Influential Properties of Cotton Fiber in Spinning
Cotton is a natural cellulosic fiber that produces a variety of yarn due to its diversified end-use. On the basis of different end-use, cotton fiber is selected for spinning keeping in mind its different quality parameters. To produce a standard quality cotton yarn the fiber should have the following properties in an optimum level. The most important characteristics considered for the fiber are:
- Fiber fineness
- Staple length
- Fiber strength
- Length uniformity
- Fiber maturity
- Color grade
- Fiber cleanness
- Elongation
- Moisture
1. Fiber Fineness
Fiber fineness is the supreme consideration that governs the yarn eminence. Fineness limits the numerical amount of fibers that exist in the cross-section of yarn. Supplementary fiber in the cross-section offers not only superfluous strength but also an enhanced fiber distribution in the yarn. At least thirty fibers are necessary in the yarn cross-section, but there are typically over 100 for almost every spinning system available.
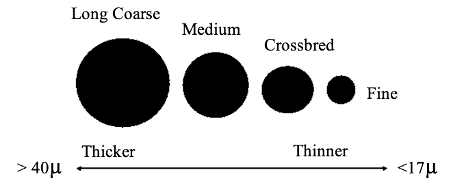
Fiber Fineness Influences
If fineness increases then,
- Spinning limit increases
- Yarn strength increases
- Yarn evenness increases
- Drape of the fabric increases
- Lusture increases
- Handle increases
- Productivity increases
What is MIC Value?
For cotton, fiber fineness is quantified by MIC value or Micronaire value (microgram/inch). It indicates the average mass of per inch the fiber in microgram. As the value of MIC gets higher the fiber gets finer. This is more like a direct count measuring method. The fineness scale is as follows:
Micronaire (MIC) | Fineness |
---|---|
Bellow 3.0 | Very Fine |
3.1-3.9 | Fine |
4.0-4.9 | Medium |
5.0-5.9 | Coarse |
Above 6.0 | Very Coarse |
2. Staple Length
One of the utmost significant characteristics of cotton is fiber length. It defines the maximum spinning limit of the fiber. The run-of-the-mill length or the mean length of fiber ready for spinning is said to be the staple length. Staple length determines the ultimate quality, maximum count and tenacity of yarn.
If fiber length rise then,
- Spinning limit increases
- Yarn strength increases
- Yarn evenness increases
- Hand feel of the end product increases
- Lusture increases
- Yarn hairiness decreases
- Productivity increases
Fiber Type | Length in Inch | Length in mm |
---|---|---|
Short Staple – SS | 1 inch or below | 25mm or below |
Medium Staple – MS | 1 1/32-1 4/32 inch | 26mm – 28mm |
Long Staple – LS | 1 5/32-1 12/32 inch | 29mm – 35mm |
Extra-long Staple – ELS | 1 13/32 inch & above | 36mm & above |
3. Fiber Strength
- Robustness of fiber has an undeviating consequence on yarn and its fabric tensile strength.
- When the fiber strength improved then yarn and fabric strength amplified.
- Very fragile cottons tend to falling-out throughout processing both in blow room (while expose to beater) and carding generating short fibers and consequently decrease yarn strength and consistency.
- Bottom strength for textile fabric is approximately 6 cN/Tex (about 6 Km breaking strength)
- A few examples of breaking strength: (in cN/Tex)
Cotton 16 – 41
Wool 13– 19
Polyester 32 – 59
- In relation to cotton, the strength of fiber bundle is dignified and stated as the Pressley Index (PI) and PSI (Pounds per Square Inch).
Pressley index (PI) = Breaking load (lbs) ÷ Bundle weight (mg)
The following scale of PI value is used:
PI Value | Grade |
---|---|
Below 70 | Weak |
70 – 74 | Fairly Strong |
75 – 80 | Medium Strong |
81 – 86 | Strong |
87 – 92 | Very Strong |
93 And Above | Excellent |
4. Length Uniformity
If length uniformity increases then,
- Yarn irregularity decreases
- Ends down decreases
- High wastage in combing decreases
- High fly liberation and machine contamination in spinning, weaving and knitting decreases
There are two popular measures of length uniformity in a cotton sample:
- Uniformity Ratio (UR) and
- Uniformity Index (UI)
These two can be denoted as following
Uniformity Ratio, UR = (50% Span Length ÷ 2.5% Span Length) x 100
UR range is 75% -85%
Uniformity Index, UI = (Mean Length ÷ Upper Half Mean Length) x 100
UI range is 40% -50%
5. Fiber Maturity
The maturity of cotton is distinct in terms of the progress of cell wall thickness. An entirely matured fiber has a well-developed thick cell wall. On the other hand, an immature fiber has comparatively thin cell wall. If the moisture swollen fiber’s cell wall represents 50% – 80% of its round cross section then the fiber is to be denoted as mature fiber. The fiber is to be considered as immature when it epitomizes 30% – 45% and as dead when it symbolizes not as much of its 25%.
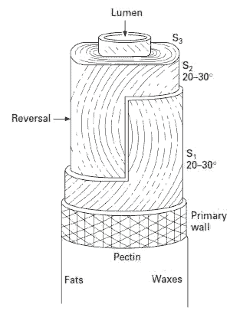
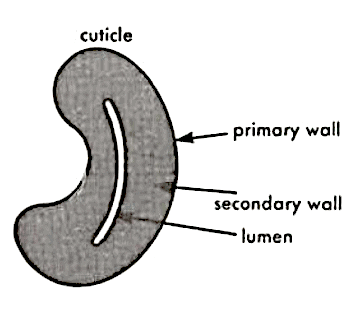
Immature fibers lead to –
- Deterioration of yarn strength
- Neppiness (neps)
- Erratic dye ability
- Greater share of short fibers
- Handling difficulties mostly arise at the carding
- Low dye adsorption whereas mature fiber shows higher adsorption of dye
Maturity is expressed as Maturity Ratio.
Maturity Ratio = {(N-D) ÷ 200} + 0.7
Where, N = Normal (mature) fiber and D = Dead fiber.
This equation is known as Lord’s equation.
The grading of maturity ratio is:
Maturity Ratio | Grade |
---|---|
0.86 | Good |
0.75 | Average |
.65 | Poor |
6. Color Grade
Color grade denotes the amount of the reflectance (Rd) and the yellowness (+b) of cotton fibers. Reflectance (Rd) refers to the whiteness of the light that is imitated by the cotton fibers and (+b) states the yellowness of the light that is replicated by the cotton fibers.
Classer’s Designation for Reflectance |
Classer’s Designation for Yellowness |
||||
White |
Light Spotted |
Spotted |
Tinged | Yellow Stained | |
Good Middling |
11* |
12 |
13 |
– |
– |
Strict Middling |
21* |
22 |
23* |
24 |
25 |
Middling |
31* |
32 |
33* |
34* |
35 |
Strict Low Middling |
41* |
42 |
43* |
44* |
– |
Low Middling |
51* |
52 |
53* |
54* |
– |
Strict Good Ordinary |
61* |
62 |
63* |
– |
– |
Good Ordinary |
71* |
– |
– |
– |
– |
Below Grade |
81* |
82 |
83 |
84 |
85 |
* stands for quantitative standards, while the others are qualitative standards
7. Fiber Cleanness
A bale of cotton contains not only the fresh cotton fibers but also provides a certain amount of impurities. In addition to operating fibers, cotton stock encloses foreign matter of numerous kinds. A list of impurities is provided here that is mostly found in cotton bale (Not in the garden-fresh fiber).
Vegetable Matter
- Husk portions
- Seed wreckage
- Steam remains
- Leaf fragments
- Wood trashes
Mineral Matter
- Earth
- Sand
- Dust
- Coal
Other Foreign Matter
- Metallic
- Dry goods fragments
- Storing material
- Cloth particles
- Packing elements
8. Elongation
Elongation is a quantity of the elastic performance of the fibers in the bundle. The stretched length of fibers right before they breakdown is said to be as its elongation percentage.
Elongation % | Grade |
---|---|
Less than 5% | Very low |
5% – 5.8% | Low |
5.9% – 6.7% | Medium |
6.8% – 7.6% | High |
Above 7.6% | Very high. |
9. Moisture
Moisture is the proportion of water that is existent in the sample. It fluctuates in the cotton with relative humidity, time, temperature and previous history of the fiber. The moisture content of cotton fiber is 7.5% and moisture regain is 8.5%.
Moisture Content | Grade |
---|---|
Below 4.5 | Very low |
4.5-6.5 | Low |
6.5-8.0 | Medium |
8.0-10.0 | High |
10.0 and above | Very high |
Frequently Asked Questions
1. Fiber contains numerous qualities. Which one of them should be prioritized?
Fiber possess a lot of properties. The end use of the product determines its selection for spinning. For cotton fiber fineness and length is the most significant criteria. Besides, moisture, trash content and elongation comes as well.
2. What is the differences between moisture content and moisture regain?
The moisture content stands for the quantity of water exist in the fiber as a percentage of sum of weight of the fiber. Whereas, moisture regain denotes the extent of water exist in the fiber as a proportion of its oven dry weight. That is why the value of moisture regain is always higher than the moisture content.
For cotton, moisture regain is 8.5 whereas moisture content is 7.5
3. What is the difference between short fiber and short staple fiber?
Normally a fiber is to be counted as short fiber if its length is below 12.5 mm. The fibers which are removed in combing are also known as short fiber or noil. But, short staple fibers are those whose length is 12.5 mm to 25 mm.[/av_textblock]