Nonwoven Meaning | Woven vs Nonwoven | Nonwoven Manufacturing Process
What is Nonwoven?
No definition of nonwoven is internationally agreed upon. International Standards Organization (ISO) and the Americal Society for Testing Materials had given two important definitions.
According to ISO 9092:1988 –
“A manufactured sheet, web or batt of directionally or randomly orientated fibers, bonded by friction, and/or cohesion and/or adhesion, excluding paper and products which are woven, knitted, tufted, stitch-bonded incorporating binding yarns or filaments, or felted by wet-milling, whether or not additionally needled. The fibers may be of natural or man-made origin.”
This definition is very narrow in its scope. Now, let’s look at the definition according to ASTM D 1117-80 –
“A nonwoven is a textile structure produced by the bonding or interlocking of fibers, or both, accomplished by mechanical, chemical, thermal or solvent means and combinations thereof. The term does not include paper or fabrics that are woven, knitted, or tufted.”
Examples of Nonwoven
Some most common nonwovens are surgical masks, tea-bags, bath-wipes, wound dressings, face-cloths, etc.
Classification of Non woven Fabric
Several types of nonwoven are available according to their manufacturing process.
- Spunlaid
- Drylaid
- Wetlaid
- Airlaid
- Heat bonded
- Melt blown
- Stitch
- Acupuncture/ Needle punched
What Are the Advantages of Nonwoven Manufacturing?
The main perk of manufacturing nonwoven is that the process is a continuous one. It starts from the raw materials and ends in the finished fabric without any interruptions. So, no material handling is required resulting in low labor and manufacturing cost.
Mass production with a vast range of fiber properties is possible. The annual increase in the production rate of nonwoven is 10%.
Manufacturing Process of Nonwoven
There are many processes for manufacturing nonwovens. One of them is the melt blown process.
Melt Blown Process for Producing Melblown Nonwoven Fabric
In this process, very fine fibers can be produced at very high production rates without using spinneret.
The Melt Blown process was first introduced in the 1950s but became very popular in 1975. The annual growth of the process is 10%.
Here are the steps to this process:
- First, the polymer is melted and introduced to the polymer hopper. The extrusion happens in a usual way but through a relatively large extrusion hole.
- A high-speed stream of hot air is introduced to the polymer after it passes the extrusion holes. Sometimes the air temperature is above the melting point of the polymer.
- The introduction of cold air solidifies the polymer. Some drawing takes place depending on the velocity of the air.
- During the process, the filaments break into staple fibers.
- The staple fibers then collected into a batt with the help of air-suction.
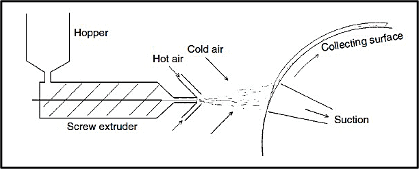
As the fiber used in this process is extremely fine, the contacts among the fiber are more, and the integrity of the batt is greater.
In the manufacturing of nonwoven, knowing what is web and batt is very important.
What is web and batt?
A thin layer of fibers is known as the web, and several lays of webs on top of each other are known as the batt. The first stage in nonwoven production is called batt production.
Needle Punched Nonwoven
One very important nonwoven is ‘Needle Punched Nonwoven.’ The bonding among the fibers is dependent on mechanical bonding, i.e., frictional forces and fiber entanglements. The process is called ‘Needle Punching’ or ‘Needle Felting.’
Manufacturing Process of Needle Punched Nonwoven
The manufacturing process of needle punched nonwoven is briefly discussed below. Take a look –
- Firstly, the batt is placed between two stationary plates known as the bed and stripper plates.
- A large number of the needle penetrates through the batt (almost 4000 needles per meter width of the machine). Some fiber gets caught by the needles during the penetration and pulled through other fibers.
- The loops generated among the fibers remain in their position when the needles go upward.
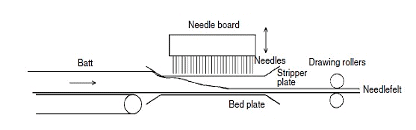
The whole process takes place in the needle loom. Several types of needle looms are available depending on the position of the needles.
- Up-punch needle loom- Pushes the fiber upwards
- Downpunch needle loom- Pushes the fiber downwards
- Combination of both
- Double-punch needle loom- One board punches up, and another punches down ta the same time.
A particular type of needle called a barbed needle is used. They are triangular in shapes, and barbs are cut in the three edges of the needle.
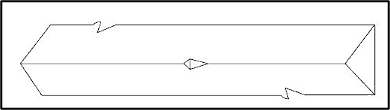
Important Parameters for the Manufacture of Needle Punched Nonwoven
The shape and the holes present in the nonwovens depends on:
- Number of needles in the needle board
- Size of the needles
- Advances of the needle after each stroke
- Punching density
- Fiber type.
The density of the webs depends on the feed rate.
- A higher feed rate produces a thick and dense web, which limits permeability in the final product.
How Can Biomimetics in Textiles Influence Nonwoven Manufacturing Processes?
Exploring biomimetic innovations in textile design can revolutionize nonwoven manufacturing processes by mimicking nature’s efficiencies. Techniques inspired by natural structures enhance durability and performance, leading to eco-friendly materials. This approach not only reduces waste but also improves the functionality and versatility of nonwoven fabrics, paving the way for sustainable production practices.
What Are the Uses of Needle-Punched Nonwoven?
Needle punched nonwoven has a high breaking tenacity and tear strength. But, as they have a low modulus and a poor extension recovery, they are only used in reinforcements where extension control is necessary.
They are widely used in air, gas, and water filtration. The best fabric pots are often constructed with this type of non-wovens. They are also used in geotextiles to remove water rather than reinforcements.
Home and commercial carpeting is another scope of use for needle punched nonwoven. You’ll see these used as the best fabric for quilt backing as well.
Comment les propriétés des matériaux non tissés influencent-elles leur utilisation en tant que géotextiles ?
Les propriétés des matériaux non tissés jouent un rôle clé dans leur utilisation en tant que géotextiles. En raison de leur perméabilité, résistance et durabilité, ces matériaux sont adaptés à diverses applications, telles que le drainage et le contrôle de l’érosion. Les différents types et propriétés des géotextiles expliqués permettent ainsi de choisir la solution optimale pour chaque projet.
Frequently Asked Questions
1. What are the raw materials for nonwoven?
Mainly Polypropylene, polyethylene, and Polyester are used for producing nonwoven.
2. Where are nonwoven fabrics used?
Nonwovens are used in places where some specific functions such as absorbency, water repellency, stretch, softness, strength, washability, thermal insulation, filtration, etc. are required. Due to its heat resistance properties, it’s often regarded as the best batting for potholders.
3. Are nonwoven fabrics environment friendly?
Yes, they are environment friendly. Nonwovens naturally decompose without any residue, and they are not toxic. So they don’t harm the environment. The life span of nonwovens is only 90 days, and it decomposes in 5 years in outside.
4. Are nonwovens washable and breathable?
Nonwovens are washable, and they are a breathable alternative to the tight woven fabrics.
5. What is the main advantage of nonwoven over woven fabrics?
When compared with woven fabrics, nonwoven are homogeneous. The whole area of the nonwoven can be used for filtration, while in woven fabrics, the flow of water is stopped by the yarn.
REFERENCE
Handbook of Technical Textiles by A.R. Horrocks and S.C. Anand