3D Textile | 3D Textile Design | 3D Textile Techniques
One of the recent innovations in the field of textiles is ‘3D Textiles’. Generally, all the textile material have an internal 3d structure. However, as they are practically used as a single layer, planer, or cylindrical 2d sheets, they are not called 3D Textile. 3D Textiles, however, push beyond traditional boundaries by incorporating volumetric designs and structures that enhance functionality and aesthetic appeal. Inspired by the principles of biomimetic design, these textiles mimic natural forms and processes, enabling advancements in strength, flexibility, and adaptability. This innovation opens new possibilities in industries ranging from fashion to aerospace engineering.
What Are 3D Textile?
When a single layer material has an overall shape, or a solid planer material has multiple layers, or a solid multilayer material has a 3D shape, then they are called ‘3D Textile’. Multi-layer hollow materials are also included in this category.
Types of 3D Textile Design
Among the many varieties of 3D textiles, we found the following ones to be more widely used. Take a look–
3D Woven Textiles
There is no exact definition. Woven 3D textiles require interlacing in the X and Y axis along with the Z-axis. They have yarns crossing in three of those mutually perpendicular directions (X, Y, and Z).
3D woven textiles need a dual-directional shedding system. The warp yarn moves up and down as well as side to side. The movement is required for the interlacement with through-the-thickness yarns.
Specially manufactured weaving machine is required. The designing of the weave is complicated than conventional weaving. A program named ‘Weave Engineer’ by TexEng Limited made the designing steps easy.
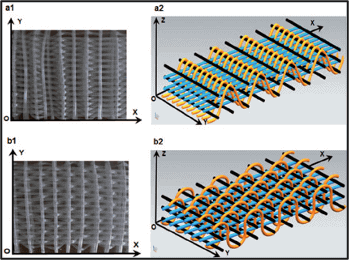
3D Braids
Braids are complex structures where single layers of yarns are diagonally interlaced. The movement of the packages around each other is done by ‘Horn gears.’ There is a limitation of using horn gear. The solid braiding process can not achieve versatility.
Four-step braiding can solve the problem by controlling the movement of carriages with the help of a computer.
Although braiding gives a lot of versatility, it has some limitations too. If the size of the product is large, the movement of packages around one another becomes slow. Also, large, braiding machines are necessary.
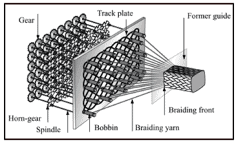
3D Knit Structures
- Complex integral shapes are possible by the computer controlling weft knitting machines. This process is used in making complete garments without sewing different parts of the garments separately. Mechanical performance in weft knitting is slow as the yarns repeatedly change direction over short periods.
- Spacer fabric is another type of 3D knit. Threads crossing between two knit layers link them.
In warp knitting, multi-axial structures can be produced. The structure is held together by knitted binder yarns.
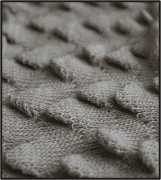
Non-Woven 3D Textile
Several types of 3D non-wovens are available –
- High bulk flat non-wovens: It can be produced by –
- Cross-laying of multiple horizontal layers (Uniform effect).
- Vertically folding the layers (More 3D effect).
- Needling which causes spacer fibers to bridge a gap between two web layers.
- Non-woven 3D shapes
- Electrospinning nanofiber
Other 3D Textile Techniques
Here are some other form of 3D clothing techniques –
False Interlacing
False interlacing is a comparatively easy mechanism of producing 3D materials. If the movement of yarn packages are reversed in pairs during interlacing, false interlacing occurs.
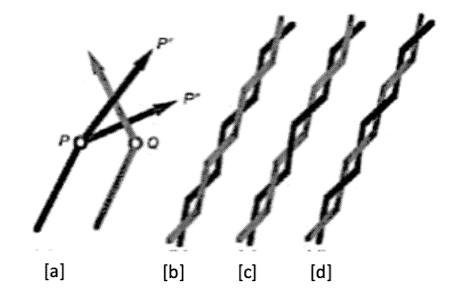
Interlacing by Crossing Yarns –
[a] Over & Under Crossing
[b] One Yarn Over, Other Yarn Under
[c] Alternating Over & Under Sections
[d] Alternating Over & Under at Each Crossing
Spiderweb
Here, yarns are laid down on one another and then bonded hypersonically.
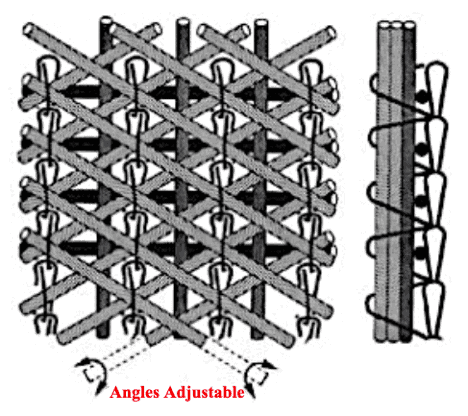
Stitched and Embroidered
Previously, 3D garments were made by stitching two layers of fabric in interlocked 3D loops. According to the requirements, pieces are cut and sewn together.
Elaborate stitching is sewn into the base fabric in decorative embroidery. The base structure is dissolved away when a free-standing 3D structure is made.
Draping and Press-Forming
Non-woven fabric is placed between two surfaces of a mould and then followed by pressing to make 3D fabric.
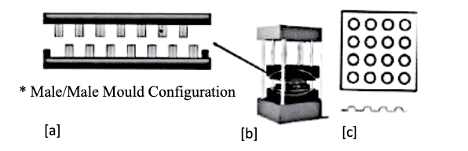
Here,
[a] Mould; [b] Press-Forming; [c] Resulting Shape
How Can 3D Textile Techniques Be Utilized in Creating Fabric Pots?
When it comes to the best fabric pots buying, considering 3D textile techniques can elevate the quality and functionality of fabric pots. Utilizing 3D textile techniques allows for the creation of innovative designs that provide better support, durability, and flexibility, making them ideal for planting and gardening purposes.
How Can 3D Textile Techniques Be Inspired by Biomimetics?
Biomimetic principles in textile engineering drive innovation by mimicking nature’s designs to create advanced 3D textile techniques. From the intricate structure of spider silk to the strength of seashell layers, these principles inspire sustainable, lightweight, and durable fabrics that revolutionize industries such as fashion, healthcare, and aerospace. Nature becomes design’s ultimate blueprint.
What Are the Uses of 3D Textiles?
The 3D textiles are used for both functional and aesthetic purposes. Oftentimes, 3D textiles are designed through biomimetics. Their application ranges from shorts shoes to helicopter blades. Take a look at some of the most pronounced areas of 3D textile applications –
- Aerospace, Automobile, and Military application: Gas turbine fan blades, stingers, Helicopter rotor blades, Military vehicle protection, etc.
- Sport and Leisure application: Sport shoes, underwear, outwear, golf-club, etc.
- Medical application: Double velour vascular graft, scaffolds, wound dressing, tissue engineering, ulcer management, etc.
- Protection application: Soft body armor, helmets, limb protectors, protective panels in vehicles, etc.
- Filtration: Gas and liquid filtration.
- Papermaking: Supporting the paper during hot air supply.
- Geotextile: Separation and filtration purpose.
- Construction: Temporary bridges, floorboard, protective side panels, main framework, and cladding of buildings.
REFERENCE