to distinct the borderline between regular and outlier bobbins.
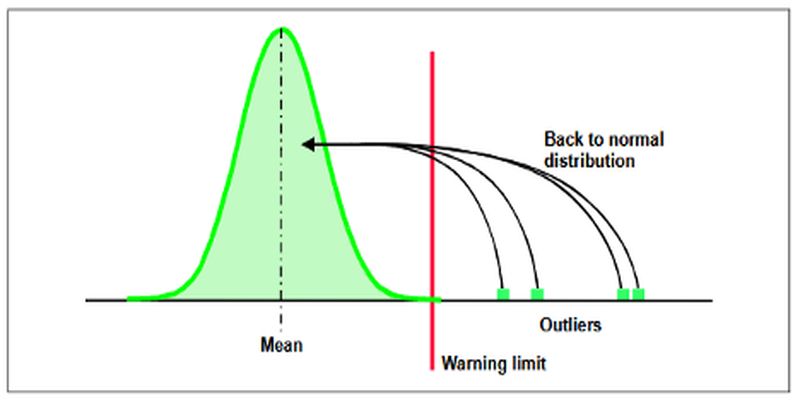
Final Thoughts
The immense mainstream spinning mills have a built-up quality administration framework dependent on sample testing. With such a quality framework, be that as it may, it might take one year or more to dispose of outliers.
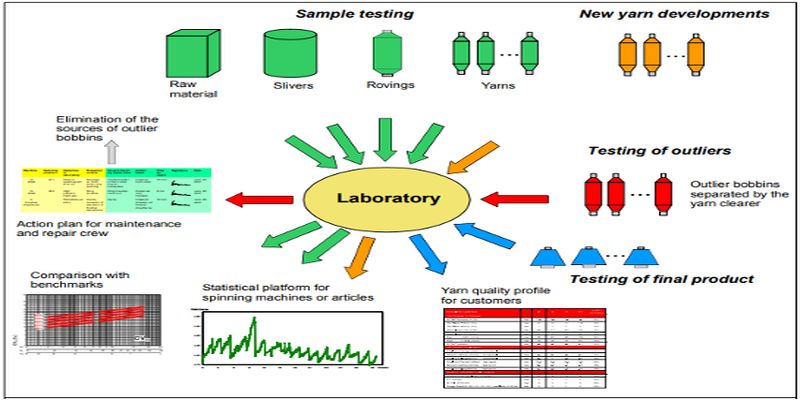
Frequently Asked Questions
1. Why is it important to identify outlier bobbins?
Outlier bobbins are those that has past the quality threshold or acceptance limit. The presence of outlier bobbin in weaving or knitting, generates multiple defects in the grey fabric. It is also responsible for the imperfections after dyeing and printing. Besides, those faults are effortlessly noticeable through the naked human eye.
2. Is it possible to manufacture completely outliers’ free bobbins?
Well, despite proper maintenance, this is really tough and practically almost impossible to produce such bobbins entirely free of outliers. There is huge quantity of production positions in the ring frame. This is a major hindrance to achieve outliers’ free bobbins. That is why the probability of a minimum fraction of outliers will always be present in the ring frame is extremely high.
3. What is the role of the winding machine to identify the outliers?
Winding machine is the very last machine of the spinning process. It can detect the faults regarding the quality parameters of the bobbins. For example, some common faults of ring bobbins are – unevenness, thick places, thin places, neps, hairiness and other mass variations. Winding machine’s electronic yarn clearer device can easily detect these faults. That is how it can isolate the outliers out of the regular bobbins.
References:
Management of outlier bobbins in ring spinning mills – Uster